High Pressure Chemical Reactor for Sale
ZZKD manufactures durable, high-quality high pressure chemical reactor and has been selling them to customers worldwide for over 33 years. ZZKD offers CE certified high pressure chemical reactor to help you grow your business and obtain accurate reaction data. You will be satisfied with the performance of your ZZKD high pressure chemical reactor because we use well-known brand components to build your high pressure chemical reactor.
Model: CF-1
Capacity (L): 1
Pressure (MPa): 22
Application Range: Application Range: Ideal for small-scale high-pressure reactions and catalyst testing in laboratory settings.
Model: CF-5
Capacity (L): 5
Pressure (MPa): 10
Application Range: Well-suited for medium-scale high-pressure reactions and research applications in laboratory settings.
Model: CF-20
Capacity (L): 20
Pressure (MPa): 22
Application Range: Tailored for large-scale high-pressure reactions, pilot plant studies, and chemical process development in laboratory and industrial settings.
Model: FCF-0.5
Capacity (L): 0.5
Pressure (MPa): 22
Temperature (°C): 350
Stirring Speed (r/min): 50-1000
Heating Power (kW): 1.5
Application Range: Ideal for high-pressure and high-temperature reactions in laboratory settings.
Model: FCF-1
Capacity (L): 1
Pressure (MPa): 22
Temperature (°C): 350
Stirring Speed (r/min): 50-1000
Heating Power (kW): 1.5
Application Range: Ideal for high-pressure and high-temperature reactions in laboratory settings.
Model: FCF-10
Capacity (L): 10
Pressure (MPa): 22
Temperature (°C): 350
Stirring Speed (r/min): 50-600
Heating Power (kW): 7
Application Range: Suitable for high-pressure and high-temperature reactions in laboratory settings.
Model: FCF-50
Capacity (L): 50
Pressure (MPa): 10
Temperature (°C): 300
Stirring Speed (r/min): 50-600
Heating Power (kW): 12
Application Range: Suitable for high-pressure and high-temperature reactions in laboratory settings.
Model: FCF-100
Capacity (L): 100
Pressure (MPa): 6
Temperature (°C): 300
Stirring Speed (r/min): 50-600
Heating Power (kW): 14
Application Range: Suitable for high-pressure and high-temperature reactions in laboratory settings.
Model: TGYF-B
Capacity (ML): 50-500
Pressure (MPa): 22
Temperature (°C): 350
Stirring Speed (r/min): 0-1800
Heating Power (kW): Variable
Application Range: Designed for various high-pressure and high-temperature stirring applications in laboratory settings.
Application
High pressure reactors facilitate controlled synthesis of compounds, catalytic research, and pharmaceutical development by providing precise pressure conditions for reactions, optimizing yields, and enhancing product purity in various industries.
Chemical Synthesis
High pressure reactors play a crucial role in chemical synthesis by providing controlled environments under elevated pressures. This enables the synthesis of complex compounds and polymers with improved reaction kinetics and higher yields compared to conventional methods.

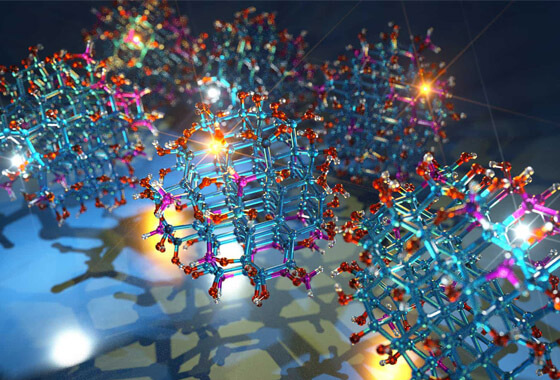
Material Synthesis
High-pressure reactors are indispensable for synthesizing advanced materials under controlled conditions. They enable researchers to explore novel synthesis routes, study material properties, and develop materials with tailored characteristics for applications in electronics, energy storage, and biomedical fields.
Catalysis Research
High pressure reactors are invaluable for studying catalytic reactions. Researchers use them to investigate reaction mechanisms, optimize catalyst performance, and develop efficient catalysts for various applications, including petroleum refining, environmental remediation, and chemical manufacturing.
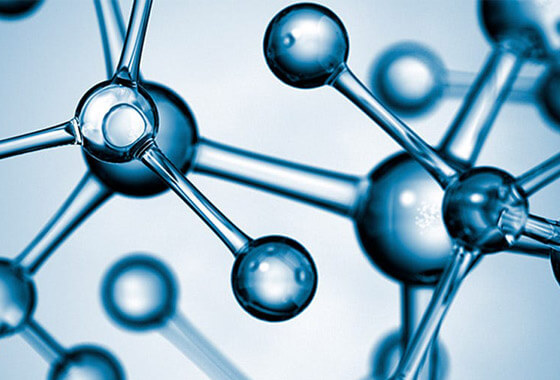
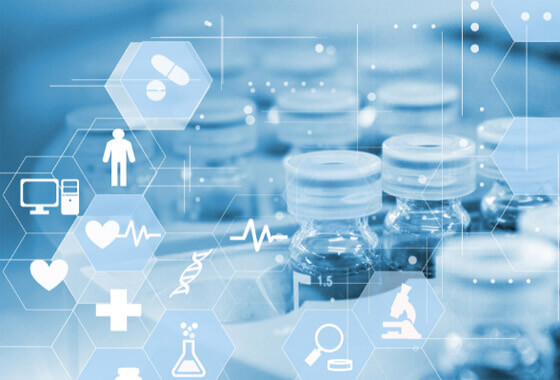
Pharmaceutical Development
High pressure reactors are employed in pharmaceutical research and development to optimize drug formulations. By providing precise pressure conditions, these reactors enhance reaction selectivity, yield, and purity, leading to the development of safer and more effective medications.
How does a high pressure batch reactor differ from other reactor types?
A high pressure batch reactor is a type of reactor where chemical reactions are conducted in discrete batches rather than continuously. Unlike continuous reactors, batch reactors offer greater flexibility in terms of reaction control and parameter adjustments between batches. This versatility makes them suitable for a wide range of applications, including process development, catalyst screening, and small-scale production.
How does a high pressure batch reactor differ from other reactor types?
A high pressure batch reactor is a type of reactor where chemical reactions are conducted in discrete batches rather than continuously. Unlike continuous reactors, batch reactors offer greater flexibility in terms of reaction control and parameter adjustments between batches. This versatility makes them suitable for a wide range of applications, including process development, catalyst screening, and small-scale production.
What are the key features of a high pressure chemical reactor?
A high pressure chemical reactor is equipped with features such as a sturdy pressure vessel, precise temperature control systems, safety relief mechanisms, and instrumentation for monitoring and controlling reaction parameters. These reactors are designed to operate safely under high pressures and temperatures while ensuring efficient mixing and heat transfer for homogeneous reaction conditions. They are widely used in chemical synthesis, material science, and process development.
How does a high pressure high temperature reactor enable advanced material synthesis?
A high pressure high temperature reactor provides the ideal conditions for synthesizing advanced materials such as nanoparticles, nanocomposites, and specialty polymers. By combining elevated pressures and temperatures, these reactors facilitate rapid nucleation, growth, and crystallization processes, resulting in the formation of unique nanostructures and tailored material properties. They are invaluable tools for research and development in nanotechnology, catalysis, and materials science.
What are the advantages of using a high pressure laboratory reactor?
A high pressure laboratory reactor offers researchers a versatile platform for conducting experiments under controlled pressure and temperature conditions. These reactors allow for precise control over reaction parameters, scalability from small to larger volumes, and the ability to explore a wide range of chemical reactions. They are essential tools for studying reaction kinetics, mechanism elucidation, and process optimization in academic and industrial laboratories.
How can a high pressure reactor vessel enhance safety in chemical processes?
High pressure reactor vessels are designed with multiple safety features to mitigate risks associated with high-pressure reactions. These features may include pressure relief valves, rupture discs, interlocking systems, and redundant pressure monitoring devices. These safety measures help prevent equipment failure, overpressure incidents, and potential hazards to operators and the environment, ensuring safe operation in chemical processing facilities.
What factors should be considered when selecting a high pressure batch reactor?
When choosing a high pressure batch reactor, factors such as maximum operating pressure and temperature, material compatibility, mixing efficiency, scalability, and safety features should be carefully evaluated. Additionally, considerations related to process automation, maintenance requirements, and regulatory compliance play a crucial role in selecting the most suitable reactor for specific applications.
How does the design of a high pressure chemical reactor impact reaction kinetics?
The design of a high pressure chemical reactor influences reaction kinetics by affecting factors such as mixing efficiency, heat transfer rates, and mass transfer characteristics. Optimal reactor designs ensure uniform distribution of reactants, efficient heat transfer, and effective mass transport, leading to enhanced reaction rates and product yields. Well-designed reactors minimize side reactions and improve the selectivity and efficiency of chemical processes.
Can a high pressure high temperature reactor be used for hydrothermal synthesis?
Yes, a high pressure high temperature reactor is commonly used for hydrothermal synthesis, a process that involves the reaction of aqueous solutions or suspensions at elevated pressures and temperatures. These reactors enable the rapid formation of crystalline materials, nanomaterials, and composites under hydrothermal conditions, offering advantages such as enhanced reaction rates, improved crystallinity, and control over particle size and morphology.
What role does a high pressure laboratory reactor play in catalyst development?
A high pressure laboratory reactor is an essential tool for catalyst development and screening. These reactors allow researchers to evaluate the performance of catalysts under high-pressure conditions, simulate industrial processes, and optimize reaction parameters for improved catalytic activity and selectivity. High pressure reactors enable efficient testing of catalysts for various applications, including hydrogenation, oxidation, and polymerization reactions.
How does pressure control impact the performance of a high pressure reactor vessel?
Pressure control is critical for optimizing reaction outcomes and ensuring safety in a high pressure reactor vessel. Precise pressure regulation allows researchers to maintain desired pressure conditions, explore reaction kinetics, and achieve reproducible results. Effective pressure control also helps prevent overpressure incidents, equipment failure, and potential hazards, ensuring reliable and safe operation of high pressure reactors.
Can a high pressure batch reactor be used for polymerization reactions?
Yes, a high pressure batch reactor is well-suited for polymerization reactions, including radical, cationic, anionic, and coordination polymerizations. These reactors provide the elevated pressures and temperatures necessary for initiating and sustaining polymerization processes, allowing for the synthesis of polymers with controlled molecular weights, architectures, and properties. High pressure batch reactors offer advantages such as improved reaction kinetics, enhanced control over polymerization conditions, and scalability from laboratory-scale to production-scale operations. They are widely used in the production of a variety of polymers for applications ranging from plastics and elastomers to specialty materials and advanced composites.
How does a high pressure laboratory reactor contribute to the development of sustainable chemical processes?
High pressure laboratory reactors play a key role in the development of sustainable chemical processes by enabling researchers to explore novel reaction pathways, optimize process parameters, and improve resource efficiency. These reactors facilitate the synthesis of valuable chemicals, pharmaceuticals, and fine chemicals using greener solvents, renewable feedstocks, and energy-efficient processes. By reducing waste generation, energy consumption, and environmental impact, high pressure laboratory reactors contribute to the advancement of sustainable chemistry practices.
What considerations should be made when scaling up reactions from a high pressure laboratory reactor to industrial production?
Scaling up reactions from a high pressure laboratory reactor to industrial production requires careful consideration of factors such as process safety, equipment design, materials compatibility, and regulatory compliance. It is essential to ensure that the chosen production-scale reactor can handle larger volumes, higher pressures, and temperatures while maintaining the desired reaction conditions and product quality. Additionally, process economics, energy efficiency, and environmental impact should be evaluated to ensure the viability of the scaled-up process.
How can a high pressure reactor vessel be optimized for corrosion resistance?
To optimize corrosion resistance in a high pressure reactor vessel, suitable materials of construction and protective coatings should be selected based on the nature of the process fluids, operating conditions, and anticipated corrosion mechanisms. Stainless steels, nickel alloys, and titanium are commonly used materials for high pressure reactor vessels due to their excellent corrosion resistance properties. Additionally, surface treatments such as passivation, chemical etching, and ceramic coatings can further enhance corrosion resistance and extend the service life of the reactor vessel.
What role does temperature control play in high pressure chemical reactions?
Temperature control is crucial for regulating reaction rates, selectivity, and product yields in high pressure chemical reactions. Precise temperature control allows researchers to optimize reaction conditions, minimize side reactions, and achieve desired reaction kinetics. High pressure reactors are equipped with advanced temperature control systems, such as heating jackets, internal heating coils, or external heating baths, to maintain uniform temperatures throughout the reaction mixture and ensure reproducible results.
Can a high pressure laboratory reactor be used for supercritical fluid extraction?
Yes, a high pressure laboratory reactor can be adapted for supercritical fluid extraction (SFE) applications. Supercritical fluids such as carbon dioxide exhibit unique solvent properties at high pressures and temperatures, making them ideal for extracting target compounds from solid or liquid samples. High pressure reactors equipped with suitable pressure vessels, heating/cooling systems, and pressure regulators can be used to generate and control supercritical conditions for efficient extraction of desired analytes.
How does the design of a high pressure batch reactor impact mixing efficiency?
The design of a high pressure batch reactor significantly influences mixing efficiency, which is critical for achieving uniform reaction conditions and maximizing mass transfer rates. Features such as agitator configurations, baffle arrangements, and vessel geometry play a crucial role in promoting turbulence, enhancing mixing, and improving heat transfer throughout the reaction mixture. Well-designed reactors ensure thorough mixing of reactants, uniform temperature distribution, and efficient utilization of resources.
What safety measures should be implemented when operating a high pressure high temperature reactor?
When operating a high pressure high temperature reactor, strict adherence to safety protocols is essential to prevent accidents and ensure operator protection. Safety measures may include conducting risk assessments, implementing engineering controls, providing adequate ventilation, and using appropriate personal protective equipment (PPE). Additionally, emergency shutdown procedures, pressure relief systems, and regular equipment inspections should be in place to mitigate potential hazards and ensure safe operation.
How can a high pressure reactor vessel be customized for specific process requirements?
High pressure reactor vessels can be customized to accommodate specific process requirements and applications. Customization options may include variations in vessel size, shape, materials of construction, agitation systems, heating/cooling methods, and instrumentation. By collaborating with experienced manufacturers and engineers, users can tailor high pressure reactor vessels to meet their unique needs, optimize process performance, and achieve desired outcomes in chemical synthesis, research, and industrial production.
HIGH PRESSURE REACTOR
Ce Certified High Pressure Reactor Manufacturer
- Famous Brand Accessories
- More Than 33 Years of Manufacturing Experience
- Affordable High Pressure Reactor Price
- Experienced Customer Service