Stainless steel batch reactors are integral components of modern chemical processing industries. Their reliability, flexibility, and ability to handle various reactions make them indispensable in a wide range of applications. This article will explore the features, advantages, and applications of stainless steel batch reactor, shedding light on their importance in modern manufacturing processes.
1. Understanding Stainless Steel Batch Reactors
Stainless steel batch reactors serve as essential vessels for conducting chemical reactions in batch mode. Constructed with high-quality stainless steel, a material renowned for its exceptional corrosion resistance and durability, these reactors are ideally suited for a wide range of chemical processes. Their applications span across pharmaceuticals, petrochemicals, food processing, and specialty chemicals industries, among others, resulting in their significance in modern manufacturing processes being beyond measure.
The key distinction of stainless steel batch reactor lies in their ability to facilitate chemical reactions in a batch-wise manner. Batch reactors, unlike continuous flow reactors, permit the addition of reactants and removal of products in discrete quantities, which makes them particularly advantageous for small-scale production or situations involving multiple reaction steps. The stainless steel construction ensures that the reactor can withstand the challenges posed by diverse chemical reactions, maintaining product purity and preventing contamination.
These reactors are designed to accommodate a variety of reaction types, ranging from simple mixing and blending processes to complex reactions requiring precise control over temperature and pressure. The versatility of stainless steel batch reactor makes them indispensable in laboratories, pilot plants, and large-scale industrial facilities, offering flexibility in adapting to different production requirements.
In summary, stainless steel batch reactors are vital tools in the arsenal of chemical processing industries, owing to their robust construction, corrosion resistance, and ability to handle various reactions in a batch-wise fashion. As we delve deeper into their features, advantages, and applications, a clearer picture emerges of the crucial role these reactors play in advancing numerous industrial sectors.
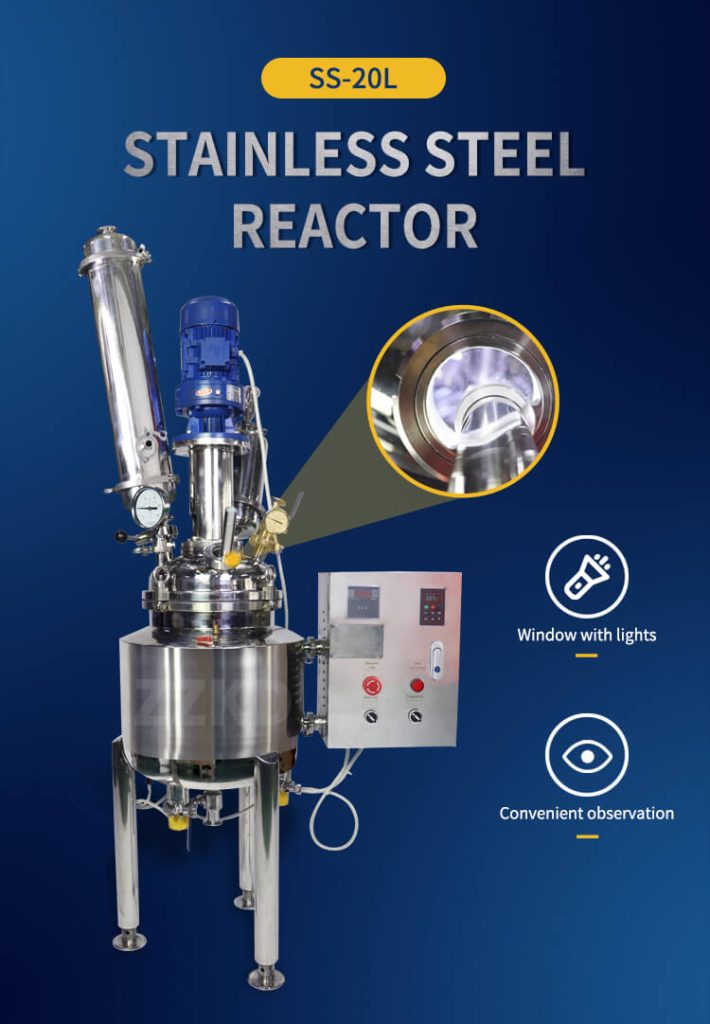
2. Key Features and Advantages
Stainless steel batch reactors offer several key features that contribute to their popularity:
a) Corrosion Resistance: Stainless steel is inherently resistant to corrosion, ensuring a longer service life and maintaining the purity of the process.
b) Temperature and Pressure Tolerance: These reactors can withstand high temperatures and pressures, enabling them to handle diverse reactions.
c) Versatility: Stainless steel batch reactor can accommodate various reaction types, including mixing, crystallization, and homogenization.
d) Easy Cleaning and Maintenance: The smooth surface of stainless steel allows for easy cleaning and maintenance, crucial for maintaining product quality.
e) Safety: With proper design and operation, stainless steel batch reactor ensure safe containment of reactive substances.
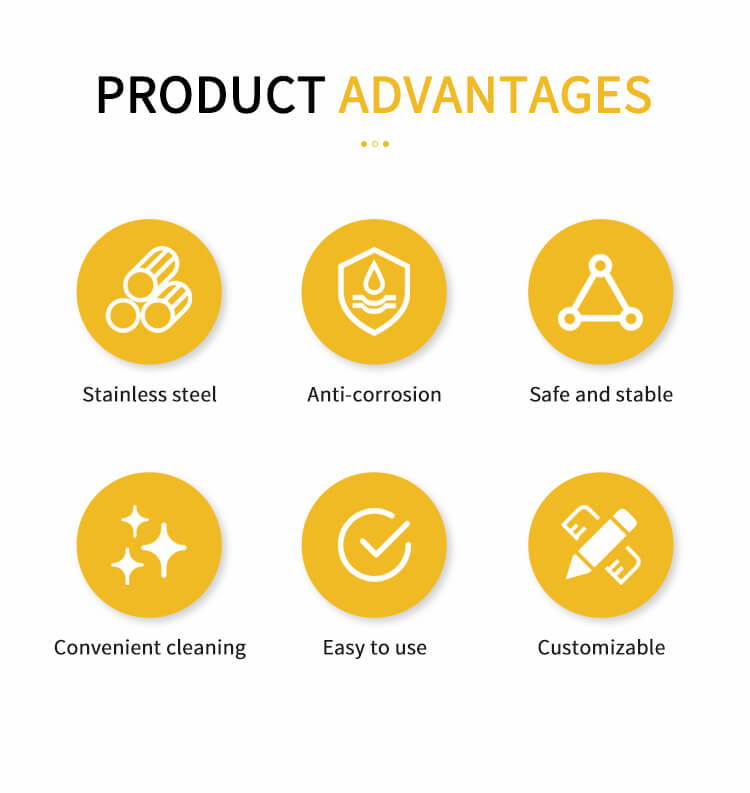
3. Design and Components of Stainless Steel Batch Reactors
Stainless steel batch reactors come in various sizes and designs, depending on the application and production scale. The essential components of a typical batch reactor include:
a) Vessel: The main body of the reactor, usually made of stainless steel, where the chemical reaction takes place.
b) Agitator: A mechanism to stir the contents inside the vessel, promoting even mixing and heat distribution.
c) Heating/Cooling System: To control the temperature during the reaction, these reactors are equipped with heating and cooling systems.
d) Control Panel: An interface that allows operators to monitor and regulate the process parameters.
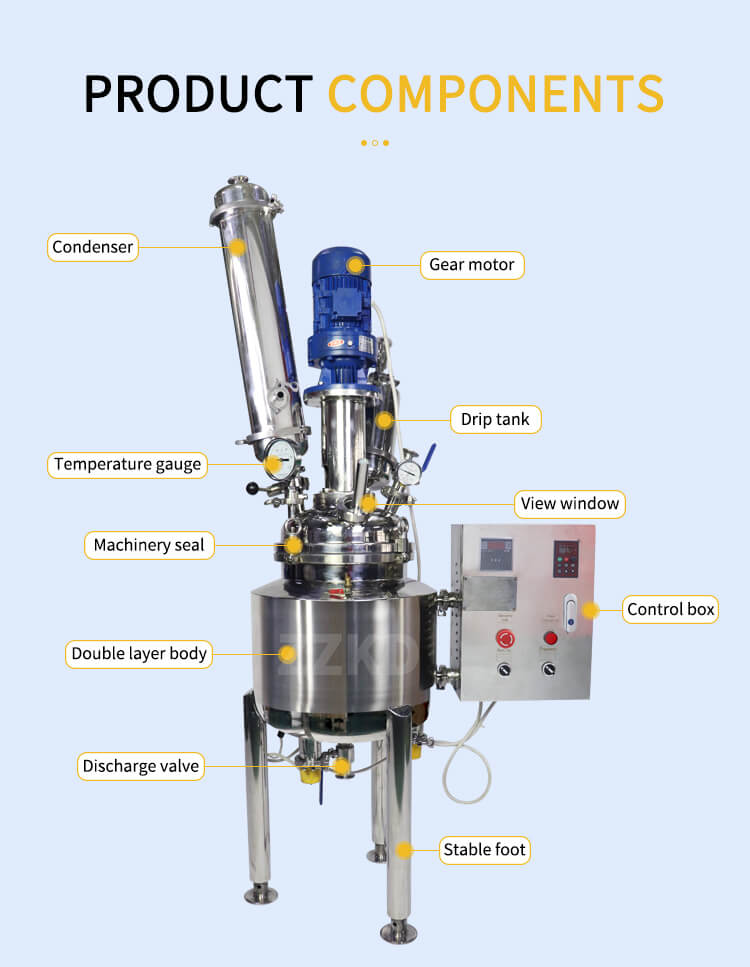
4. Applications of Stainless Steel Batch Reactors
The versatility of stainless steel batch reactors finds application in various industries. One notable case is their role in pharmaceutical manufacturing:
Case: Pharmaceutical Intermediate Synthesis
A pharmaceutical company was tasked with synthesizing an intermediate compound crucial for a life-saving drug. The chemical reaction involved several highly reactive substances that required careful handling and precise control of process parameters.
The company opted for a stainless steel batch reactor due to its suitability for the challenging synthesis. The reactor’s corrosion-resistant property ensured that the final product would meet the required purity standards. The agitator facilitated efficient mixing, preventing the formation of hotspots. Additionally, the heating and cooling systems allowed precise temperature control throughout the reaction.
The reactor’s robust design and safety features assured the company that the process would be carried out securely. The successful synthesis of the intermediate compound played a pivotal role in the production of the life-saving drug, saving countless lives worldwide.
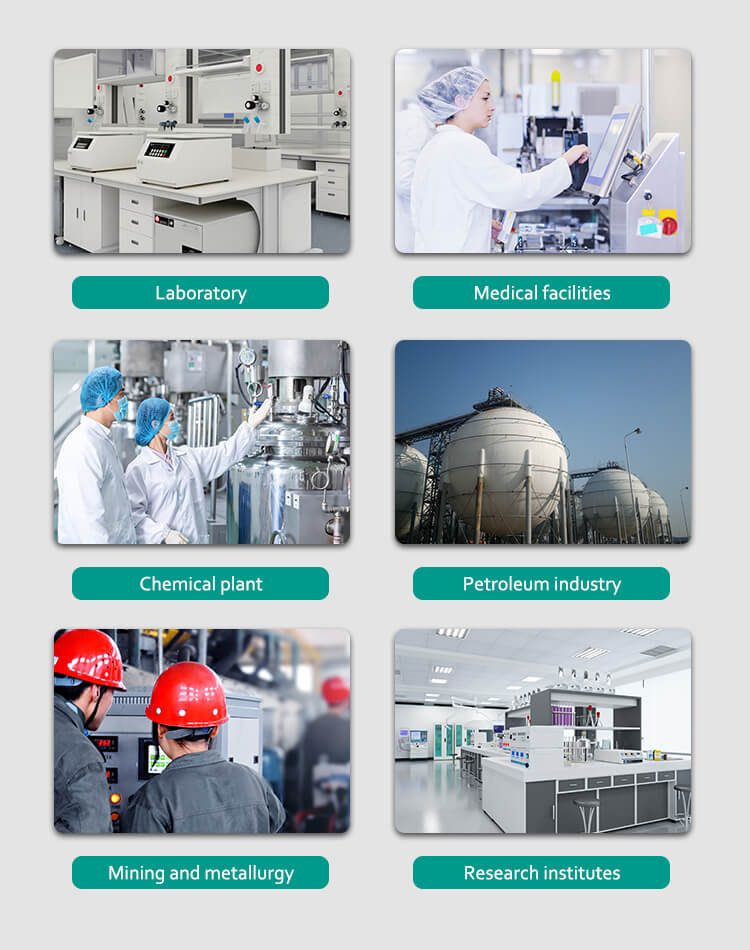
5. Process Optimization and Control
Efficient process optimization and control are essential to maximize the performance of stainless steel batch reactors. The following factors play a crucial role:
a) Reaction Kinetics: Understanding the reaction kinetics helps in determining the ideal temperature, pressure, and reaction time.
b) Agitation Speed: Proper agitation speed ensures uniform mixing and prevents the formation of dead zones.
c) Heat Transfer: Optimizing the heating and cooling systems enhances the energy efficiency of the process.
d) Monitoring and Automation: Incorporating advanced monitoring and automation technologies improves process efficiency and minimizes human errors.
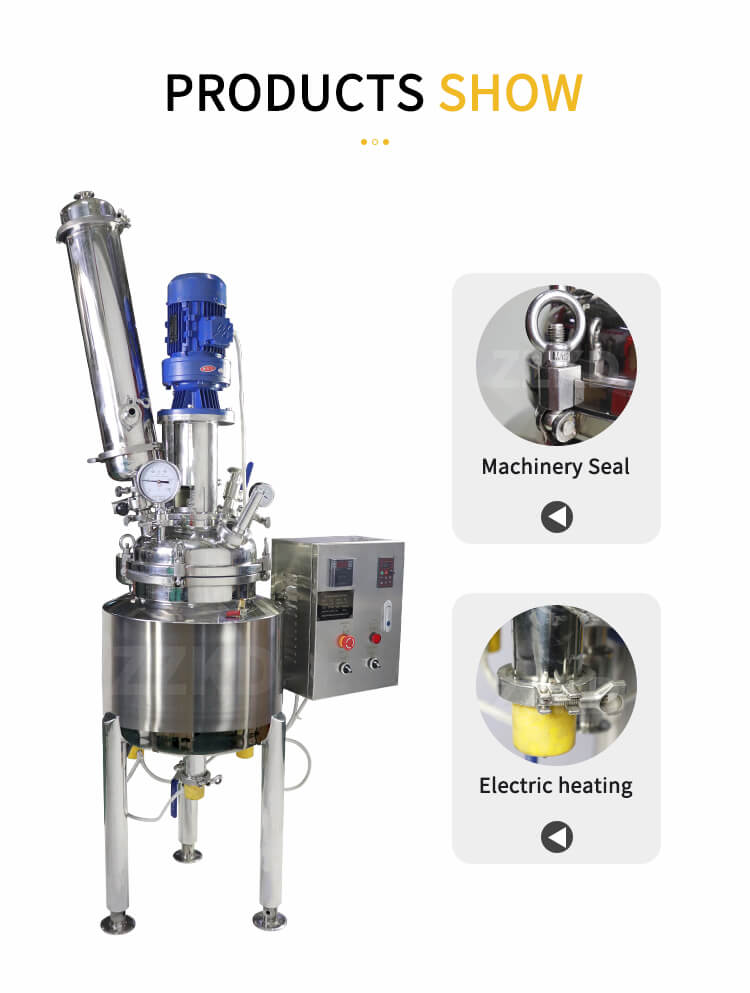
6. Maintenance and Safety Considerations
To ensure the longevity and safe operation of stainless steel batch reactors, regular maintenance is essential. Proper cleaning, inspection, and maintenance of components such as agitators, seals, and heating/cooling systems are vital for smooth operation.
Safety protocols should be strictly adhered to during operation, and operators must be well-trained in handling emergencies. Additionally, periodic inspections and adherence to industry standards are critical to avoid potential hazards.
Conclusion
Stainless steel batch reactors have revolutionized chemical processing by providing a versatile and reliable platform for various reactions. Their corrosion resistance, temperature tolerance, and ease of maintenance make them indispensable in pharmaceuticals, petrochemicals, and other industries.
As technology advances, stainless steel batch reactors will continue to evolve, further contributing to the advancement of chemical processing and the development of life-saving drugs, specialty chemicals, and other essential products. Understanding their design, applications, and optimization principles will empower industries to make the most of this valuable tool for chemical synthesis.