High pressure reactors play a pivotal role in various industries, enabling the synthesis of critical chemical compounds and materials. As the demand for high-quality and efficient reactors grows, manufacturers continually innovate to meet the requirements of diverse applications. This article sheds light on the world of high pressure reactor manufacturers, exploring their importance, technological advancements, and the key players shaping the industry.
Understanding High Pressure Reactors and Their Applications
High pressure reactors are specialized vessels designed to handle chemical reactions at elevated pressures, typically above 10 bar. These reactors find extensive usage in industries such as pharmaceuticals, petrochemicals, and material science, where high-pressure conditions are essential for specific reactions to occur efficiently.
In pharmaceutical research and manufacturing, high pressure reactors are employed for drug synthesis and formulation. They facilitate the production of pharmaceutical intermediates and active pharmaceutical ingredients (APIs) with high purity and yield. High pressure reactors are also instrumental in petrochemical processes, enabling the production of specialty chemicals and refining of raw materials into valuable end products.
The material science sector benefits from high pressure reactors as they enable the synthesis of advanced materials with enhanced properties. These materials find applications in aerospace, electronics, and energy industries, among others. From carbon nanotubes to advanced ceramics, high pressure reactors have opened up new frontiers in materials engineering.
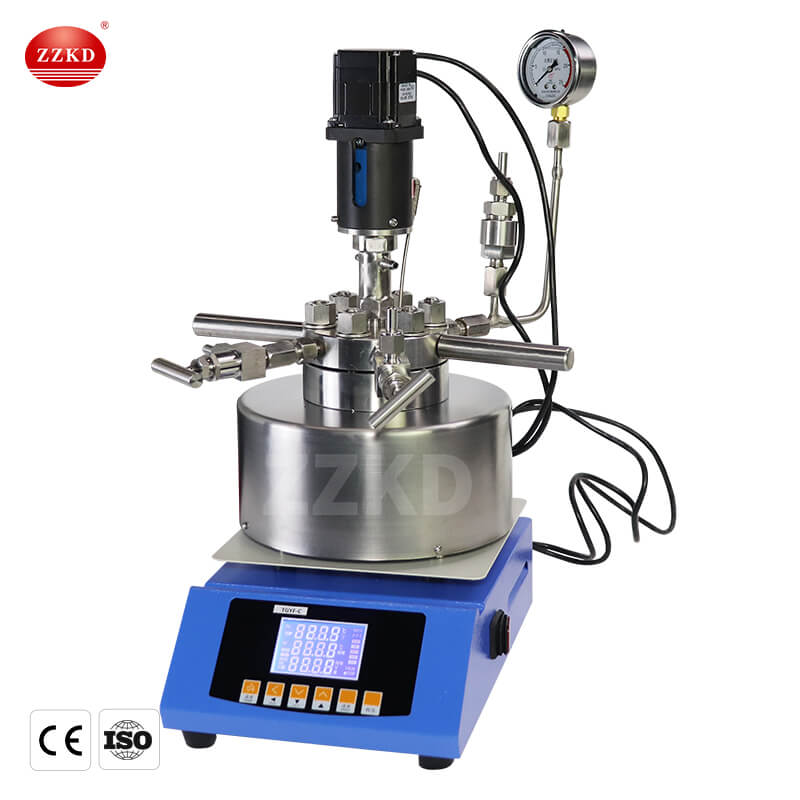
Key Features and Design Considerations
Innovation in high pressure reactor manufacturing centers around incorporating advanced features to enhance safety, performance, and ease of operation. Reactor vessels are usually made from high-strength materials like stainless steel or high-nickel alloys to withstand the immense pressure. The design also includes safety measures like pressure relief systems, rupture discs, and fail-safe mechanisms to prevent accidents during operation.
Moreover, manufacturers pay special attention to the sealing mechanisms in high pressure reactors. Efficient and reliable sealing ensures that no hazardous chemicals leak during the reaction, maintaining the safety of the operators and the environment. Some reactors feature magnetic stirrers to facilitate mixing without the need for mechanical seals, reducing the risk of seal failure.
Additionally, many high pressure reactors are equipped with temperature and pressure monitoring systems. These systems enable precise control over the reaction conditions, ensuring the reactions proceed as intended. Automated control systems have become more prevalent, offering user-friendly interfaces and remote monitoring capabilities.
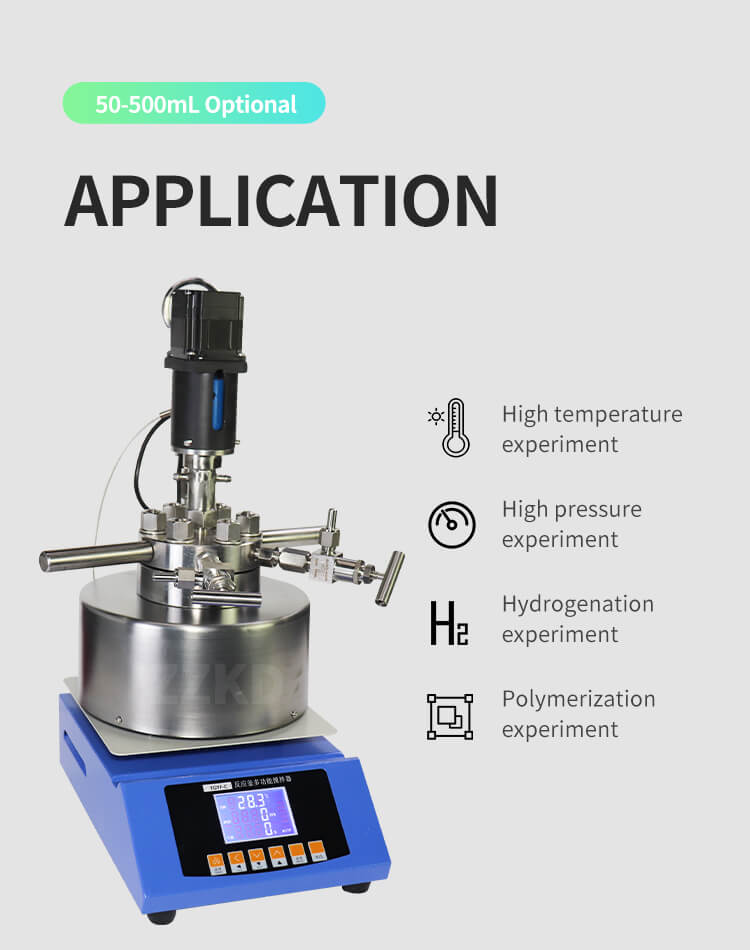
Leading High Pressure Reactor Manufacturers
One of the most prominent players in the high pressure reactor manufacturing industry is ZZKD INSTRUMENTS. With a legacy of excellence and a commitment to research and development, ZZKD INSTRUMENTS has established itself as a leading name in the market. Throughout its history, ZZKD’s high pressure reactors have been widely sought after, gaining recognition for their exceptional quality and performance.
ZZKD INSTRUMENTS takes a customer-centric approach, focusing on customizing reactors to cater to the unique requirements of its clients. Their team of experts works closely with customers, understanding their specific needs, and designing reactors that precisely align with those demands. This personalized approach has earned ZZKD INSTRUMENTS a loyal customer base across diverse industries.
Moreover, an additional strength of ZZKD is its unwavering commitment to cost-effectiveness without compromising on quality. Through innovative manufacturing processes and an emphasis on efficiency, ZZKD can offer high pressure reactors at competitive prices, thus making them accessible to small to medium-scale industries.
With its continuous pursuit of excellence and commitment to technological advancements, ZZKD INSTRUMENTS remains at the forefront of the high pressure reactor manufacturing industry. As the demand for cutting-edge solutions grows, ZZKD’s innovative and reliable reactors are poised to shape the future of chemical engineering applications worldwide.
Technological Advancements and Innovations
The continuous pursuit of improvement has led high pressure reactor manufacturers to develop cutting-edge technologies. One such innovation is the integration of automated control systems, enabling precise monitoring and regulation of pressure, temperature, and other critical parameters. This advancement has significantly improved the reproducibility and reliability of reactions, making them more attractive for large-scale industrial applications.
Furthermore, the incorporation of catalytic reactors has shown promising results in enhancing reaction rates and selectivity. Catalytic high pressure reactors allow reactions to occur at lower temperatures and pressures, saving energy and reducing the wear and tear on reactor materials. These reactors are particularly advantageous in processes where specific catalysts play a crucial role in the reaction.
Moreover, the use of computational fluid dynamics (CFD) simulations in reactor design has revolutionized the industry. CFD allows manufacturers to visualize and analyze fluid flow patterns within the reactor, leading to optimized reactor designs that ensure better mixing and heat transfer during the reaction.
Quality Control and Compliance with Standards
To ensure the utmost safety and reliability, high pressure reactor manufacturers adhere to stringent quality control processes. Reputable manufacturers follow international standards, such as ISO 9001 and ASME BPVC, throughout the manufacturing process. These standards cover material selection, fabrication, testing, and certification, providing customers with confidence in the performance and durability of their high-pressure reactors.
Non-destructive testing techniques like ultrasonic and radiographic examination detect and address reactor structure defects before reaching users. In addition to safety, compliance with international standards also streamlines global trade, allowing manufacturers to export their high pressure reactors to various countries.
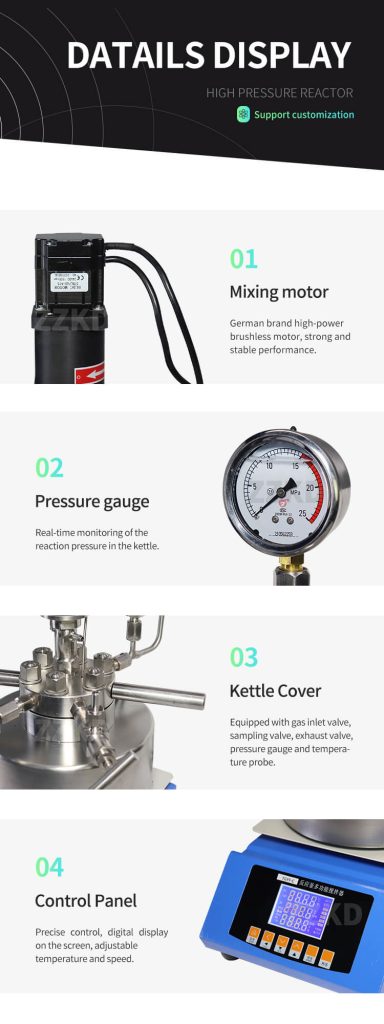
Future Outlook and Emerging Trends
As the demand for high pressure reactors grows, manufacturers are actively exploring sustainable and eco-friendly practices in their production processes. The reduction of carbon footprint and the use of recyclable materials are gaining importance in the industry, aligning with the global effort to combat climate change.
Moreover, advancements in nanotechnology and materials science hold the potential for the development of more efficient and durable reactor materials. Nanomaterials exhibit unique properties that could revolutionize high pressure reactor design, leading to higher performance and longer-lasting vessels.
The integration of artificial intelligence and machine learning algorithms is also on the horizon, aiming to optimize reactor performance and reduce energy consumption. AI-driven control systems can adapt to changing reaction conditions and automatically adjust parameters to achieve the desired outcomes, maximizing efficiency and reducing waste.
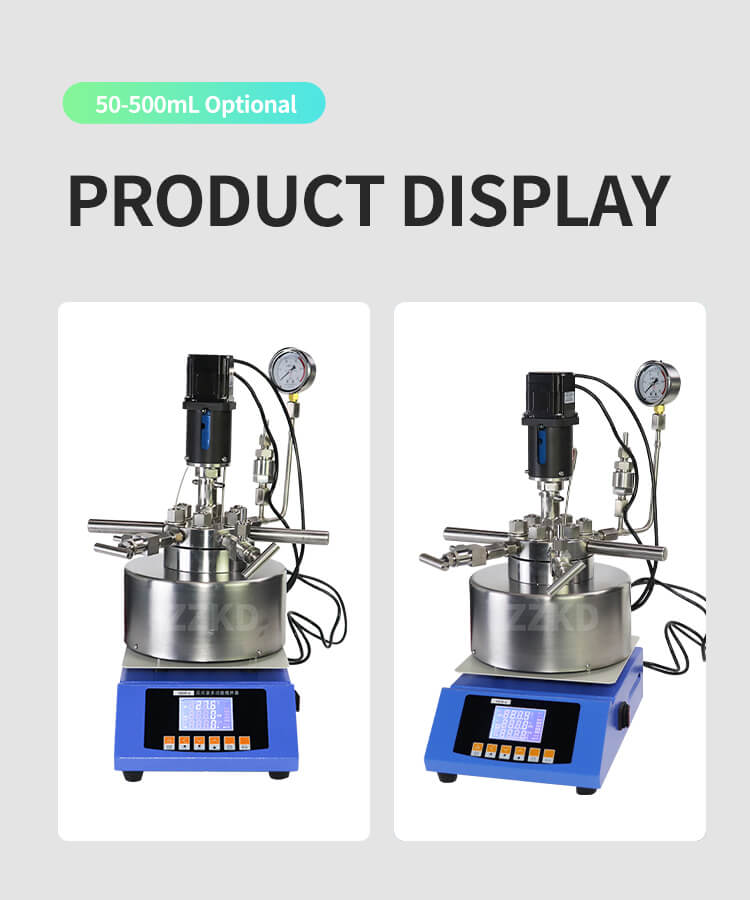
Conclusion
High pressure reactor manufacturers play a crucial role in advancing chemical engineering across various industries. Their dedication to innovation, safety, and compliance with international standards ensures the reliable production of essential chemicals and materials. As technology continues to evolve, these manufacturers will undoubtedly shape the future of high pressure reactors, empowering industries to achieve greater efficiency and sustainability in their operations. Through continuous research and development, high pressure reactor manufacturers will further revolutionize chemical processes, enabling the creation of new and innovative products that will shape the world in the years to come.