In the realm of chemical research and industrial processes, remarkable advancements have taken place in recent years. These innovations have revolutionized the way experiments are conducted and products are manufactured. One such breakthrough is the electric glass reactor kettle. This cutting-edge device combines the benefits of glass reactors with the efficiency of electric heating systems. This article explores the intricacies of the electric glass reactors kettle, including its functionality, advantages, and applications across various industries. Furthermore, a compelling real-life case study highlights the practical implementation and impact of this revolutionary technology.
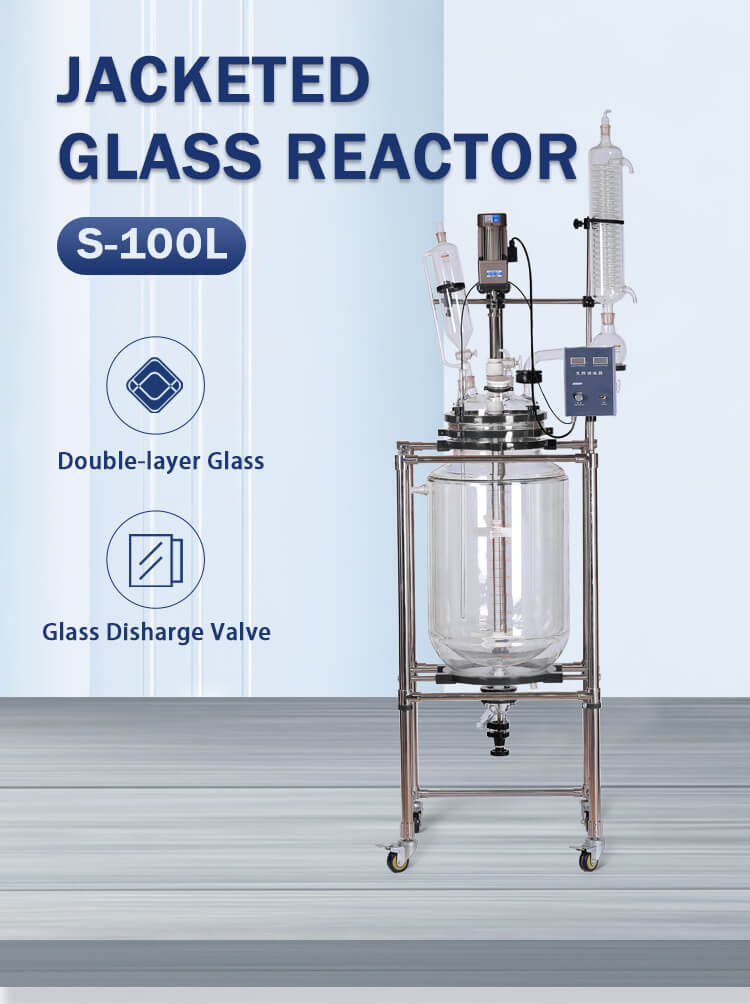
I. Understanding the Electric Glass Reactor Kettle
A. Overview and Working Principle
The electric glass reactor kettle is an innovative apparatus designed to facilitate chemical reactions and experimental processes. It consists of a glass vessel equipped with an electric heating system, offering precise temperature control during reactions. By heating the reaction mixture directly, this device enhances the efficiency of heat transfer and ensures uniform temperature distribution.
B. Components and Design Features
The electric glass reactors kettle comprises several essential components. These include a glass vessel, electric heating elements, temperature sensors, stirring mechanisms, and control panels. The glass vessel is made of high-quality borosilicate glass, known for its resistance to thermal shocks and chemical corrosion. The electric heating elements are strategically placed within the vessel to ensure optimal heat distribution. Temperature sensors provide accurate readings, allowing scientists to monitor and adjust the reaction conditions as necessary. Stirring mechanisms aid in homogenizing the reaction mixture, promoting efficient reactions.

C. Safety Measures and Contamination Prevention
Ensuring the safety of operators and preventing contamination are paramount in any chemical process. Electric glass reactor kettles are equipped with safety features such as overheating protection, automated shut-off systems, and pressure release valves. These measures safeguard against potential accidents and ensure smooth and secure operation. Moreover, the use of glass vessels minimizes the risk of contamination, as glass is non-reactive and easy to clean.
II. Advantages of the Electric Glass Reactor Kettle
A. Enhanced Temperature Control and Heating Efficiency
The electric glass reactor kettle offers superior temperature control compared to conventional heating methods. The electric heating elements enable precise and rapid adjustments to the desired temperature, minimizing temperature fluctuations. This level of control ensures the accurate replication of reaction conditions, leading to consistent and reliable experimental results. Furthermore, the direct heating method employed by the electric glass reactors kettle enhances heat transfer efficiency, reducing heating times and improving overall process efficiency.
B. Versatility and Flexibility in Experiment Design
The electric glass reactor kettle provides researchers with significant versatility and flexibility in designing experiments. The transparent glass vessel allows real-time observation of the reaction, enabling researchers to monitor and analyze the progress of the process. This feature is particularly valuable when studying color changes, phase transitions, or gas evolution. Additionally, the ability to control temperature gradients within the vessel facilitates various reaction setups, including reflux, distillation, and multi-step synthesis.
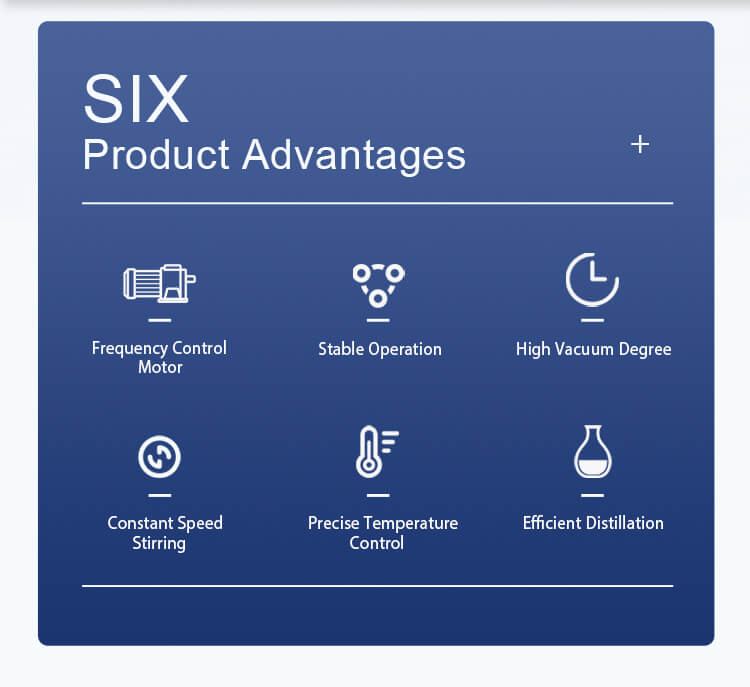
C. Transparency and Observation Capabilities
The transparency of the glass vessel in the electric glass reactor kettle is a significant advantage. It enables researchers to visually inspect the reaction, making it easier to identify any irregularities or unexpected phenomena. This visual feedback can be crucial in troubleshooting experiments or optimizing reaction parameters. The transparency also allows for the integration of additional monitoring tools, such as pH sensors or spectrometers, to gather further data during the reaction.
D. Easy Maintenance and Cleaning Procedures
Maintaining a clean and contamination-free environment is essential for reliable experimental results. The electric glass reactor kettle simplifies the cleaning process due to its smooth glass surfaces and easy disassembly. Glass vessels are inert, non-absorbent, and resistant to chemical attacks, ensuring thorough cleaning and eliminating the risk of residual contamination. The ease of disassembly allows for convenient access to all parts, simplifying maintenance and replacement of components.
III. Application Case: Optimizing Pharmaceutical Synthesis
A. Problem Statement and Objective
In the pharmaceutical industry, the synthesis of new drug compounds is a critical process that requires precision and efficiency. A pharmaceutical company aimed to optimize the synthesis of a complex molecule, targeting increased yield, reduced reaction time, and improved purity. The electric glass reactor kettle was identified as a potential solution to address these challenges.
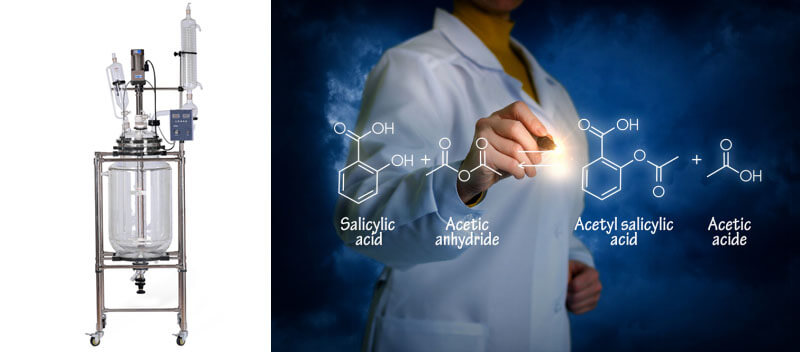
B. Implementation of the Electric Glass Reactor Kettle
The electric glass reactor kettle was integrated into the existing synthesis setup, replacing the traditional heating method with its advanced electric heating system. The glass vessel allowed real-time observation of the reaction, ensuring optimal temperature control and monitoring of reaction progress. The researchers optimized the heating parameters, leveraging the precise temperature control offered by the electric glass reactor kettle.
C. Results and Benefits Achieved
The implementation of the electric glass reactor kettle resulted in significant improvements in the pharmaceutical synthesis process. The precise temperature control enabled the researchers to achieve a higher yield of the desired compound, reducing wastage and costs. Additionally, the improved heat transfer efficiency led to shorter reaction times, accelerating the overall synthesis process. The transparency of the glass vessel allowed for real-time monitoring, ensuring timely adjustments and preventing unwanted side reactions. These benefits combined to increase the purity of the final product, meeting the stringent quality requirements of the pharmaceutical industry.
D. Future Scope and Potential Improvements
The successful implementation of the electric glass reactor kettle in pharmaceutical synthesis opens up new possibilities for further optimization and process improvements. Future research could focus on integrating additional monitoring and control systems, such as automated dosing or feedback loops, to enhance reaction precision and reproducibility. Exploring the compatibility of the electric glass reactor kettle with different reaction conditions, such as high pressures or corrosive environments, could also expand its applicability in the pharmaceutical industry.
IV. Electric Glass Reactor Kettle in the Chemical Industry
A. Synthesis of Specialty Chemicals
The electric glass reactor kettle finds extensive application in the synthesis of specialty chemicals. Its versatility and precise temperature control make it ideal for reactions requiring stringent conditions, such as high temperatures, controlled atmospheres, or sensitive reagents. The transparency of the glass vessel facilitates monitoring of color changes or precipitation events, aiding in reaction control and optimization.
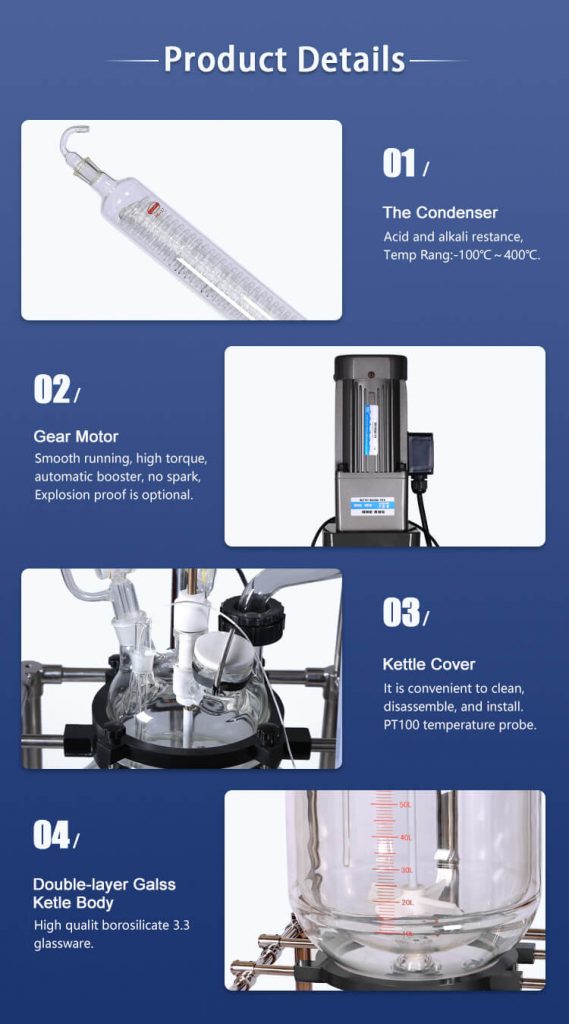
B. Production of Fine Chemicals and Pharmaceuticals
In the production of fine chemicals and pharmaceuticals, the electric glass reactor kettle offers significant advantages. Its transparent design allows for the visual inspection of reactions, ensuring the absence of impurities or unexpected by-products. The precise temperature control and efficient heat transfer promote yield improvement, reaction optimization, and reduction in production costs.
C. Petrochemical Research and Development
Petrochemical research often involves complex and sensitive reactions that require careful control and monitoring. The electric glass reactor kettle’s ability to maintain precise temperature conditions and its transparency facilitate the study of reaction kinetics, phase changes, and catalyst performance. These capabilities contribute to the development of efficient and environmentally friendly petrochemical processes.
D. Material Synthesis and Characterization
The electric glass reactor kettle is invaluable in material synthesis and characterization. Its transparent vessel allows researchers to observe the formation of nanoparticles, crystal growth, or polymerization reactions in real-time. The precise temperature control and efficient heat transfer enable the synthesis of materials with specific properties, such as particle size, morphology, or crystallinity.
V. Advancements and Future Developments
A. Integration with Automation and Process Control Systems
To further streamline experimental processes, integrating the electric glass reactor kettle with automation and process control systems is a promising avenue. Automation can facilitate precise dosing, data logging, and optimization algorithms, while process control systems enable real-time adjustments based on sensor feedback. These advancements would enhance the reproducibility, efficiency, and scalability of experiments.
B. Incorporation of Artificial Intelligence and Machine Learning
Artificial intelligence (AI) and machine learning (ML) techniques have the potential to revolutionize chemical research and industrial processes. By leveraging data collected from the electric glass reactor kettle, AI algorithms can identify reaction patterns, optimize reaction conditions, and predict outcomes. ML models can analyze vast amounts of experimental data, aiding in process optimization and accelerating research and development efforts.
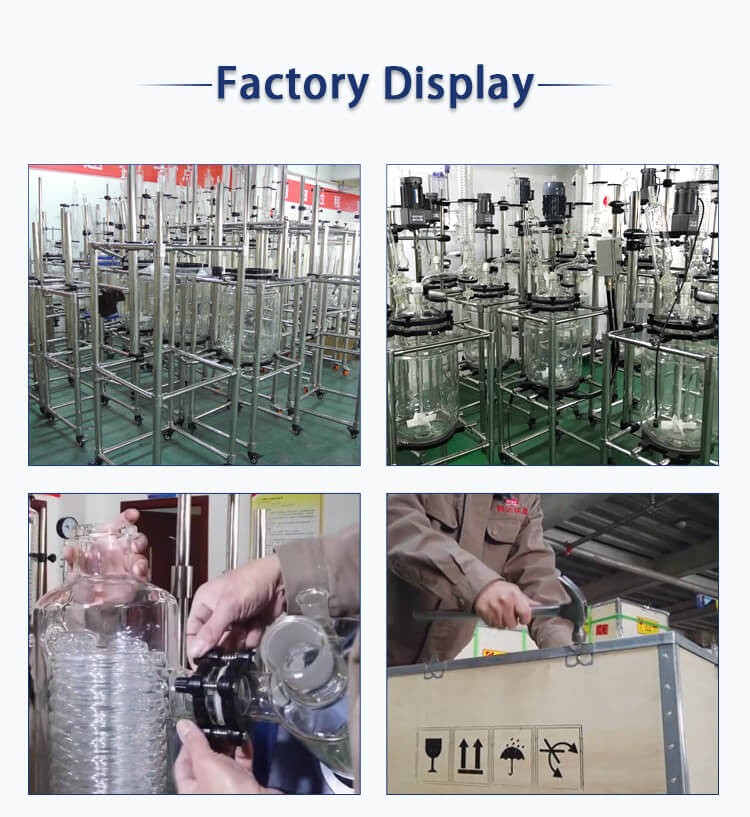
C. Miniaturization and Portable Solutions
Advancements in miniaturization can lead to the development of compact and portable electric glass reactor kettles. These portable solutions would enable on-site research, process optimization, and point-of-care production. They would also find applications in resource-limited settings, expanding access to chemical research and manufacturing capabilities.
D. Exploration of New Materials for Reactor Design
Continued research into new materials for reactor design holds the potential for further enhancing the performance of electric glass reactor kettles. Novel materials could improve heat transfer efficiency, increase resistance to aggressive chemicals, or enable the use of higher operating temperatures and pressures. Exploring advanced materials can unlock new possibilities for reaction optimization and expand the range of applications for this technology.
VI. Conclusion
The electric glass reactor kettle has emerged as a game-changer in the field of chemical research and industrial processes. By combining the transparency and observation capabilities of glass reactors with the precise temperature control and efficiency of electric heating systems, this technology offers numerous advantages. Its impact spans across various industries, from pharmaceutical synthesis to petrochemical research and material synthesis.
The application case highlighted the successful implementation of the electric glass reactor kettle in optimizing pharmaceutical synthesis, resulting in increased yield, reduced reaction time, and improved product quality. This real-life example demonstrates the practical benefits and the potential for advancements in other industries.
Looking ahead, integration with automation and process control systems, incorporation of AI and ML techniques, miniaturization of devices, and exploration of new materials will further enhance the capabilities of electric glass reactor kettles. As this technology continues to evolve, it holds the promise of driving innovation, optimizing processes, and shaping the future of chemical research and industrial manufacturing.