The high pressure batch reactor is a versatile and powerful tool in the field of chemical engineering. It enables researchers and industrial professionals to conduct reactions under controlled conditions, ensuring enhanced safety, improved efficiency, and a wider range of possible reactions. This article aims to provide an in depth understanding of high pressure batch reactors, their applications, benefits, and key considerations in their usage.
I. Understanding High Pressure Batch Reactors
A. Definition and Working Principle
B. Components and Design Considerations
C. Safety Measures and Regulations
II. Applications of High Pressure Batch Reactors
A. Catalysis and Reaction Kinetics Studies
III. Case: High Pressure Batch Reactor in Hydrogenation Process
A. Background of the Hydrogenation Process
B. Benefits of High Pressure Batch Reactors in Hydrogenation
C. Process Optimization and Yield Improvement
D. Industrial Implementation and Success Stories
IV. Advantages of High Pressure Batch Reactors
A. Enhanced Mass and Heat Transfer
C. Improved Safety and Control
V. Considerations in High Pressure Batch Reactor Usage
A. Material Selection and Compatibility
B. Reactor Scale up and Automation
C. Reaction Optimization and Monitoring
D. Maintenance and Troubleshooting
VI. Future Developments and Emerging Trends
B. Integration of Artificial Intelligence and Machine Learning
C. Sustainable and Green Chemistry Applications
D. Miniaturization and Portable Reactors
A. Recap of High Pressure Batch Reactor Advantages
B. Importance of Continuous Innovation
C. The Role of High Pressure Batch Reactors in Advancing Chemical Engineering
I. Understanding High Pressure Batch Reactors
Definition and Working Principle:
A high pressure batch reactor refers to a vessel designed to withstand elevated pressures, typically ranging from a few hundred to several thousand psi (pounds per square inch). It allows for the controlled mixing of reactants and the initiation of chemical reactions under specific temperature and pressure conditions. This controlled environment enables researchers to study various reaction parameters and optimize reaction kinetics.
Components and Design Considerations:
High pressure batch reactors consist of several key components, including a sturdy pressure vessel, an agitator or stirring mechanism, a heat transfer system, pressure control devices, and safety features such as relief valves and rupture disks. Design considerations revolve around material selection, reactor geometry, sealing mechanisms, and efficient heat transfer to maintain temperature control.
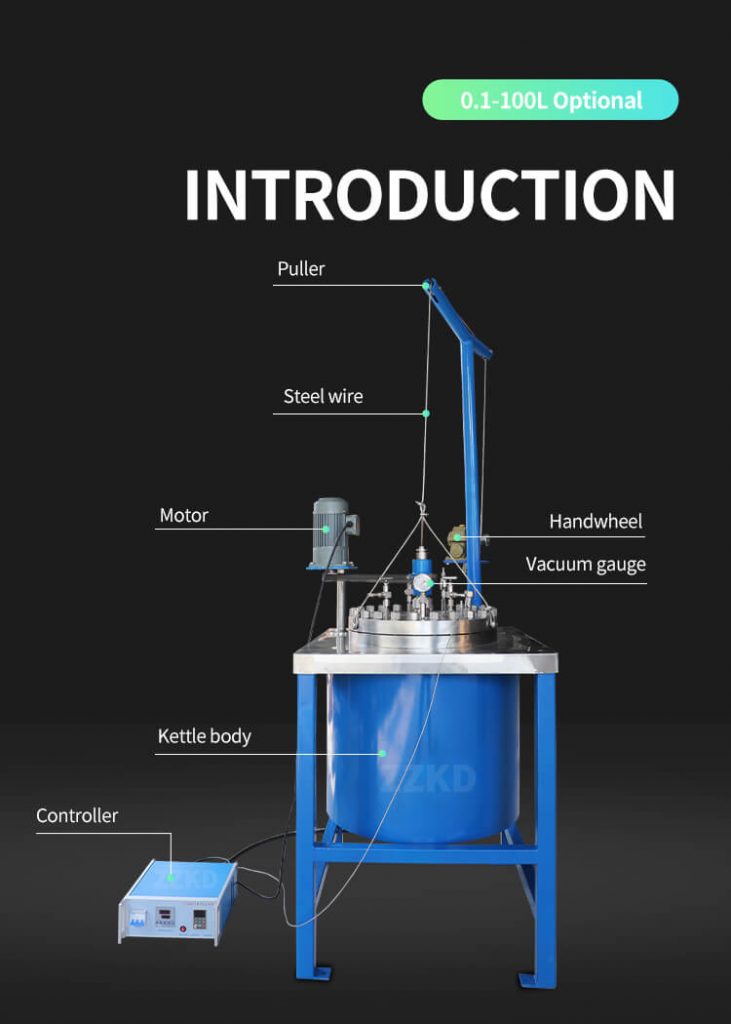
Safety Measures and Regulations:
Operating high pressure batch reactors requires adherence to strict safety protocols and regulations to mitigate potential hazards. These measures include thorough risk assessments, proper training for operators, frequent inspections, and the use of safety interlocks. Compliance with applicable industry standards and guidelines, such as those outlined by the American Society of Mechanical Engineers (ASME) and the Occupational Safety and Health Administration (OSHA), is crucial.
II. Applications of High Pressure Batch Reactors
Catalysis and Reaction Kinetics Studies:
High pressure batch reactors play a crucial role in studying catalytic processes and reaction kinetics. By subjecting reactants to elevated pressures, researchers can investigate the impact of pressure on reaction rates, selectivity, and overall efficiency. This knowledge aids in the development of new catalysts and optimization of existing catalytic processes.
Pharmaceutical Synthesis:
The pharmaceutical industry often relies on high pressure batch reactors for the synthesis of active pharmaceutical ingredients (APIs). The ability to control temperature, pressure, and reactant concentration enables precise control over reaction conditions, leading to improved yields and reduced impurities. High pressure batch reactors also facilitate the exploration of new reaction pathways and the development of innovative drug synthesis strategies.
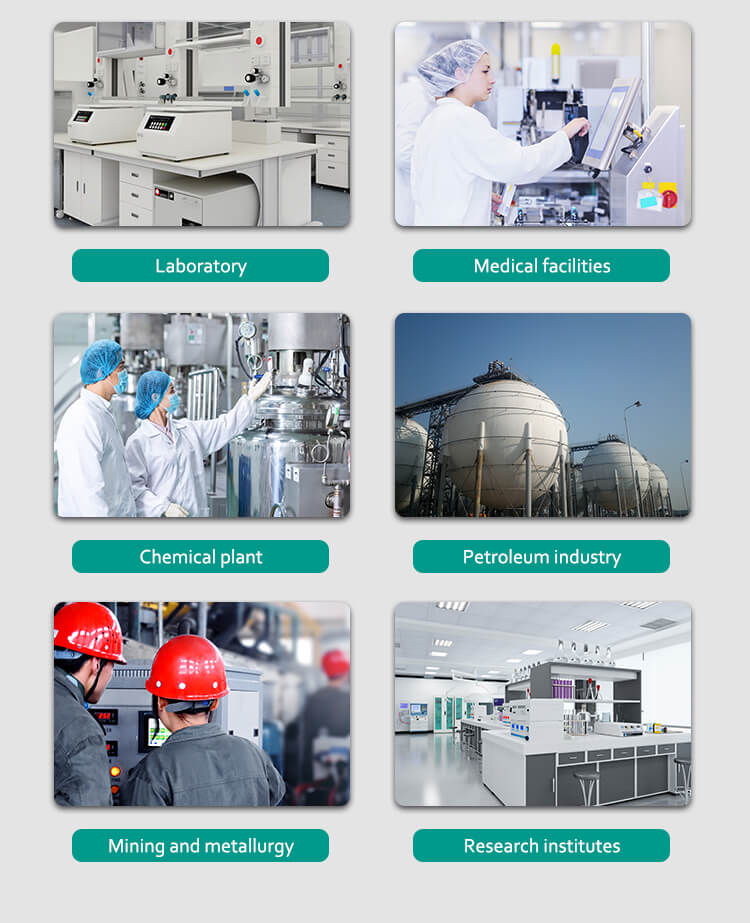
Polymerization Reactions:
Polymerization reactions, such as those used in the production of plastics, require precise control of reaction parameters to achieve desired polymer properties. High pressure batch reactors provide an ideal environment for conducting polymerization reactions, allowing for efficient mixing of monomers, control over reaction kinetics, and the synthesis of tailored polymers with specific molecular weights and structures.
Petrochemical Industry:
The petrochemical industry relies heavily on high pressure batch reactors for various processes, including hydrocracking, reforming, and hydrotreating. These reactors enable the conversion of crude oil fractions into valuable products, such as gasoline, diesel, and petrochemical intermediates. High pressure conditions facilitate the breaking of complex hydrocarbon chains, enhancing product yields and improving overall process efficiency.
III. Case: High Pressure Batch Reactor in Hydrogenation Process
Background of the Hydrogenation Process:
Hydrogenation is a common chemical process employed in various industries, including food production, pharmaceuticals, and fine chemicals. It involves the addition of hydrogen gas to unsaturated compounds, resulting in the saturation of double or triple bonds. High pressure batch reactors provide an ideal platform for conducting hydrogenation reactions due to their ability to achieve and maintain elevated pressure levels.
Benefits of High Pressure Batch Reactors in Hydrogenation:
1. Enhanced Mass Transfer: High pressure conditions improve the solubility of hydrogen gas, allowing for increased reactant contact and faster reaction rates. This leads to higher conversion rates and improved product yields.
2. Increased Reaction Selectivity: Hydrogenation reactions can often result in multiple products due to varying degrees of unsaturation. By carefully controlling pressure and temperature, high pressure batch reactors enable better selectivity, producing the desired product with minimal byproducts.
3. Reduced Side Reactions: Some hydrogenation reactions can lead to undesired side reactions, such as overhydrogenation. High pressure batch reactors allow for precise control over reaction conditions, minimizing side reactions and optimizing the desired reaction pathway.
4. Efficient Heat Transfer: Hydrogenation reactions are exothermic, releasing significant heat. High pressure batch reactors employ efficient heat transfer mechanisms to control temperature and prevent thermal runaway, ensuring safe and controlled reactions.
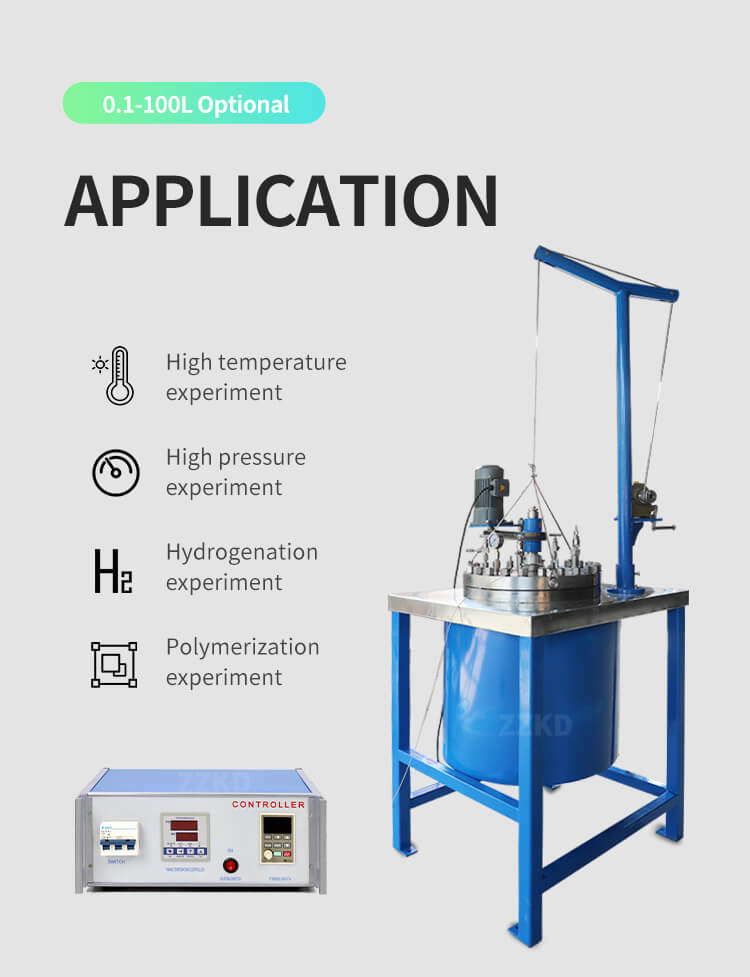
Process Optimization and Yield Improvement:
High pressure batch reactors enable researchers to optimize the hydrogenation process by systematically varying reaction parameters, such as pressure, temperature, catalyst type, and concentration. This optimization leads to improved reaction kinetics, higher yields, and reduced reaction times. Additionally, the ability to perform multiple experiments in a single vessel allows for rapid screening of different catalysts and reaction conditions, accelerating the development of efficient hydrogenation processes.
Industrial Implementation and Success Stories:
High pressure batch reactors have found extensive use in industrial scale hydrogenation processes. One notable example is the production of hydrogenated vegetable oils, where high pressure batch reactors have replaced traditional batch reactors due to their enhanced mass transfer capabilities and improved product quality. Other applications include the hydrogenation of pharmaceutical intermediates, leading to the production of drugs with improved stability and bioavailability.
IV. Advantages of High Pressure Batch Reactors
Enhanced Mass and Heat Transfer:
High pressure batch reactors offer superior mass transfer characteristics, allowing for better reactant mixing and increased reaction rates. Elevated pressure levels enhance the solubility of gases, such as hydrogen, leading to improved gas liquid interactions. Additionally, efficient heat transfer mechanisms within the reactor ensure optimal temperature control, preventing hot spots and thermal gradients.
Increased Product Yield:
Precise control over reaction conditions, such as pressure, temperature, and catalyst selection, enables high pressure batch reactors to achieve higher product yields. Optimization of these parameters reduces undesired side reactions, improves selectivity, and enhances the overall efficiency of the process. The ability to perform multiple experiments in a single reactor vessel facilitates rapid screening and optimization, leading to further yield improvements.
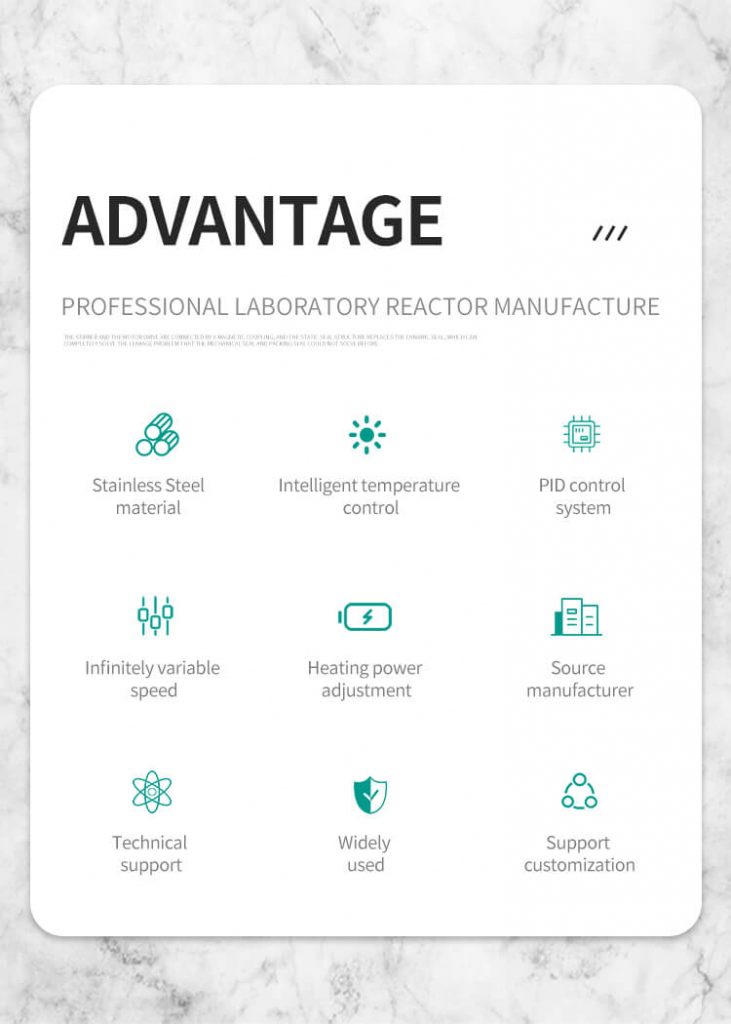
Improved Safety and Control:
High pressure batch reactors are designed with safety as a primary consideration. They incorporate various safety features, such as relief valves, rupture disks, and pressure monitoring systems, to ensure safe operation under high pressure conditions. Additionally, the closed system design minimizes the risk of exposure to hazardous reactants, providing a controlled and safe environment for operators.
Expanded Reaction Space:
The ability to operate under high pressure conditions significantly expands the reaction space, allowing for the exploration of new reaction pathways and the synthesis of novel compounds. High pressure batch reactors enable researchers to investigate the influence of pressure on reaction selectivity, kinetics, and equilibrium, providing valuable insights into reaction mechanisms and driving innovation in chemical synthesis.
V. Considerations in High Pressure Batch Reactor Usage
Material Selection and Compatibility:
Selecting appropriate materials for high pressure batch reactors is crucial to ensure compatibility with the reactants, pressure levels, and temperature ranges. Materials must exhibit high strength, corrosion resistance, and suitability for the specific reaction conditions. Common materials include stainless steel, Hastelloy, and titanium alloys. Careful consideration of material compatibility is essential to prevent corrosion, leakage, and unwanted reactions.
Reactor Scale up and Automation:
When transitioning from laboratory scale to industrial scale processes, reactor scale up becomes a critical consideration. Factors such as heat transfer, mixing efficiency, and pressure control need to be carefully evaluated to maintain process efficiency and product quality. Automation of high pressure batch reactors also improves process control and repeatability, allowing for precise monitoring and adjustment of reaction parameters.
Reaction Optimization and Monitoring:
Optimizing high pressure batch reactions requires systematic variation of key parameters, such as pressure, temperature, reactant concentration, and catalyst loading. Real time monitoring of reaction progress through analytical techniques, such as spectroscopy or chromatography, aids in understanding reaction kinetics, identifying intermediates, and determining the optimal reaction conditions. Continuous optimization ensures maximum product yield and process efficiency.
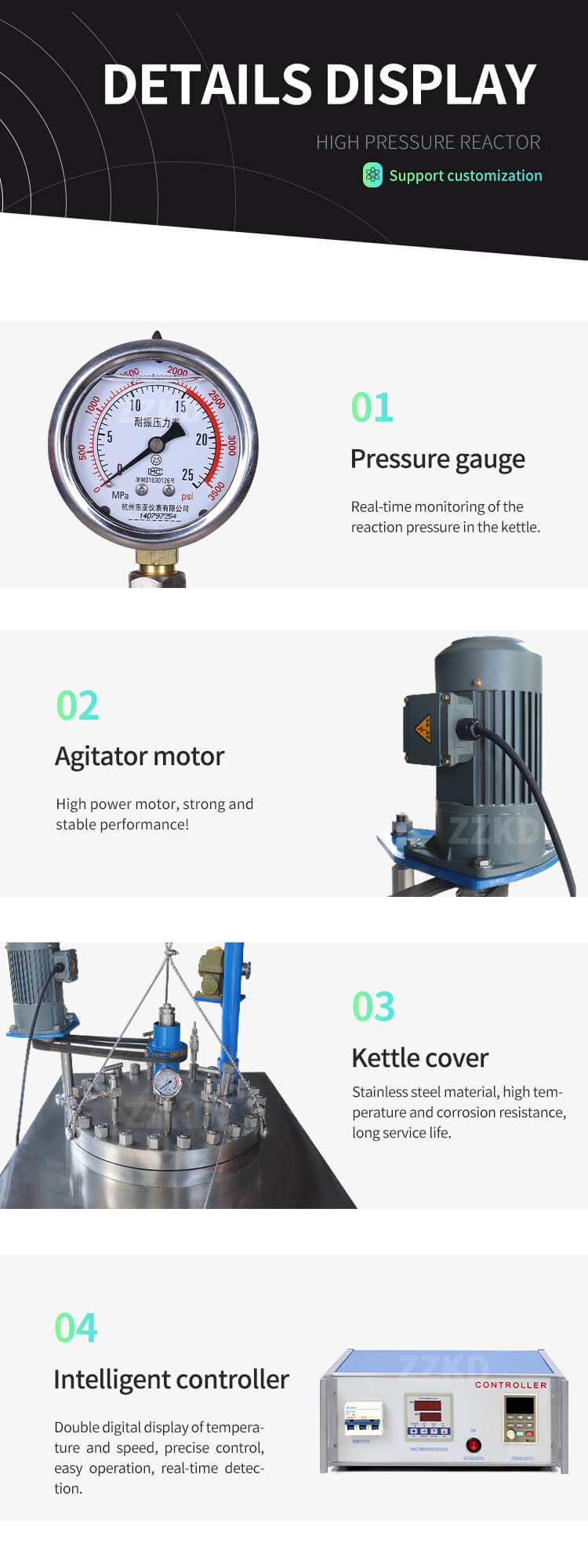
Maintenance and Troubleshooting:
Regular maintenance and periodic inspections of high pressure batch reactors are crucial to ensure long term reliability and safe operation. Components such as seals, gaskets, and pressure relief devices should be checked and replaced if necessary. Troubleshooting issues, such as leaks or pressure deviations, require prompt investigation to identify the root cause and prevent potential hazards. Proper training of personnel in maintenance procedures and troubleshooting protocols is essential.
VI. Future Developments and Emerging Trends
Continuous Flow Systems:
While high pressure batch reactors have been widely used, there is a growing interest in continuous flow systems. Continuous flow reactors offer several advantages, including improved heat and mass transfer, precise control over residence times, and scalability. Integration of high pressure continuous flow systems with online analytics and automation holds tremendous potential for efficient and sustainable chemical synthesis.
Integration of Artificial Intelligence and Machine Learning:
The integration of artificial intelligence (AI) and machine learning (ML) techniques in high pressure batch reactors can revolutionize process optimization and control. AI algorithms can analyze vast amounts of data, identify reaction patterns, and suggest optimal reaction conditions for improved yield and selectivity. ML models can learn from experimental data to predict reaction outcomes and facilitate the development of new catalytic systems.
Sustainable and Green Chemistry Applications:
High pressure batch reactors have a significant role to play in advancing sustainable and green chemistry practices. By enabling precise control over reaction conditions, they facilitate the development of more sustainable processes with reduced energy consumption, waste generation, and environmental impact. High pressure batch reactors contribute to the synthesis of greener solvents, catalysts, and materials, leading to a more sustainable chemical industry.
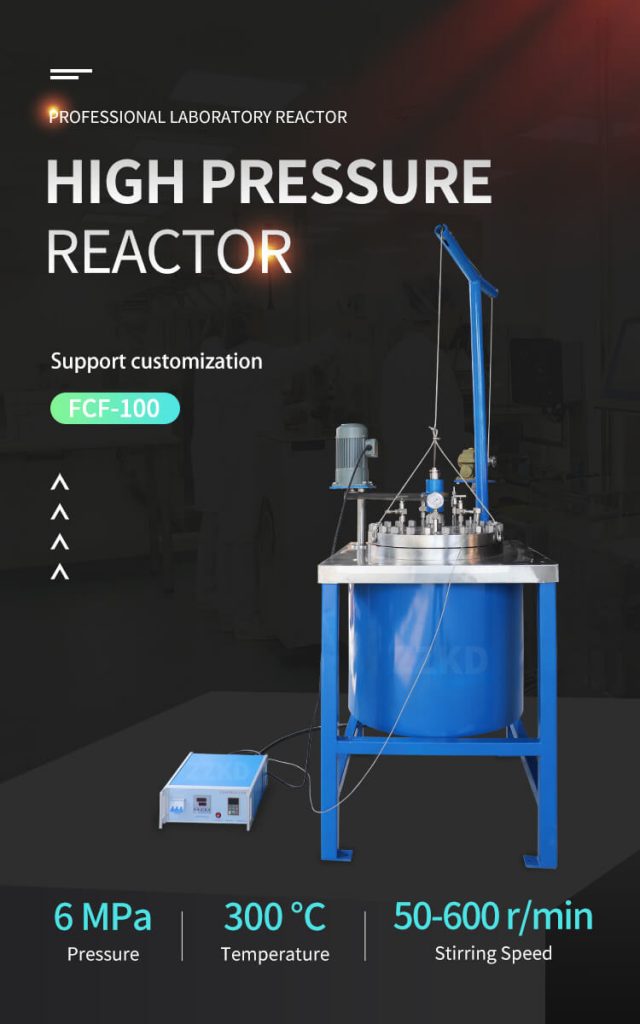
Miniaturization and Portable Reactors:
The miniaturization of high pressure batch reactors offers advantages in terms of reduced reaction volumes, faster heat transfer, and increased safety. Portable reactors allow for on site or remote reactions, reducing transportation costs and enabling decentralized chemical production. Miniaturized and portable high pressure batch reactors find applications in areas such as on demand chemical synthesis, point of care pharmaceutical production, and field based chemical analysis.
VII. Conclusion
High pressure batch reactors are versatile tools that have revolutionized the field of chemical engineering. Their ability to operate under elevated pressure conditions enables precise control over reactions, leading to enhanced safety, improved efficiency, and expanded possibilities in chemical synthesis. From catalysis studies to industrial applications, high pressure batch reactors have proven their value in various domains. By continually advancing their design, optimizing processes, and integrating emerging technologies, researchers and engineers can unlock new opportunities for innovation and sustainability in the chemical industry.