The stainless steel lab reactor has emerged as a crucial tool in various scientific disciplines, facilitating a wide range of experiments and research. With its robust construction and exceptional chemical resistance, this versatile equipment has revolutionized the field of chemical engineering, pharmaceutical development, and materials science. In this article, we will explore the key features, applications, and advancements of stainless steel lab reactors, shedding light on their significance in modern scientific endeavors.
I. Understanding Stainless Steel Lab Reactor
Stainless steel lab reactors are specialized vessels designed for conducting controlled chemical reactions in laboratory settings. These reactors are predominantly fabricated using high-grade stainless steel alloys, known for their exceptional durability and resistance to corrosion. This construction ensures that the reactor can withstand a variety of chemicals, high pressures, and temperatures, making it a reliable apparatus for a wide range of applications.
Key Components of a Stainless Steel Lab Reactor
A stainless steel lab reactor comprises several integral components that facilitate efficient operation and accurate control of the reaction. These components include:
1.1. Vessel: The primary body of the reactor, usually cylindrical in shape, where the reaction takes place. It is constructed using high-quality stainless steel to ensure resistance to chemical corrosion and thermal stress.
1.2. Agitator: The agitator, or stirrer, assists in mixing the reactants evenly and promoting efficient heat transfer during the reaction process. It is typically driven by a motor and consists of various impellers or blades, designed to suit different types of reactions.
1.3. Heating and Cooling Systems: Stainless steel lab reactors incorporate sophisticated temperature control systems, such as external jackets, internal coils, or circulating fluids, to heat or cool the reaction as required. This allows precise regulation of the reaction conditions.
1.4. Pressure Control System: To handle reactions requiring high pressures, stainless steel lab reactors are equipped with pressure control systems, including pressure gauges, relief valves, and safety measures to ensure operator safety.
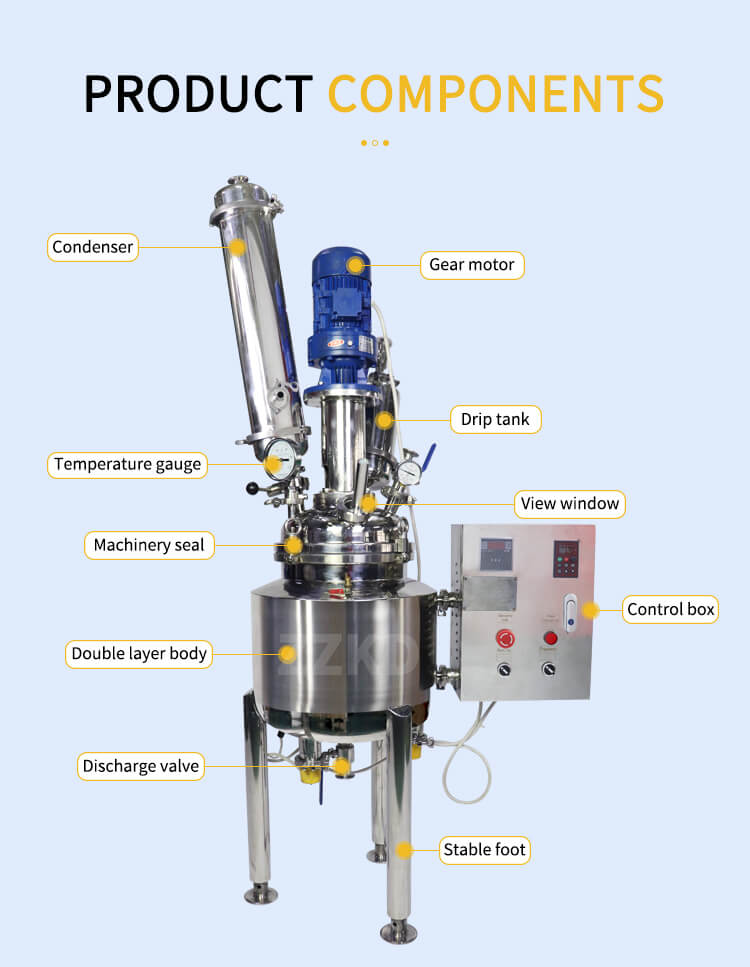
II. Applications of Stainless Steel Lab Reactors
2.1. Chemical Synthesis and Process Development
Stainless steel lab reactors play a vital role in chemical synthesis and process development, allowing scientists to study and optimize reactions under controlled conditions. They enable the synthesis of new compounds, evaluation of reaction kinetics, and scale-up of chemical processes for industrial applications. These reactors are extensively used in pharmaceutical, petrochemical, and fine chemical industries for manufacturing drugs, polymers, and specialty chemicals.
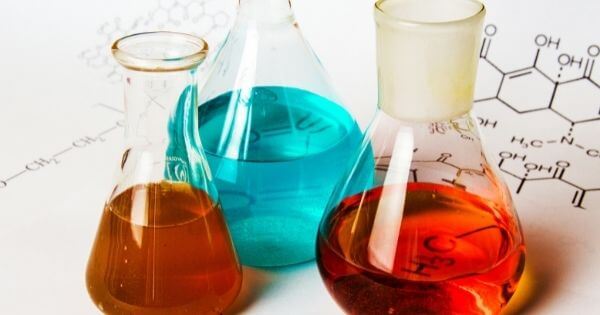
2.2. Catalysis and Materials Science
The field of catalysis heavily relies on stainless steel lab reactors to study and develop efficient catalysts. These reactors enable researchers to investigate catalytic reactions, such as hydrogenation, oxidation, and polymerization, providing insights into reaction mechanisms and catalyst performance. Moreover, stainless steel reactors find applications in materials science, where they are employed for the synthesis and characterization of nanomaterials, catalyst supports, and functional coatings.
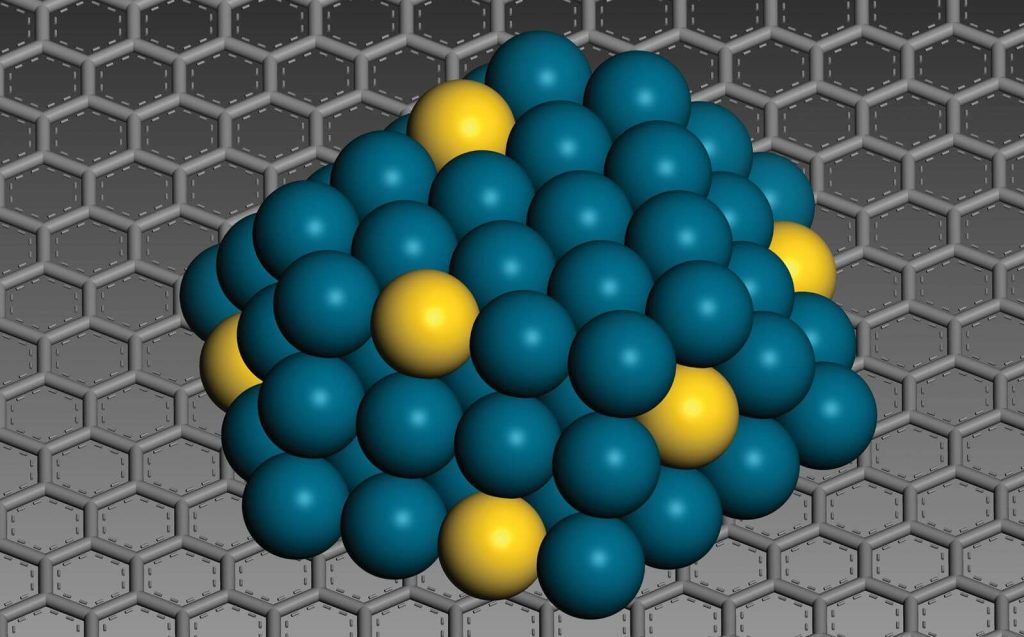
2.3. Biotechnology and Pharmaceutical Development
In biotechnology and pharmaceutical research, stainless steel lab reactors are indispensable tools for various applications. They are utilized in the production of vaccines, antibiotics, and enzymes, as well as in the development of biopolymers and biofuels. Stainless steel reactors facilitate precise control over bioreactor conditions, such as temperature, pH, and dissolved oxygen, enabling optimal growth of microorganisms and cell cultures.
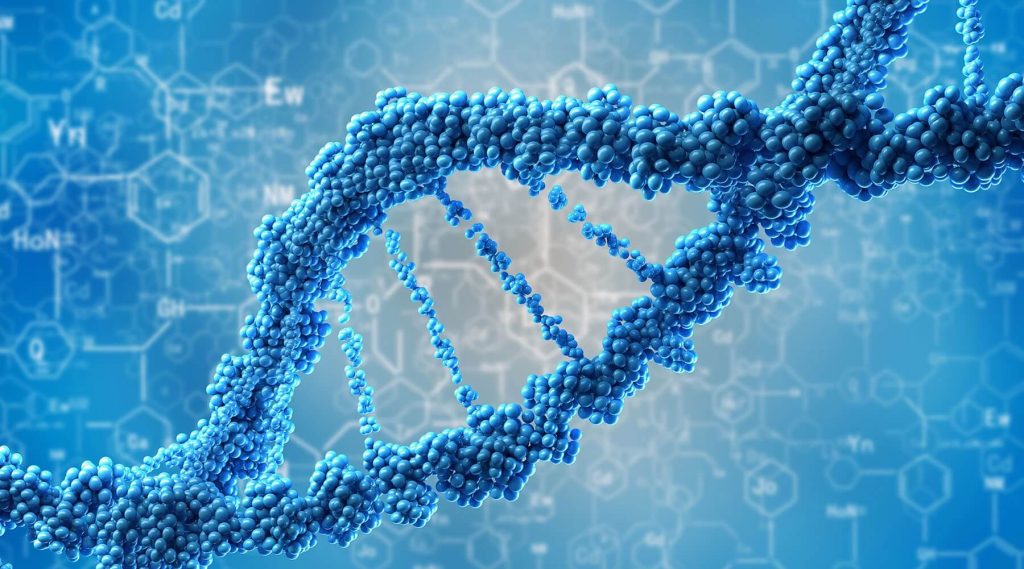
III. Advancements in Stainless Steel Lab Reactors
3.1. Enhanced Safety and Automation Features
Modern stainless steel lab reactors incorporate advanced safety features and automation capabilities, making them more user-friendly and efficient. Safety enhancements include pressure relief systems, emergency shut-off mechanisms, and automatic control of critical parameters. Additionally, advanced automation allows for real-time monitoring, data acquisition, and precise control of reaction conditions, ensuring reproducibility and minimizing human error.
3.2. Innovative Design and Construction
Recent advancements in design and construction techniques have resulted in the development of stainless steel lab reactors with improved performance and reliability. Manufacturers are utilizing advanced computer-aided design (CAD) software and simulation tools to optimize reactor geometry, agitator configurations, and heat transfer efficiency. Furthermore, the use of innovative welding techniques and high-quality stainless steel alloys enhances the durability, chemical resistance, and pressure-bearing capacity of these reactors.
3.3. Integration of Process Analytical Technology (PAT)
The integration of Process Analytical Technology (PAT) in stainless steel lab reactors has revolutionized reaction monitoring and control. PAT involves the real-time analysis of critical process parameters, such as temperature, pressure, pH, and concentration, using various spectroscopic and analytical techniques. By providing continuous feedback, PAT enables researchers to monitor reaction progress, detect deviations, and make necessary adjustments in real-time, leading to improved process understanding and efficiency.
The stainless steel lab reactor is a crucial tool in various scientific disciplines, enabling diverse experiments and research. Its durable construction and chemical resistance revolutionize chemical engineering, pharmaceutical development, and materials science.
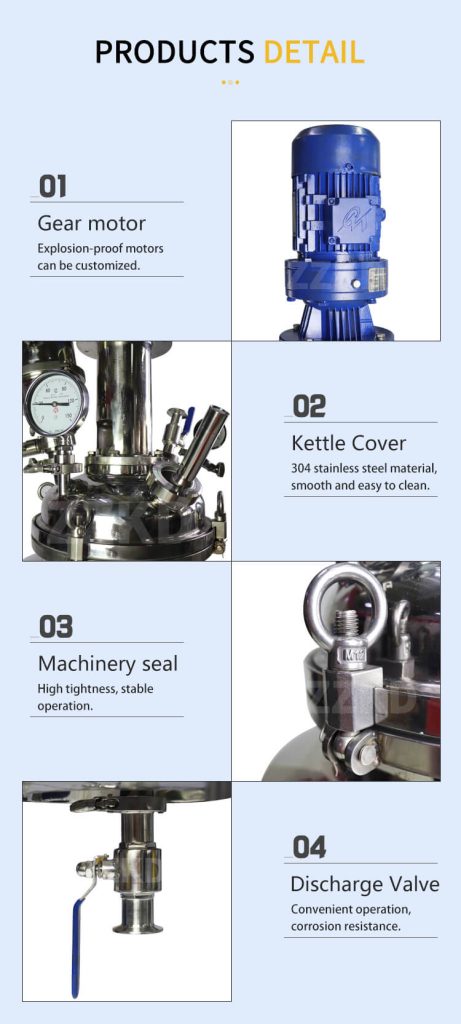
IV.Case: Optimizing Drug Synthesis using a Stainless Steel Lab Reactor
Background:
A pharmaceutical company, PharmaTech Solutions, is in the process of developing a new drug compound with potential therapeutic benefits. The synthesis of this drug involves a complex chemical reaction that requires precise control of reaction conditions, temperature, and pressure. To streamline the process and enhance efficiency, the company decides to utilize a stainless steel lab reactor.
Objectives:
1. Identify optimal reaction conditions for maximum yield and minimal byproducts, ensuring precise control.
2. Streamline the drug synthesis process by reducing reaction time, enhancing overall efficiency.
3. Establish a safe and scalable process that can be replicated in larger production volumes.
4. Improve product quality by fine-tuning reaction parameters and minimizing variability.
5. Enhance process understanding by monitoring critical parameters and analyzing real-time data.
6. Implement advanced technology, such as Process Analytical Technology (PAT), for continuous monitoring and control.
Implementation:
1. Selection of a Stainless Steel Lab Reactor:
PharmaTech Solutions partners with a top lab equipment manufacturer to select a stainless steel lab reactor. The chosen reactor has high-quality stainless steel construction, an advanced agitation system, precise temperature control, and safety features. It ensures compatibility with the chemical reaction and meets safety standards.
2. Experimental Design and Optimization:
The research team designs a series of experiments using the stainless steel lab reactor to investigate the effect of various reaction parameters on the synthesis of the drug compound. They systematically vary temperature, pressure, reactant concentrations, and reaction times to understand their impact on yield, selectivity, and reaction kinetics.
3. Real-Time Monitoring and Data Acquisition:
To monitor the reaction progress and collect crucial data, the stainless steel lab reactor is equipped with advanced sensors and data acquisition systems. These systems enable real-time monitoring of critical parameters such as temperature, pressure, pH, and reaction progress indicators.
4. Integration of Process Analytical Technology (PAT):
The research team integrates Process Analytical Technology (PAT) tools, such as in-line spectroscopy and automated sampling, with the stainless steel lab reactor. This integration allows for continuous monitoring of reaction intermediates, byproduct formation, and impurity profiles. The collected data is analyzed in real-time, providing insights into the reaction kinetics and allowing for immediate adjustments to optimize the process.
5. Optimization and Scale-Up:
Based on the data collected from the experiments, the research team identifies the optimal reaction conditions that yield the highest product purity and yield. They fine-tune parameters such as temperature, reactant stoichiometry, and catalyst concentration to achieve the desired results. The optimized process is then scaled up using larger stainless steel reactors, ensuring consistency and reproducibility in larger production volumes.
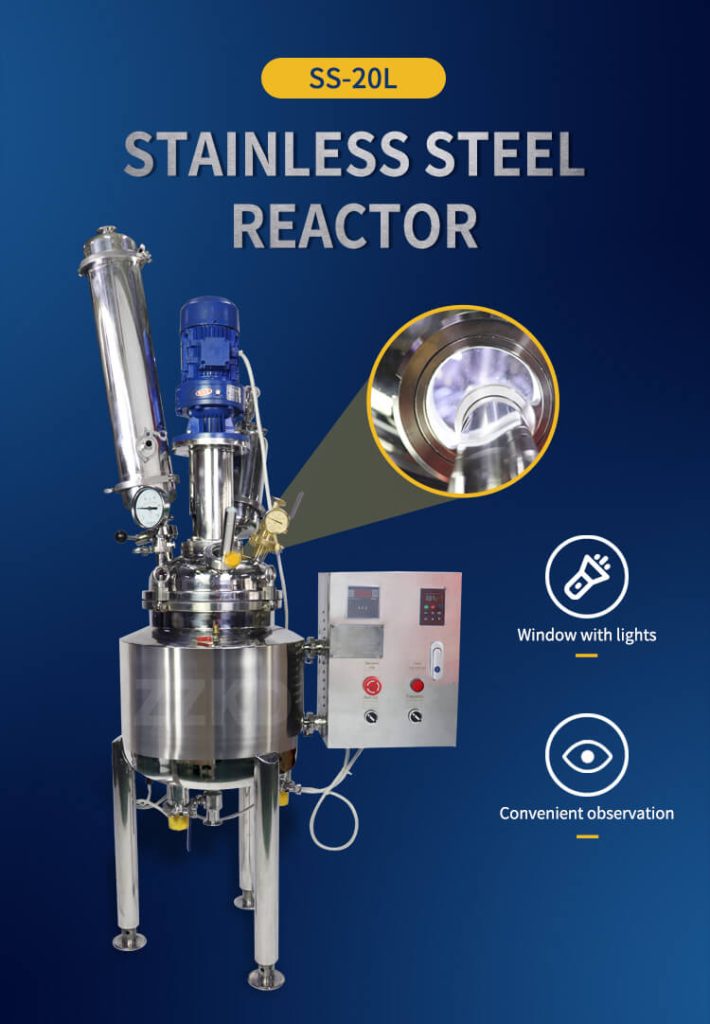
Benefits and Results:
1. Enhanced Yield and Purity:
The use of a stainless steel lab reactor enables precise control of reaction parameters, leading to improved product yield and purity. By optimizing temperature, pressure, and reaction time, PharmaTech Solutions achieves a higher yield of the desired drug compound while minimizing the formation of unwanted byproducts.
2. Reduced Reaction Time:
Through systematic optimization and real-time monitoring, the company successfully reduces the overall reaction time. This improvement translates into increased productivity, cost savings, and faster time-to-market for the new drug.
3. Safety and Scalability:
The incorporation of advanced safety features and strict adherence to safety protocols ensures a safe working environment for researchers. Additionally, the scalability of the optimized process allows for efficient transition from lab-scale synthesis to larger production volumes, meeting the future demands of the pharmaceutical market.
4. Process Understanding and Control:
The integration of Process Analytical Technology (PAT) tools provides valuable insights into the reaction kinetics and critical process parameters. This enhanced process understanding enables researchers to make informed decisions, troubleshoot issues in real-time, and maintain control over the synthesis process.
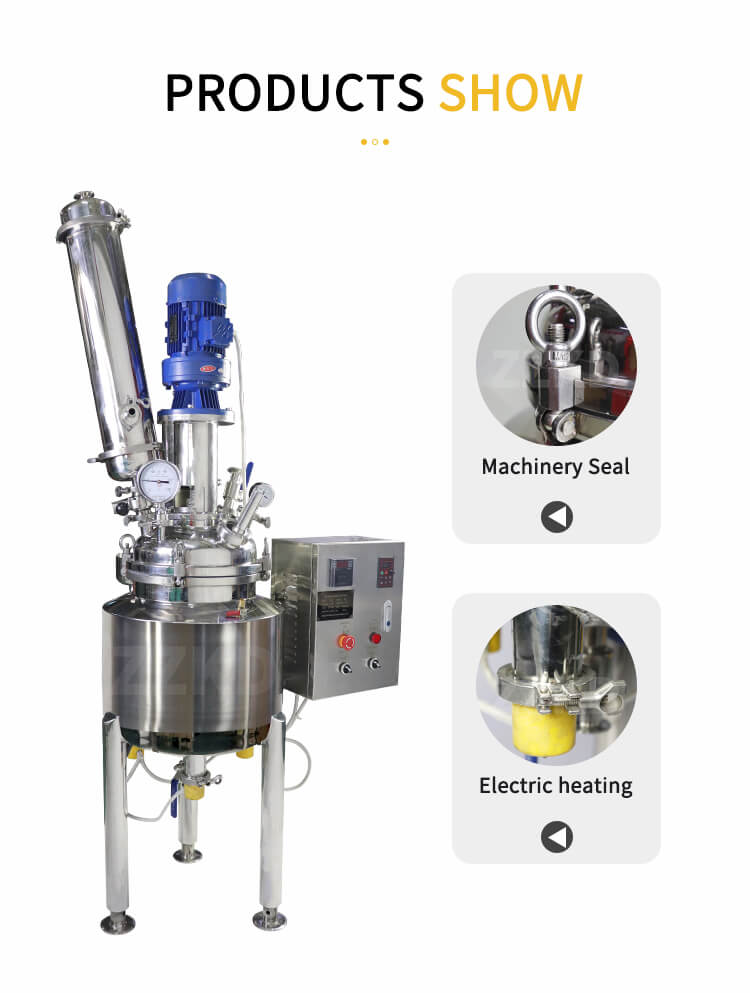
PharmaTech Solutions successfully utilizes a stainless steel lab reactor in the optimization of a complex drug synthesis process. The integration of advanced technology, real-time monitoring, and process optimization techniques enables the company to achieve higher product yields, improved purity, and reduced reaction times. The stainless steel lab reactor proves to be an essential tool in the pharmaceutical industry, facilitating efficient process development, scalability, and adherence to safety standards. Through the application of stainless steel lab reactors, pharmaceutical companies can enhance their research and development efforts, ultimately leading to the discovery and production of life-saving drugs.