High-pressure reactor vessels play a crucial role in various industries, enabling the safe and efficient execution of chemical reactions and processes under extreme conditions. Designed to withstand high pressures and temperatures, these vessels find applications in a wide range of sectors, from pharmaceuticals to petrochemicals and beyond. This article delves into the intricacies of high-pressure reactor vessels, exploring their working principles, applications, and analyzing the current market trends.
I. Understanding High Pressure Reactor Vessels
A. Definition and Working Principles:
High-pressure reactor vessels, also known as autoclaves or pressure vessels, are specialized containers designed to handle reactions and processes at elevated pressures and temperatures. They are built to withstand the stresses induced by high internal pressures, typically ranging from a few hundred to several thousand pounds per square inch (psi). These vessels are constructed using robust materials, such as stainless steel or other alloys, to ensure durability and resistance to corrosion.
The working principle of a high-pressure reactor vessel involves creating a sealed environment where reactants can undergo chemical reactions or physical processes under controlled conditions. By increasing the pressure, the vessel allows for higher reaction rates, improved yield, and selectivity in certain cases. Temperature control systems, such as heating or cooling jackets, are often integrated into these vessels to maintain precise process conditions.
B. Components and Construction:
High-pressure reactor vessel consist of several key components:
– Shell: The main body of the vessel, typically cylindrical in shape, houses the reactants and provides structural integrity.
– Head or Closure: The top and bottom ends of the vessel, which are tightly sealed to prevent any leakage or loss of pressure.
– Agitation System: Stirrers, impellers, or magnetic stir bars are used to facilitate mixing and enhance reaction kinetics.
– Heat Transfer System: Heating and cooling jackets or coils ensure precise temperature control during the process.
– Pressure Relief Devices: Safety valves, rupture discs, and pressure gauges are incorporated to prevent over-pressurization.
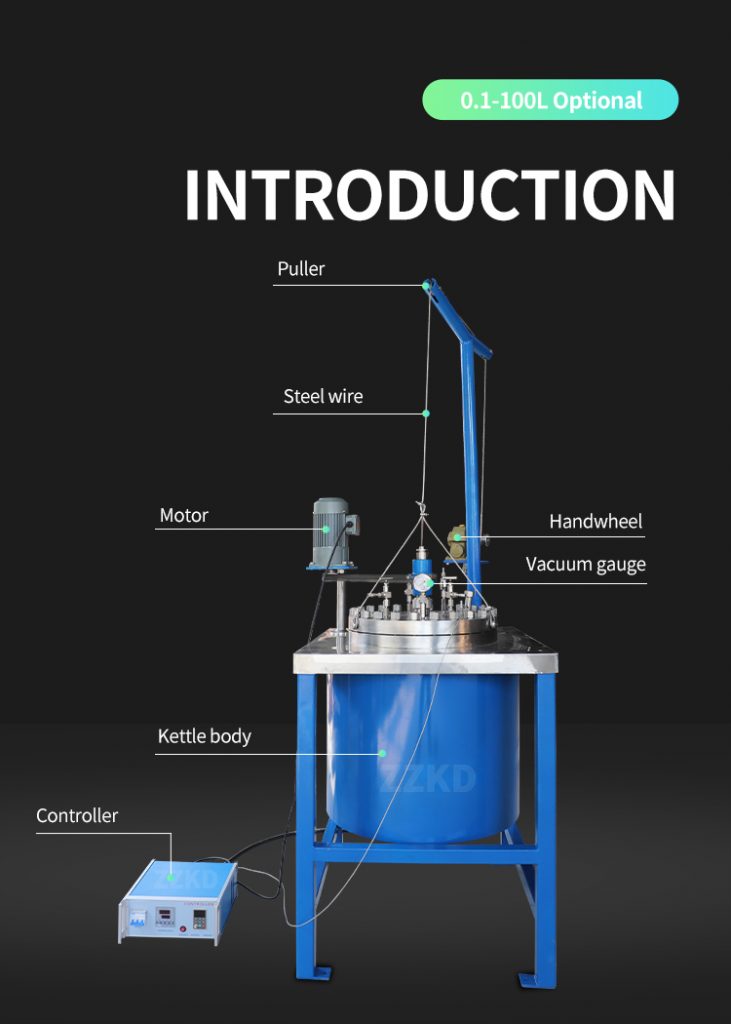
C. Safety Measures and Regulations:
Operating high-pressure reactor vessels involves inherent risks. To ensure safety, strict adherence to established regulations and guidelines is crucial. Regulatory bodies, such as the American Society of Mechanical Engineers (ASME) in the United States and various national and international standards organizations, provide codes and standards for the design, fabrication, and operation of pressure vessels. Regular inspections, maintenance, and appropriate safety protocols minimize the chances of accidents and ensure the well-being of personnel and the environment.
II. Applications of High Pressure Reactor Vessels
A. Chemical Synthesis and Catalysis:
High-pressure reactor vessel find extensive use in chemical synthesis and catalytic processes. They enable the synthesis of complex compounds by providing the necessary conditions of elevated pressure and temperature. These vessels facilitate reactions that are otherwise challenging or impossible to achieve at ambient conditions. High-pressure conditions often enhance reaction rates, alter equilibrium positions, and increase product yields, making them indispensable in the pharmaceutical, petrochemical, and specialty chemical industries.
B. Polymerization Reactions:
Polymerization reactions, such as the production of plastics, rubber, and fibers, often require high-pressure conditions. High-pressure reactor vessels provide the controlled environment necessary for efficient polymerization processes. By optimizing temperature and pressure, these vessels enable the formation of long polymer chains with desired properties, ensuring product quality and performance.
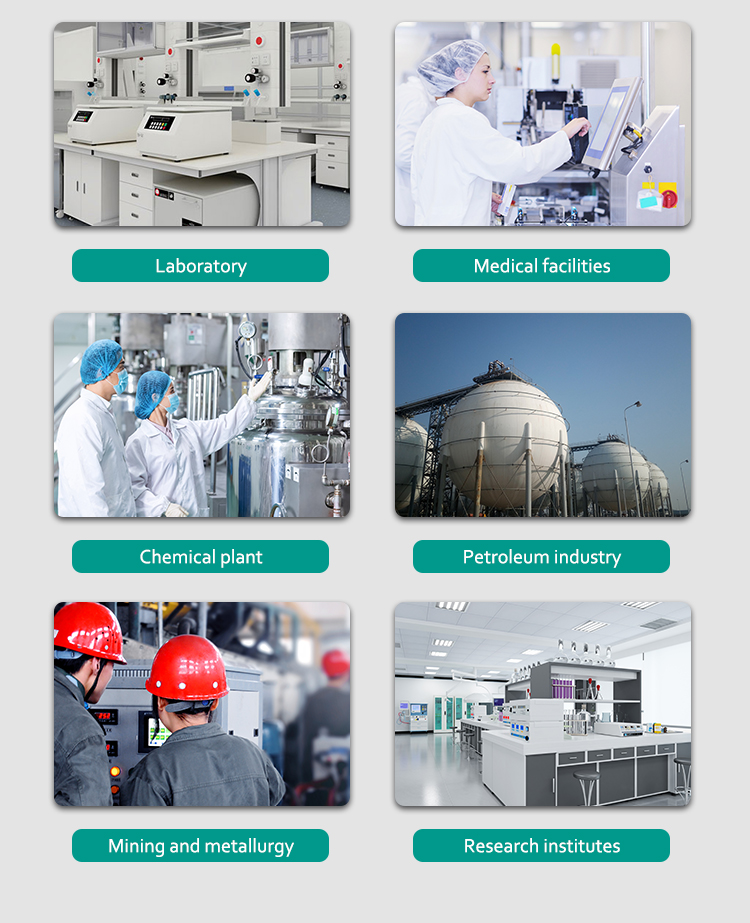
C. Hydrogenation and Oxidation Processes:
Hydrogenation and oxidation reactions, widely employed in the production of fine chemicals, pharmaceutical intermediates, and fuel additives, often require high-pressure conditions. High-pressure reactor vessels enable precise control over reaction parameters, enhancing the efficiency and selectivity of these processes. Hydrogenation, for example, involves the addition of hydrogen to unsaturated compounds under elevated pressure and temperature, allowing the conversion of precursors into valuable products.
D. Material Testing and Development:
High-pressure reactor vessel serve as essential tools for material testing and development. Researchers and engineers utilize these vessels to simulate extreme conditions that materials may encounter during their applications. These tests provide valuable insights into material behavior, durability, and performance under high-pressure and high-temperature environments. Such data aids in the design and development of materials for aerospace, automotive, and other industries.
E. Supercritical Fluid Extraction:
Supercritical fluid extraction (SFE) involves the extraction of desired compounds using supercritical fluids, which exhibit both liquid and gas properties. High-pressure reactor vessels provide the necessary conditions for supercritical fluid extraction processes, offering advantages such as enhanced solubility, selective extraction, and reduced solvent usage. This technique is widely employed in the extraction of natural products, flavors, fragrances, and pharmaceutical compounds.
F. Other Specialized Applications:
High-pressure reactor vessels have diverse applications beyond those mentioned above. They are used in areas such as waste treatment, environmental remediation, nanomaterial synthesis, and carbon capture and storage. The flexibility and versatility of high-pressure reactor vessels make them invaluable tools across numerous industries.
III. Case : High Pressure Reactor Vessel in Pharmaceutical Industry
A. Overview of Pharmaceutical Applications:
The pharmaceutical industry extensively utilizes high-pressure reactor vessels due to the complex nature of drug synthesis and the need for precise control over reaction conditions. High-pressure vessels enable the synthesis of active pharmaceutical ingredients (APIs), intermediate compounds, and advanced drug delivery systems. The use of high pressures allows for improved reaction kinetics, reduced reaction times, and enhanced product quality.
B. Application Case: Synthesis of Active Pharmaceutical Ingredients (APIs)
1. Background and Importance:
Active Pharmaceutical Ingredients (APIs) are the core components responsible for the therapeutic effects of drugs. The synthesis of APIs often involves complex reactions and requires specific conditions for optimal yield and purity. High-pressure reactor vessels provide a controlled environment for the synthesis of APIs, allowing pharmaceutical manufacturers to produce high-quality drugs efficiently.
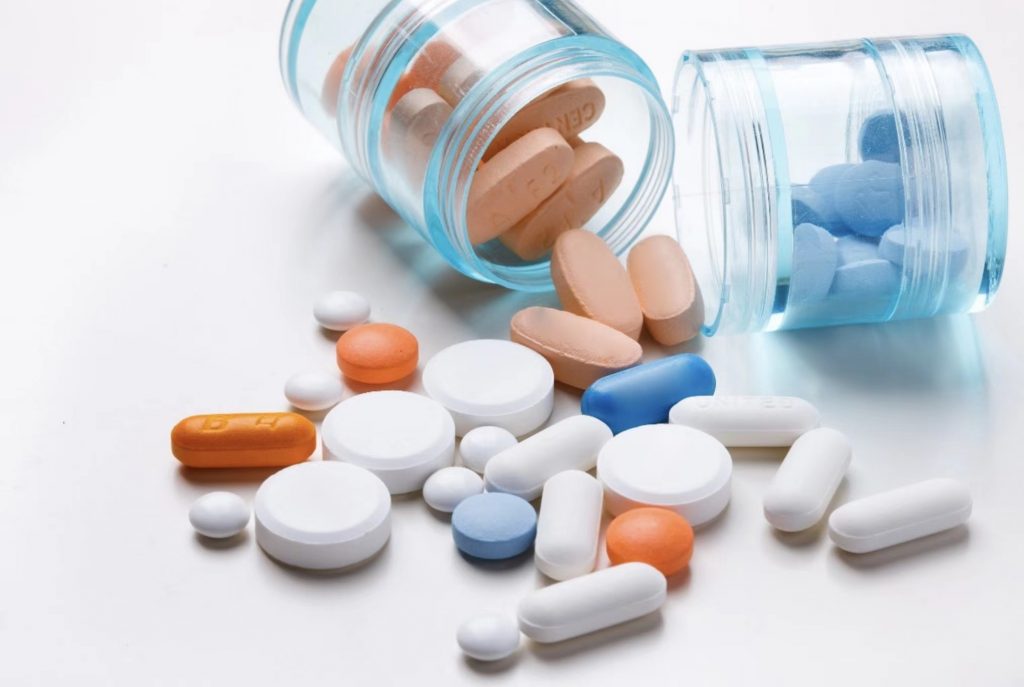
2. Process Description:
In the synthesis of APIs, high-pressure reactor vessels enable chemists to perform reactions that require elevated pressures and temperatures. These vessels accommodate various reaction types, including hydrogenation, oxidation, and condensation reactions. By maintaining precise pressure and temperature parameters, chemists can control reaction rates, selectivity, and the formation of desired products.
3. Benefits of High Pressure Reactor Vessels in API Synthesis:
High-pressure reactor vessels offer several advantages in API synthesis:
a. Improved Reaction Kinetics: High-pressure conditions enhance reaction rates, allowing for faster synthesis and increased productivity.
b. Enhanced Yield and Selectivity: High pressures can shift equilibrium positions, favoring the formation of desired products and improving overall yield and selectivity.
c. Reduction in Side Reactions: High-pressure environments often suppress unwanted side reactions, leading to higher purity of the final API.
d. Energy Efficiency: High-pressure reactions may require less energy input, resulting in cost savings and reduced environmental impact.
4. Success Story: Improved Efficiency and Safety:
One notable success story in API synthesis involves the production of a life-saving drug used to treat a rare genetic disorder. The pharmaceutical company faced challenges in synthesizing the API due to its complex molecular structure and the requirement for high-pressure conditions. By implementing a high-pressure reactor vessel, the company achieved improved reaction efficiency, significantly reducing the production time and increasing API yield. Moreover, the use of high-pressure vessels enhanced safety by minimizing the risks associated with handling hazardous reactants at higher pressures.
IV. Market Analysis of High Pressure Reactor Vessels
A. Current Market Overview:
The market for high-pressure reactor vessel has witnessed substantial growth in recent years. The increasing demand for specialty chemicals, pharmaceuticals, and advanced materials, coupled with the growing need for efficient and sustainable manufacturing processes, drives the market’s expansion. The market players offer a diverse range of high-pressure reactor vessels catering to various industries and applications.
B. Market Segmentation by End-Use Industry:
The high-pressure reactor vessel market can be segmented based on end-use industries:
1. Pharmaceuticals: The pharmaceutical industry holds a significant share in the market, driven by the demand for APIs, drug intermediates, and specialized drug delivery systems.
2. Petrochemicals: High-pressure reactor vessels find extensive application in the petrochemical sector for the synthesis of chemicals, polymers, and refining processes.
3. Chemicals: Chemical manufacturers utilize high-pressure reactor vessels for diverse chemical reactions, including specialty chemical synthesis and process optimization.
4. Food and Beverage: High-pressure processing techniques, facilitated by reactor vessels, enable food preservation, extraction, and enhancement of product quality.
5. Others: The market also caters to industries such as research and development, environmental engineering, and academic institutions.
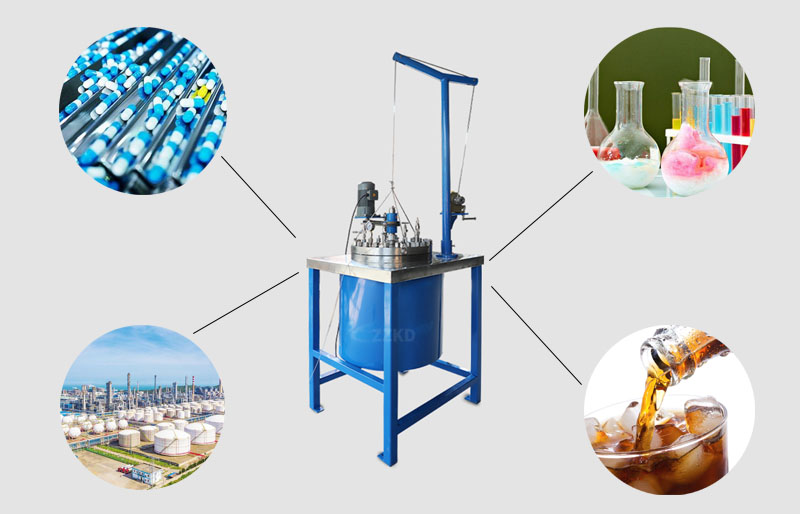
C. Regional Analysis:
The market for high-pressure reactor vessels is geographically diverse, with key regions including:
1. North America: The region has a well-established pharmaceutical and chemical industry, driving the demand for high-pressure reactor vessels.
2. Europe: Europe boasts a strong presence of chemical and petrochemical industries, contributing to the market growth.
3. Asia Pacific: The rapid industrialization, particularly in countries like China and India, fuels the demand for high-pressure reactor vessels across multiple industries.
4. Latin America: The region demonstrates potential growth opportunities in the pharmaceutical and chemical sectors, creating demand for high-pressure reactor vessels.
5. Middle East and Africa: The presence of a flourishing petrochemical industry and increasing investments in research and development activities contribute to the market expansion.
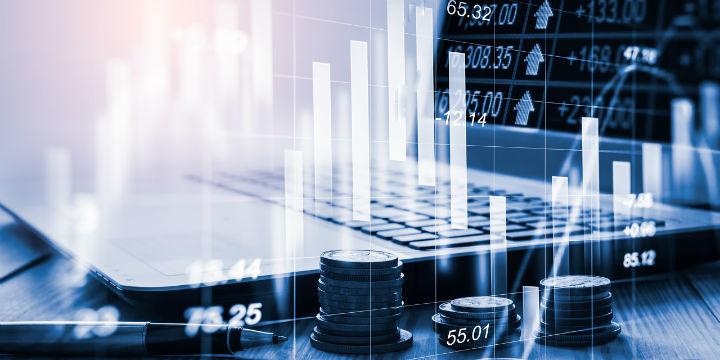
D. Key Market Players and Competitive Landscape:
The market for high-pressure reactor vessels is competitive, with several key players dominating the industry. Prominent market players include established manufacturers, engineering firms, and solution providers offering a wide range of high-pressure reactor vessels. These companies focus on innovation, product development, and strategic partnerships to maintain their market position.
E. Growth Drivers and Challenges:
The growth of the high-pressure reactor vessel market is driven by factors such as:
– Increasing demand for specialty chemicals and pharmaceuticals
– Technological advancements in reactor vessel design and automation
– Growing focus on sustainable manufacturing processes
– Regulatory support and safety standards
However, the market also faces certain challenges:
– High initial costs associated with the procurement and maintenance of high-pressure reactor vessels
– Complexities in scaling up reactions from laboratory to industrial scale
– Safety concerns related to the handling of high-pressure processes
F. Future Market Trends and Opportunities:
The high-pressure reactor vessel market is poised for significant growth and presents several future trends and opportunities:
– Increasing adoption of automated and smart reactor vessels for improved process control and safety
– Integration of advanced materials and coatings for enhanced durability and corrosion resistance
– Rising demand for continuous flow reactor systems for efficient and scalable production
– Expanding applications in emerging sectors, such as renewable energy and green chemistry
– Collaborations between manufacturers and research institutions to drive innovation and technology advancements
V. Conclusion
In conclusion, high-pressure reactor vessels are critical tools that enable a wide range of applications across various industries. Their ability to provide controlled environments for reactions under elevated pressure and temperature conditions is vital for achieving desired outcomes in chemical synthesis, polymerization, material testing, and more. The pharmaceutical industry, in particular, benefits greatly from high-pressure reactor vessels, improving the synthesis of APIs and facilitating the development of life-saving drugs.
The market for high-pressure reactor vessels is experiencing steady growth, driven by the demand for efficient manufacturing processes and the need for specialized chemical products. Regional market dynamics, such as the presence of pharmaceutical and petrochemical industries, influence the market’s growth in different regions. Key market players focus on innovation and strategic collaborations to maintain a competitive edge.
Looking ahead, the high-pressure reactor vessel market holds promising prospects, fueled by technological advancements, sustainability initiatives, and emerging applications. Continued investment in research and development, safety measures, and regulatory compliance will be crucial to unlock the full potential of high-pressure reactor vessels in driving innovation and meeting evolving industry demands.