Stainless steel reactors play a crucial role in various industries, providing a safe and efficient environment for chemical reactions and manufacturing processes. As the demand for high-quality stainless steel reactors continues to rise, numerous manufacturers have emerged to meet these needs. In this article, we will explore the world of stainless steel reactor manufacturers, highlighting their significance, application cases, and market analysis to understand their pivotal role in modern industrial processes.
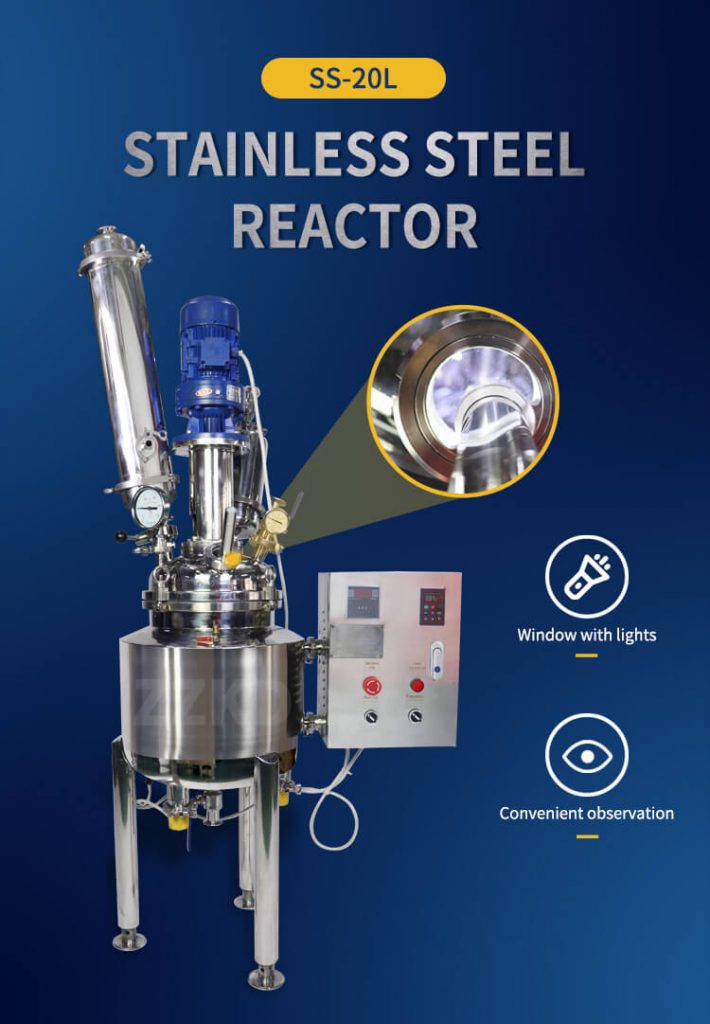
I. The Importance of Stainless Steel Reactors
B. Advantages of Stainless Steel Reactors
C. Industries that Utilize Stainless Steel Reactors
II. Application Case: Petrochemical Industry
A. Overview of the Petrochemical Industry
B. Role of Stainless Steel Reactors in Petrochemical Processes
C. Case: Stainless Steel Reactors in Petrochemical Plant
III. Customization and Specialization: Meeting Unique Industry Requirements
A. Tailoring Reactors to Specific Industrial Processes
B. Design Considerations for Customized Reactors
C. Benefits of Specialized Stainless Steel Reactors
IV. Quality Assurance and Compliance
A. Importance of Quality Standards
B. Compliance with Industry Regulations
C. Quality Control Processes in Stainless Steel Reactor Manufacturing
V. Innovations and Advancements in Stainless Steel Reactor Technology
A. Improved Materials and Construction Techniques
B. Enhanced Safety Features and Automation
C. Integration of IoT and Industry 4.0 Technologies
VI. The Future of Stainless Steel Reactor Manufacturers
A. Growth Opportunities in Emerging Industries
B. Expansion into Global Markets
C. Sustainable Manufacturing Practices
I. The Importance of Stainless Steel Reactors
A. Definition and Components:
Stainless steel reactors are vessels specifically designed for carrying out chemical reactions or manufacturing processes. They are constructed using high-quality stainless steel, which offers excellent corrosion resistance, durability, and thermal stability. The reactors consist of several essential components, including the vessel body, agitators, heating or cooling jackets, baffles, and various ports for adding reactants, removing products, and monitoring process parameters.
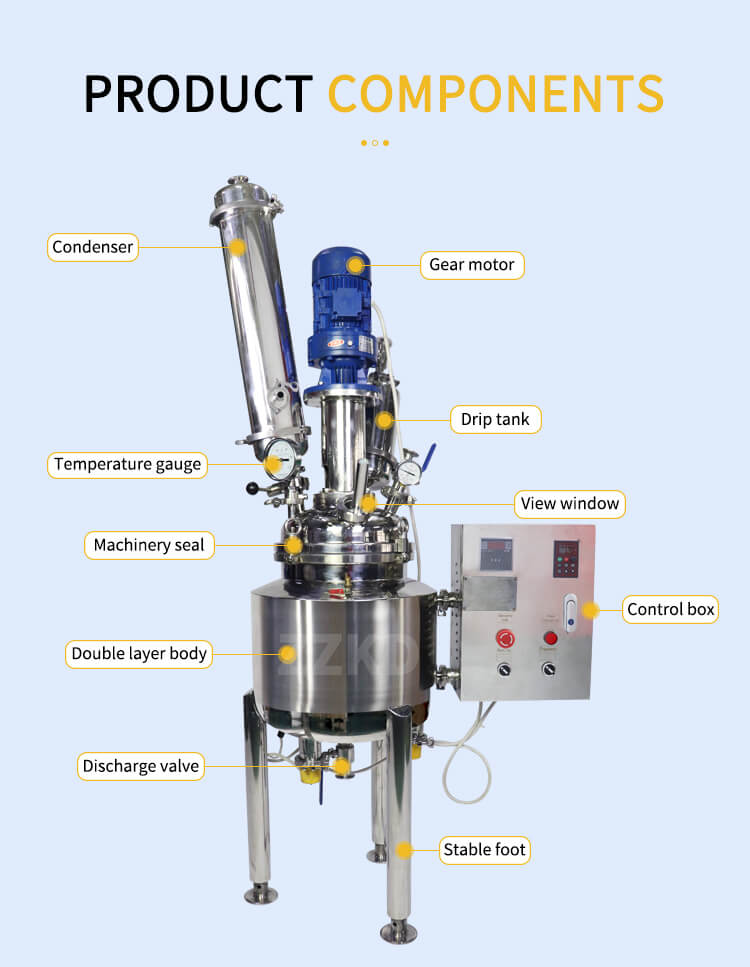
B. Advantages of Stainless Steel Reactors:
Stainless steel reactors offer numerous advantages that make them the preferred choice in various industries. These advantages include:
1. Corrosion Resistance: Stainless steel is known for its exceptional resistance to corrosion, making it suitable for handling corrosive substances and harsh chemicals. This property ensures the longevity and reliability of stainless steel reactors.
2. High Temperature and Pressure Resistance: Stainless steel reactors can withstand high operating temperatures and pressures, making them ideal for processes that require elevated conditions. They provide a secure environment for reactions that involve heat generation or require high-pressure conditions.
3. Hygiene and Cleanability: Stainless steel surfaces are non-porous, smooth, and easy to clean, ensuring high levels of hygiene in industries such as pharmaceuticals and food processing. The material’s non-reactive nature also prevents contamination of the product, ensuring its purity and quality.
4. Versatility: Stainless steel reactors can accommodate a wide range of chemical reactions and processes, including mixing, blending, heating, cooling, and various catalytic reactions. They can utilize their versatile nature in diverse industries, such as petroleum chemicals, pharmaceuticals, food and beverages, chemicals, and polymers.
C. Industries that Utilize Stainless Steel Reactors:
Stainless steel reactors find extensive applications in various industries where chemical reactions or manufacturing processes are conducted. Some prominent industries that rely on stainless steel reactors include:
1. Petrochemical Industry: Petrochemical processes, such as polymerization, hydrogenation, and distillation, heavily depend on stainless steel reactors for their robustness, corrosion resistance, and ability to withstand high temperatures and pressures.
2. Pharmaceutical Industry: Stainless steel reactors play a critical role in pharmaceutical manufacturing, enabling the production of medicines, active pharmaceutical ingredients (APIs), and other specialized chemicals. They ensure sterile conditions, efficient mixing, and precise temperature control to meet stringent quality and safety requirements.
3. Food and Beverage Industry: Stainless steel reactors are utilized in the food and beverage industry for processes such as fermentation, flavor extraction, and the production of additives and ingredients. The material’s hygienic properties and resistance to corrosion make it ideal for maintaining product purity and meeting strict regulatory standards.
4. Chemical Industry: Chemical reactions, such as oxidation, reduction, esterification, and polymer synthesis, require reliable and durable reactors. Chemical manufacturing widely uses stainless steel reactors due to their ability to handle corrosive chemicals and maintain process integrity.
5. Environmental and Energy Sector: Stainless steel reactors are employed in the production of biofuels, biodiesel, and renewable chemicals. These reactors offer high thermal stability, making them suitable for sustainable energy production and eco-friendly processes.
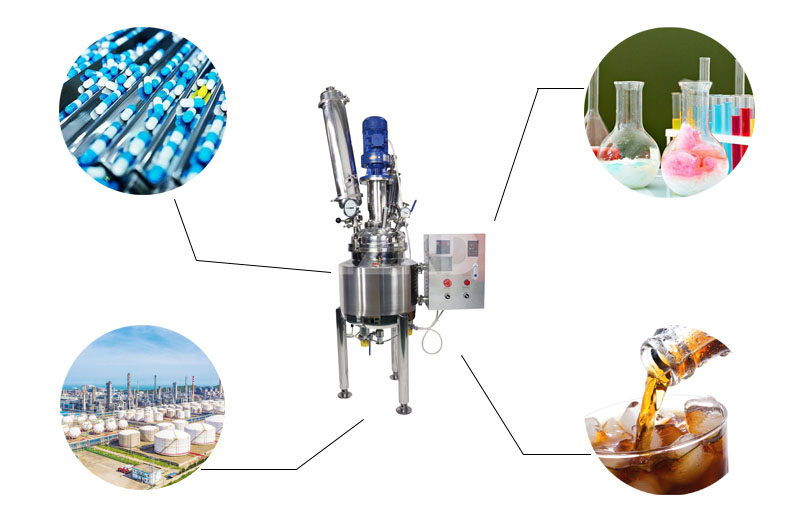
The utilization of stainless steel reactors in these industries highlights their indispensable role in facilitating safe, efficient, and cost-effective manufacturing processes. These reactors contribute to the advancement of industries and drive innovation in various sectors.
II. Application Case: Pharmaceutical Industry
A. Overview of the Pharmaceutical Industry:
The pharmaceutical industry plays a vital role in the development and production of life-saving drugs and medications. It encompasses processes such as synthesis, fermentation, and purification, which require specialized equipment like stainless steel reactors. The industry serves as a critical provider of medicines to improve human health.
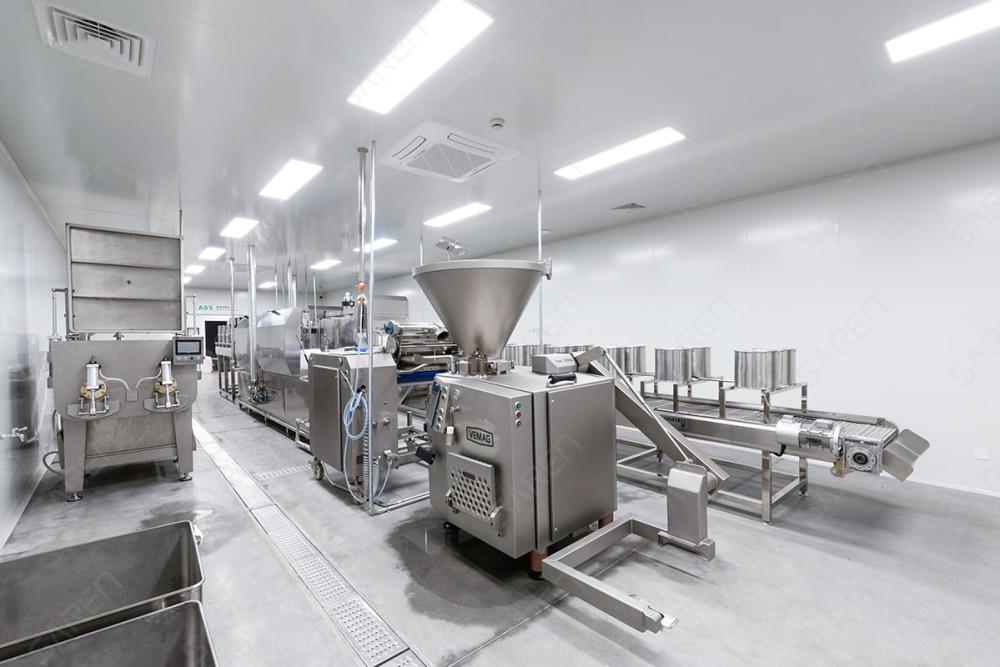
B. Role of Stainless Steel Reactors in Pharmaceutical Processes:
Stainless steel reactors are integral to numerous pharmaceutical processes, providing a controlled environment for chemical reactions and ensuring the production of high-quality pharmaceutical products. Their key roles in the pharmaceutical industry include:
1. Chemical Synthesis: Stainless steel reactors facilitate chemical synthesis processes involved in drug production. They provide a sterile and controlled environment for reactions, ensuring the synthesis of pure and potent pharmaceutical compounds.
2. Fermentation and Bioprocessing: Stainless steel reactors are used in fermentation and bioprocessing, where microorganisms or cells are employed to produce therapeutic proteins, vaccines, or antibiotics. The reactors provide optimal conditions for cell growth, nutrient supply, and efficient product formation.
3. Purification and Separation: Stainless steel reactors equipped with purification systems, such as chromatography columns, are utilized for separating and purifying pharmaceutical compounds. These reactors ensure the removal of impurities and contaminants, resulting in high-quality and safe pharmaceutical products.
4. Sterilization and Aseptic Processing: Stainless steel reactors can be designed for sterilization and aseptic processing, crucial in pharmaceutical manufacturing. These reactors maintain sterile conditions during drug formulation, preventing contamination and ensuring product safety.
C. Case: Stainless Steel Reactors in Pharmaceutical Company:
To illustrate the application of stainless steel reactors in the pharmaceutical industry, let’s consider the case of Pharmaceutical Company. Company X specializes in the production of antibiotics, utilizing advanced manufacturing processes.
At Pharmaceutical Company, stainless steel reactors play a critical role in antibiotic production. The reactors are instrumental in the chemical synthesis of key antibiotic compounds, enabling precise control over reaction parameters to yield pure and potent antibiotics. The stainless steel construction of the reactors ensures compatibility with the pharmaceutical compounds and facilitates easy cleaning and sterilization between batches.
Additionally, industries employ stainless steel reactors with specialized fermentation capabilities for the production of antibiotics through microbial fermentation. These reactors provide a controlled environment for the growth of microorganisms, optimizing yield and product quality. The stainless steel material offers excellent corrosion resistance, ensuring the durability and longevity of the reactors during prolonged fermentation processes.
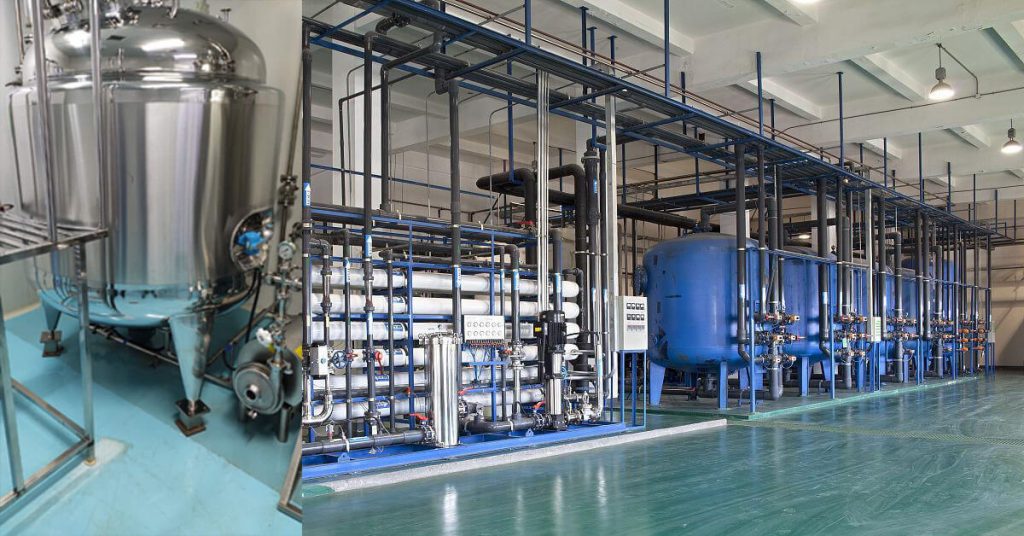
Furthermore, stainless steel reactors with integrated purification systems are utilized in Pharmaceutical Company for the separation and purification of antibiotics. The reactors enable the removal of impurities and contaminants, ensuring the production of high-purity antibiotics with minimal side effects.
The application of stainless steel reactors in Pharmaceutical Company exemplifies their crucial role in ensuring the production of safe and effective pharmaceutical products. These reactors contribute to the manufacturing processes involved in antibiotic production, enabling Pharmaceutical Company to meet the global demand for life-saving medications.
III. Customization and Specialization: Meeting Unique Industry Requirements
A. Tailoring Reactors to Specific Industrial Processes:
Stainless steel reactor manufacturers understand that different industries have unique requirements for their manufacturing processes. To cater to these specific needs, manufacturers offer customization options to tailor reactors accordingly. Customization involves designing and engineering reactors with specific features, dimensions, and capabilities to meet the demands of individual industries.
1. Size and Capacity: Reactor size and capacity can vary significantly based on the scale of the industrial process. Manufacturers can customize reactors to accommodate specific volumes, ensuring optimal utilization of space and efficient production.
2. Agitation Systems: Different chemical reactions require specific agitation mechanisms. Manufacturers can customize the agitators in stainless steel reactors, considering factors such as speed, blade design, and mixing efficiency to ensure effective blending and homogeneity.
3. Heating and Cooling Systems: Industries often require precise temperature control in their processes. Stainless steel reactors can be customized with different heating or cooling systems, such as steam jackets, coils, or external heat exchangers, to achieve the desired temperature profiles and optimize reaction kinetics.
4. Material Selection: While stainless steel is the primary material for reactors, the choice of stainless steel grade can be customized based on the compatibility with the chemicals and process conditions. Manufacturers can recommend and provide reactors constructed from specific stainless steel alloys to enhance corrosion resistance and durability.
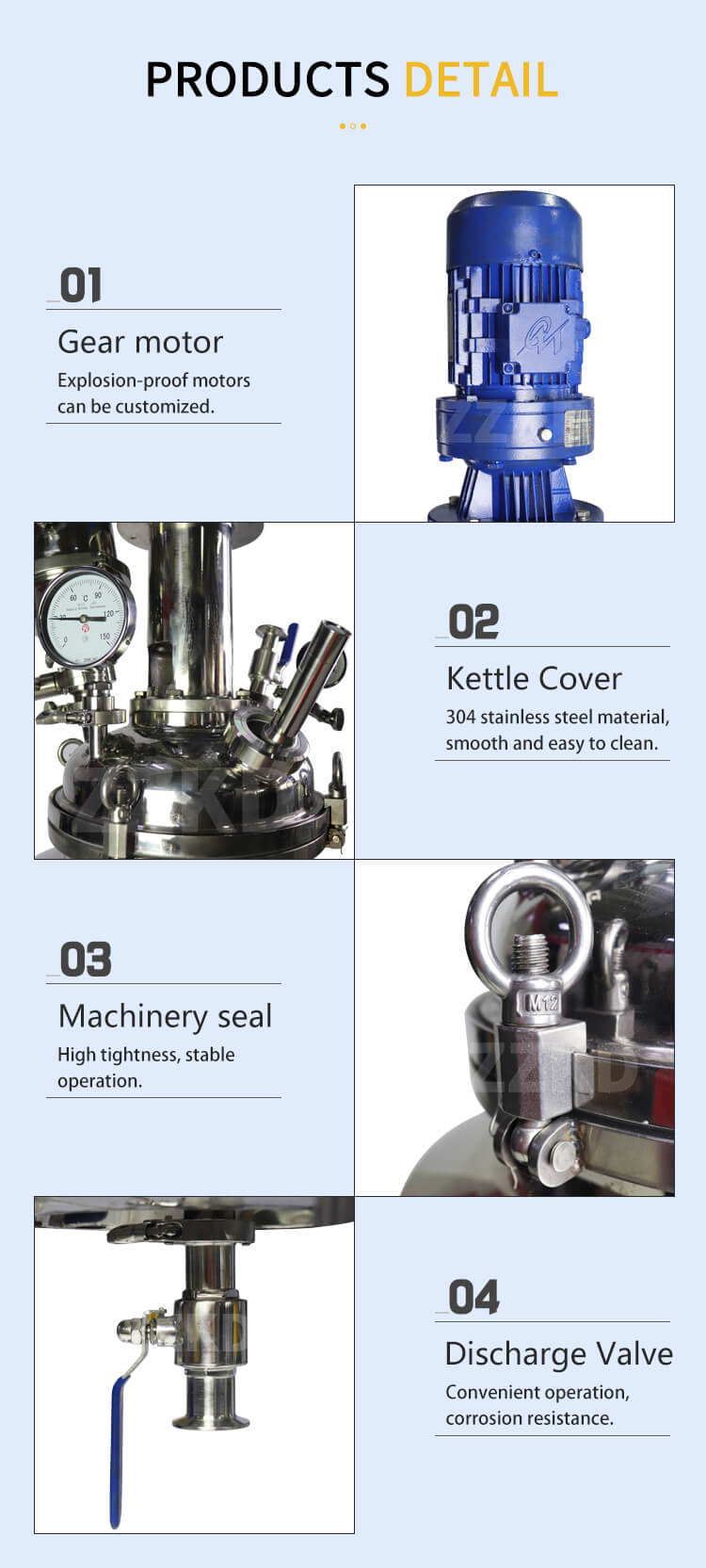
B. Design Considerations for Customized Reactors:
When customizing stainless steel reactors, manufacturers need to consider several design factors to ensure optimal performance and safety.
1. Process Compatibility: Reactor design should be compatible with the specific chemicals, reactants, and operating conditions involved in the industrial process. This includes considering the corrosion resistance, thermal stability, and mechanical strength required for handling the substances.
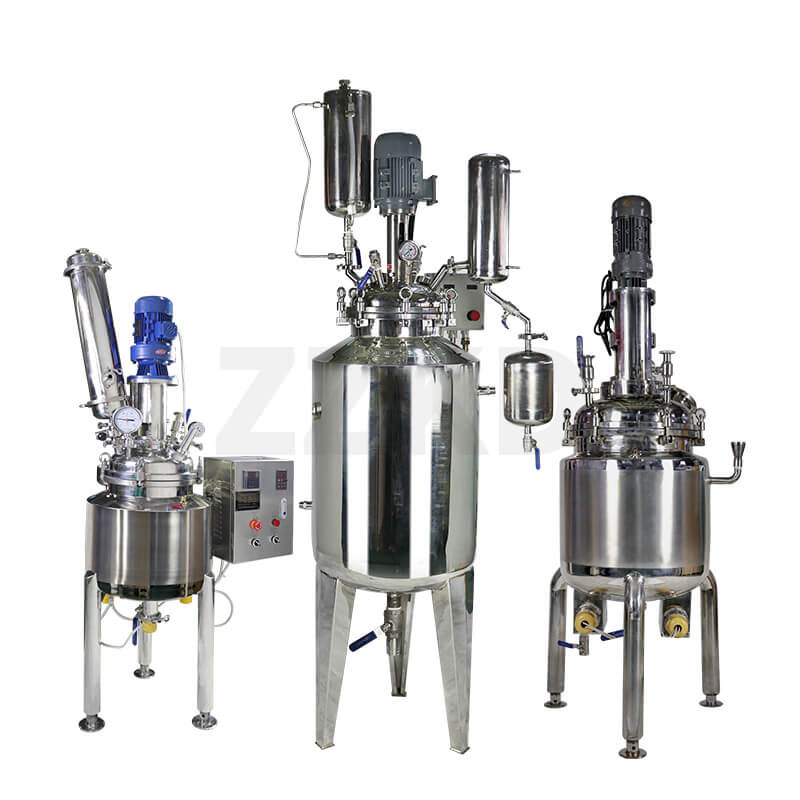
2. Safety Measures: Customized reactors should incorporate necessary safety features such as pressure relief systems, rupture discs, safety valves, and temperature monitoring devices. Compliance with safety standards and regulations is of utmost importance to protect personnel, equipment, and the environment.
3. Ease of Cleaning and Maintenance: Reactor designs should prioritize accessibility for cleaning, inspection, and maintenance purposes. Smooth surfaces, minimal dead spaces, and easy disassembly of components contribute to efficient cleaning and prevent contamination between batches.
4. Scalability: Customized reactors should be designed with scalability in mind, allowing for future expansion or process modifications. This enables industries to adapt to changing production requirements without the need for significant equipment replacements.
C. Benefits of Specialized Stainless Steel Reactors:
Specialized stainless steel reactors offer several benefits that cater to specific industry needs and enhance manufacturing processes.
1. Enhanced Efficiency: Customized reactors optimize the reaction conditions, resulting in improved process efficiency, higher yields, and reduced energy consumption. The tailored design ensures that the reactors meet the exact requirements of the industry, leading to enhanced productivity and cost-effectiveness.
2. Product Quality and Consistency: Specialized reactors enable precise control over reaction parameters, ensuring consistent product quality and reproducibility. This is especially crucial in industries such as pharmaceuticals and food processing, where stringent quality standards must be met.
3. Flexibility and Adaptability: Customized reactors provide industries with the flexibility to adapt to changing market demands, process variations, and product development. By having reactors tailored to their specific needs, industries can remain competitive and responsive to evolving trends.
4. Risk Mitigation: Specialized stainless steel reactors address industry-specific risks and challenges, such as corrosion, contamination, or thermal stresses. By considering these factors during customization, manufacturers can mitigate potential risks and ensure the safety and reliability of the reactors.
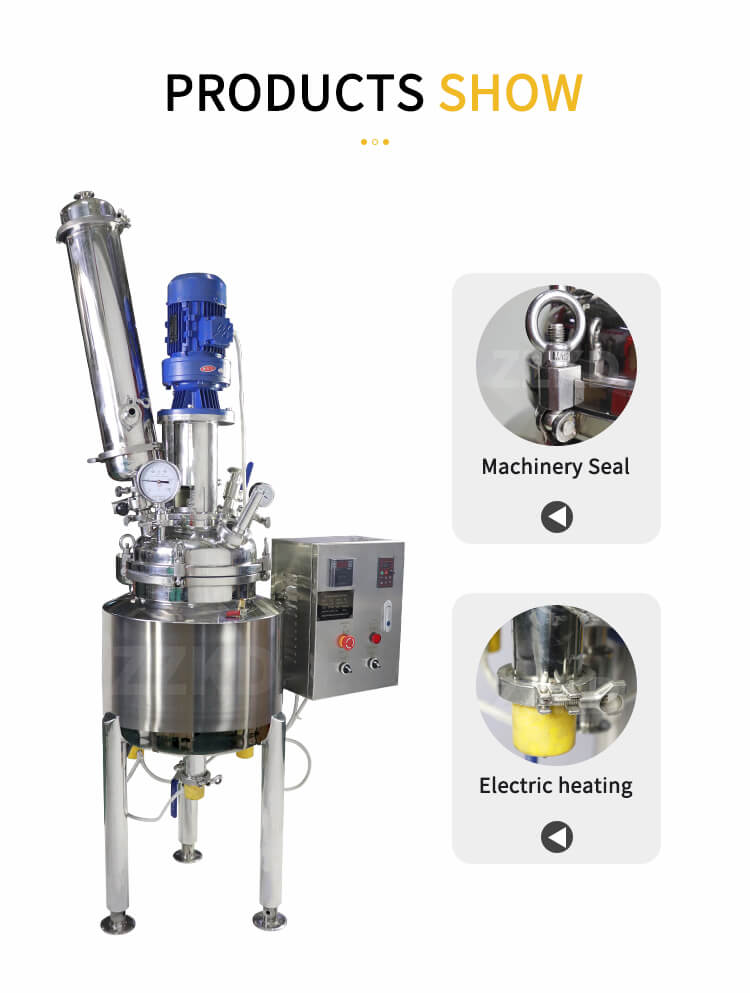
Customization and specialization offered by stainless steel reactor manufacturers play a vital role in meeting the diverse needs of industries. By tailoring reactors to specific industrial processes, manufacturers enable efficient, safe, and optimized manufacturing operations, contributing to the overall success and growth of various sectors.
IV. Quality Assurance and Compliance
A. Importance of Quality Standards:
In the manufacturing of stainless steel reactors, ensuring high-quality standards is of paramount importance. Quality assurance measures are implemented to guarantee the reliability, performance, and safety of the reactors. By adhering to rigorous quality standards, stainless steel reactor manufacturers instill confidence in their customers and demonstrate their commitment to delivering superior products.
1. Structural Integrity: Stainless steel reactors must be designed and constructed to withstand the process conditions and loads they will encounter. Rigorous quality control processes, including material testing, welding inspections, and non-destructive testing, are conducted to verify the structural integrity of the reactors.
2. Corrosion Resistance: Stainless steel’s corrosion resistance is a critical factor in reactor performance. Manufacturers employ quality control measures, such as material selection, surface treatments, and passivation, to ensure the reactors are resistant to corrosive substances and maintain their integrity over time.
3. Pressure and Temperature Ratings: Stainless steel reactors operate under varying pressure and temperature conditions. It is essential to verify that the reactors meet the specified pressure and temperature ratings through thorough testing and compliance with industry standards and codes.
B. Compliance with Industry Regulations:
Stainless steel reactor manufacturers must comply with industry-specific regulations and standards to ensure the safety and legality of their products. Some of the key regulations and standards applicable to stainless steel reactors include:
1. ASME Boiler and Pressure Vessel Code: The ASME code sets guidelines for the design, fabrication, and inspection of pressure vessels, including stainless steel reactors. Compliance with the ASME code ensures that reactors meet the necessary safety standards.
2. FDA Regulations: In industries such as pharmaceuticals and food processing, stainless steel reactors must comply with regulations set by the U.S. Food and Drug Administration (FDA). These regulations ensure that the reactors meet stringent hygiene, cleanliness, and product safety requirements.
3. International Standards: Manufacturers often adhere to international standards such as ISO 9001 (Quality Management Systems), ISO 14001 (Environmental Management Systems), and ISO 45001 (Occupational Health and Safety Management Systems). These standards provide a framework for ensuring consistent quality, environmental responsibility, and workplace safety.
C. Quality Control Processes in Stainless Steel Reactor Manufacturing:
To maintain high quality and compliance, stainless steel reactor manufacturers implement robust quality control processes throughout the manufacturing cycle. These processes involve various inspections, testing, and documentation to ensure that the reactors meet the required specifications.
1. Incoming Material Inspection: Manufacturers conduct thorough inspections of incoming stainless steel materials to verify their quality, dimensional accuracy, and compliance with specified standards. Material certificates are checked, and samples may undergo chemical analysis and mechanical testing.
2. Welding and Fabrication Inspections: Welding procedures and techniques are carefully monitored and inspected to ensure sound welds and proper fusion. Non-destructive testing methods, such as radiographic or ultrasonic testing, are employed to detect any weld defects or discontinuities.
3. Pressure and Leak Testing: Stainless steel reactors undergo pressure testing to verify their strength and integrity. Hydrostatic or pneumatic pressure tests are performed to ensure that the reactors can safely withstand the operating conditions without any leaks or failures.
4. Documentation and Traceability: Throughout the manufacturing process, manufacturers maintain detailed documentation, including material certifications, welding records, inspection reports, and test results. This documentation provides traceability and serves as evidence of compliance with quality standards.
By implementing stringent quality control processes and ensuring compliance with industry regulations, stainless steel reactor manufacturers instill confidence in their customers, guarantee the reliability of their products, and contribute to the overall safety and success of industrial processes.
In the next section, we will explore the innovations and advancements in stainless steel reactor technology, highlighting the improvements in materials, safety features, and integration of emerging technologies.
V. Advancements in Stainless Steel Reactor Technology
A. Evolution of Materials:
Stainless steel reactor technology has evolved over time, driven by advancements in material science. Manufacturers are constantly exploring new stainless steel alloys and improving existing ones to enhance the performance, durability, and corrosion resistance of reactors.
1. High-Performance Alloys: The development of high-performance stainless steel alloys, such as duplex stainless steels and super austenitic stainless steels, has expanded the range of applications for stainless steel reactors. These alloys offer superior corrosion resistance, higher strength, and improved resistance to stress corrosion cracking.
2. Specialized Coatings and Linings: In certain industries where extreme corrosive conditions are encountered, manufacturers have introduced specialized coatings and linings to enhance the corrosion resistance of stainless steel reactors. These coatings, such as glass or ceramic linings, provide an additional barrier against aggressive chemicals, prolonging the lifespan of the reactors.
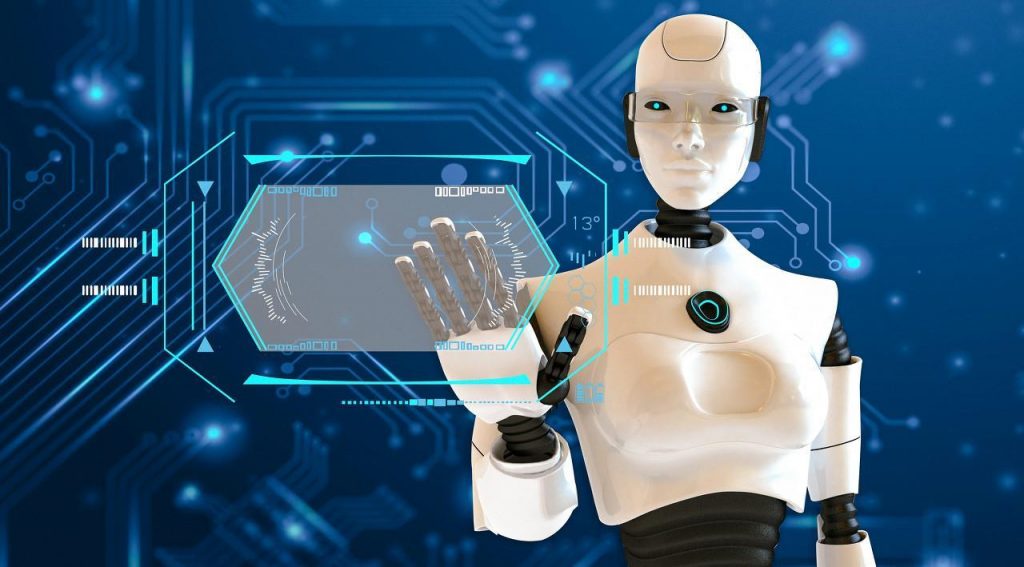
B. Enhanced Safety Features:
Safety is a top priority in stainless steel reactor design, and manufacturers are continually integrating advanced safety features to mitigate risks and ensure the protection of personnel and the environment.
1. Pressure Relief Systems: Reactors are equipped with pressure relief systems, such as safety valves and rupture discs, to prevent overpressurization. These safety devices release excess pressure in the event of a malfunction, safeguarding the integrity of the reactor and preventing catastrophic failures.
2. Instrumentation and Monitoring: Advanced instrumentation and monitoring systems are incorporated into stainless steel reactors to provide real-time data on temperature, pressure, and other process parameters. This allows for early detection of any anomalies or deviations, enabling prompt corrective actions and preventing potential accidents.
3. Automated Control Systems: The integration of automated control systems, such as programmable logic controllers (PLCs) and distributed control systems (DCS), enhances the safety and efficiency of stainless steel reactors. These systems enable precise control of process parameters, automated safety interlocks, and emergency shutdown capabilities, reducing the reliance on manual operations and minimizing human error.
C. Integration of Emerging Technologies:
Stainless steel reactor technology has embraced emerging technologies to optimize performance, energy efficiency, and process control.
1. Computational Fluid Dynamics (CFD): CFD simulations are utilized in the design phase to analyze fluid flow patterns, temperature distributions, and mixing efficiency within reactors. This computational approach helps optimize reactor design, ensuring better process performance and reducing the need for physical prototypes.
2. Process Intensification: Process intensification involves the design and integration of innovative features within stainless steel reactors to enhance productivity, reduce energy consumption, and minimize environmental impact. Examples include microreactors, reactive distillation, and continuous flow systems, which offer improved reaction kinetics, better heat transfer, and higher selectivity.
3. IoT and Industry 4.0: The integration of the Internet of Things (IoT) and Industry 4.0 concepts in stainless steel reactor technology allows for remote monitoring, data analytics, and predictive maintenance. Connected sensors and smart devices enable real-time data collection, performance optimization, and early detection of equipment failures, enhancing operational efficiency and reducing downtime.
These advancements in stainless steel reactor technology demonstrate the industry’s commitment to continuous improvement, innovation, and sustainability. By incorporating new materials, enhancing safety features, and integrating emerging technologies, manufacturers are driving the evolution of stainless steel reactors to meet the evolving needs of industries.
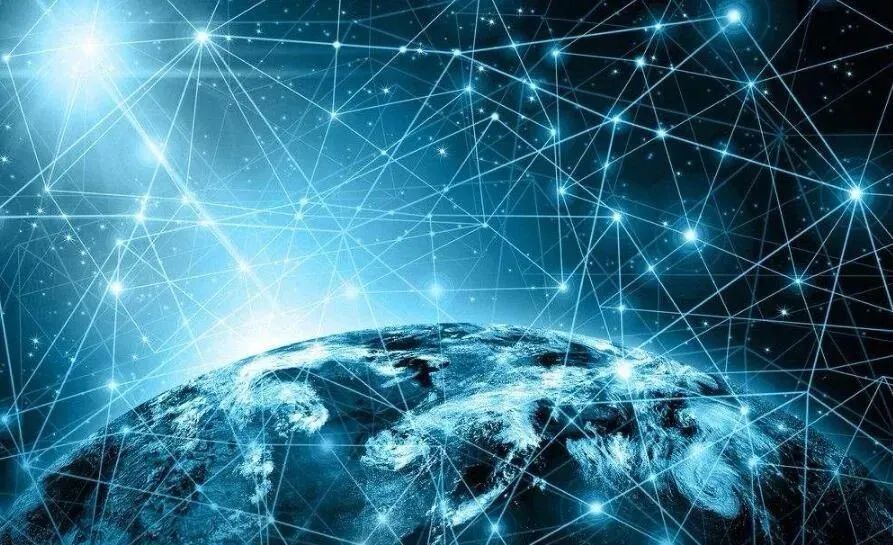
Stainless steel reactor manufacturers play a vital role in supporting a wide range of industrial processes, with their innovative designs and advanced manufacturing techniques. As demonstrated by the application case in the petrochemical industry, these reactors facilitate efficient and safe chemical reactions, resulting in enhanced productivity and product quality. With an ever-growing market demand and continuous technological advancements, stainless steel reactor manufacturers are well-positioned to meet the evolving needs of various industries. By focusing on customization, quality assurance, and sustainability, they will continue to play a crucial role in shaping the future of modern industrial processes.