In the realm of chemical engineering, the development and optimization of new processes and products often require extensive experimentation and testing. To facilitate this crucial phase, pilot plant glass reactor have emerged as indispensable tools for conducting small-scale experiments that closely mimic large-scale industrial operations. These reactors provide a controlled environment for various chemical reactions, allowing researchers to study reaction kinetics, optimize parameters, and evaluate the feasibility of scaling up processes. In this article, we delve into the intricacies of pilot plant glass reactors, their applications, and the advantages they offer in the field of industrial research and development.
I. What is a Pilot Plant Glass Reactor?
A. Definition and Design
A pilot plant glass reactor is a specialized vessel designed for conducting small-scale chemical reactions in a controlled environment. It is typically constructed with borosilicate glass, renowned for its excellent resistance to heat, chemical corrosion, and thermal shock. The glass reactor consists of a reaction vessel, a heating and cooling system, a stirring mechanism, and appropriate ports for adding reactants, monitoring parameters, and removing products. The transparent nature of the glass vessel allows researchers to visually observe the ongoing reaction, making it an invaluable tool for analysis and optimization.
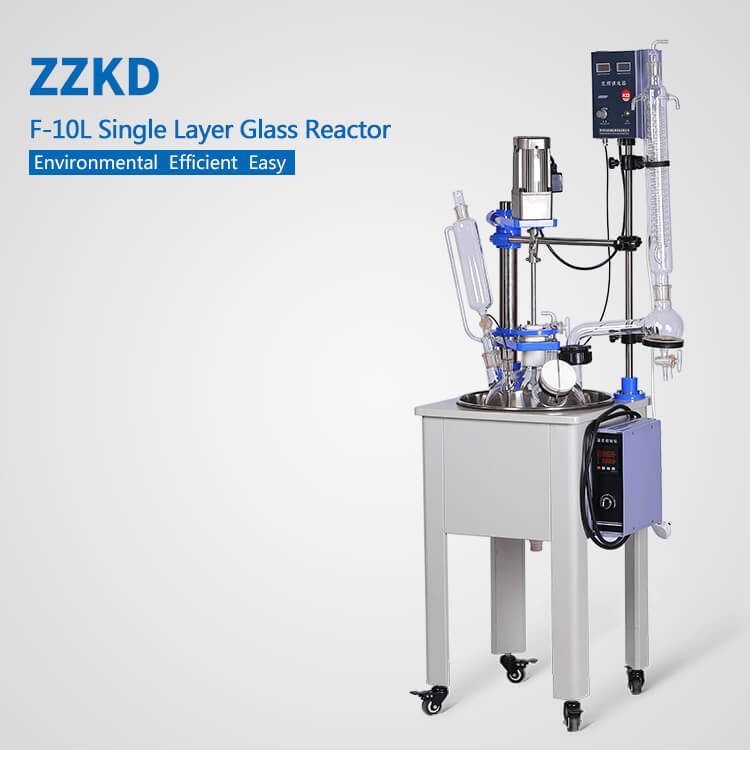
B. Key Components and Features
Pilot plant glass reactors comprise several essential components. The reaction vessel is the primary component, providing a sealed environment for the chemical reaction. It is often cylindrical in shape, equipped with a lid or flange to ensure proper sealing. The vessel’s capacity can range from a few liters to several hundred liters, depending on the desired application and experimental scale.
The heating and cooling system plays a vital role in maintaining the desired temperature range within the reactor. It consists of a heating jacket or coil and a cooling jacket surrounding the reaction vessel. The heating jacket is connected to a temperature control unit, allowing precise regulation of the reaction temperature. The cooling jacket, on the other hand, enables rapid cooling if needed.
To promote efficient mixing and stirring of the reactants, pilot plant glass reactors feature a robust stirring mechanism. This can be achieved using mechanical agitators, magnetic stirrers, or overhead stirrers, depending on the specific requirements of the reaction. The stirring mechanism ensures proper homogenization of the reaction mixture, facilitating uniform heat and mass transfer.
C. Types of Pilot Plant Glass Reactors
Different types of pilot plant glass reactors cater to various experimental needs. Some common variations include:
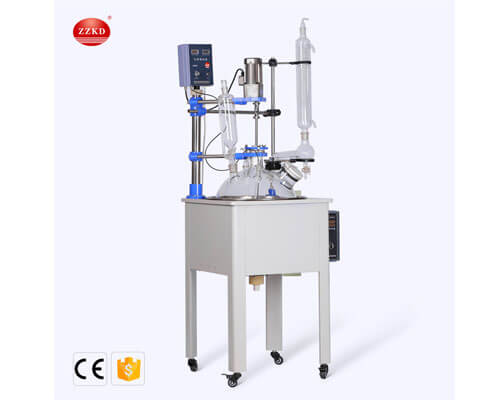
1. Single-Walled Glass Reactors: These reactors consist of a single layer of borosilicate glass and are suitable for experiments involving non-reactive processes or when corrosion resistance is not a primary concern. They are cost-effective and offer easy access to the reaction mixture for sampling and analysis.
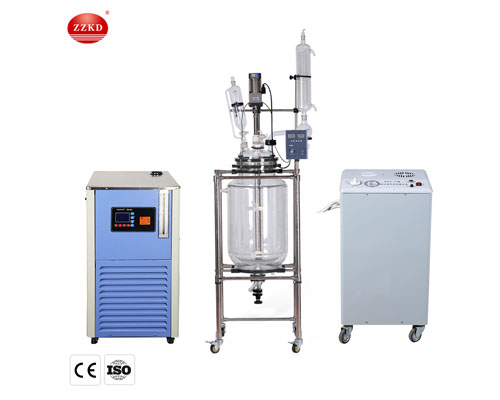
2. Double-Walled Glass Reactors: These reactors feature an additional layer of glass surrounding the reaction vessel, creating a jacket space that can be utilized for temperature control. The double-walled design enhances thermal insulation, reducing heat loss to the surroundings and providing better control over exothermic or endothermic reactions.
II. Applications of Pilot Plant Glass Reactors
Pilot plant glass reactors find applications across various industries, primarily in chemical process development, pharmaceutical and fine chemicals sectors, and the petrochemical industry. Let’s explore these applications in detail.
A. Chemical Process Development
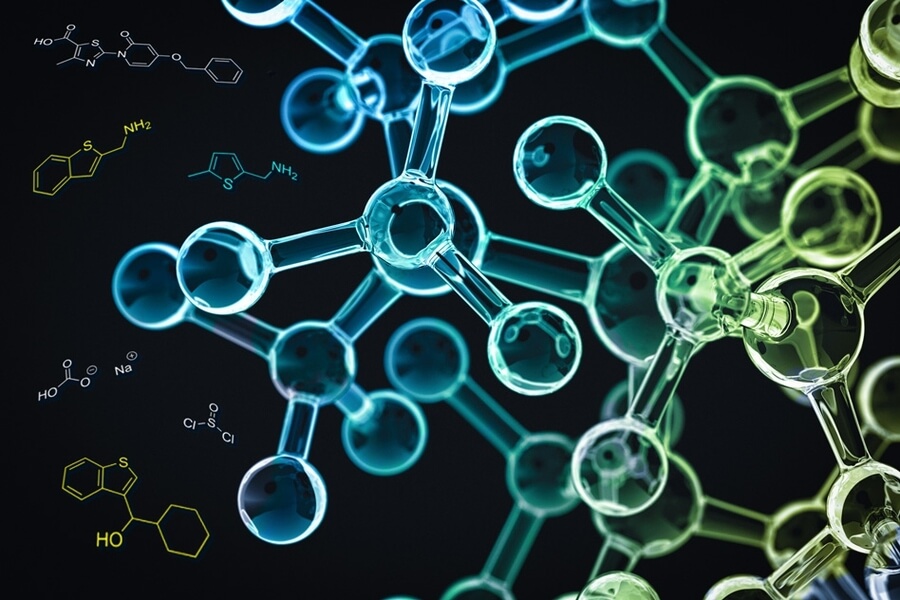
1. Reaction Kinetics Studies
In the early stages of process development, understanding the kinetics of a chemical reaction is crucial. Pilot plant glass reactors facilitate real-time observation and monitoring of reaction progress, allowing researchers to study reaction rates, intermediate formation, and overall reaction behavior. By analyzing the obtained data, scientists can derive rate equations and determine the influence of various factors such as temperature, concentration, and catalysts.
2. Parameter Optimization
To achieve optimal process conditions, parameters such as temperature, pressure, reactant concentrations, and catalyst dosage must be optimized. Pilot plant glass reactors enable researchers to evaluate different parameter combinations systematically, leading to the identification of optimal conditions that maximize reaction yield, selectivity, and efficiency. The ability to visualize the reaction aids in identifying potential issues and optimizing the process accordingly.
3. Scale-up Evaluation
Before transitioning to large-scale production, it is essential to evaluate the feasibility of scaling up a process from the laboratory to an industrial setting. Pilot plant glass reactors provide a bridge between these scales, allowing researchers to mimic industrial conditions and assess the scalability of a process. By operating at a larger scale while maintaining controlled conditions, researchers can evaluate any challenges that may arise during the scale-up process and make necessary adjustments.
B. Pharmaceutical and Fine Chemicals Industries
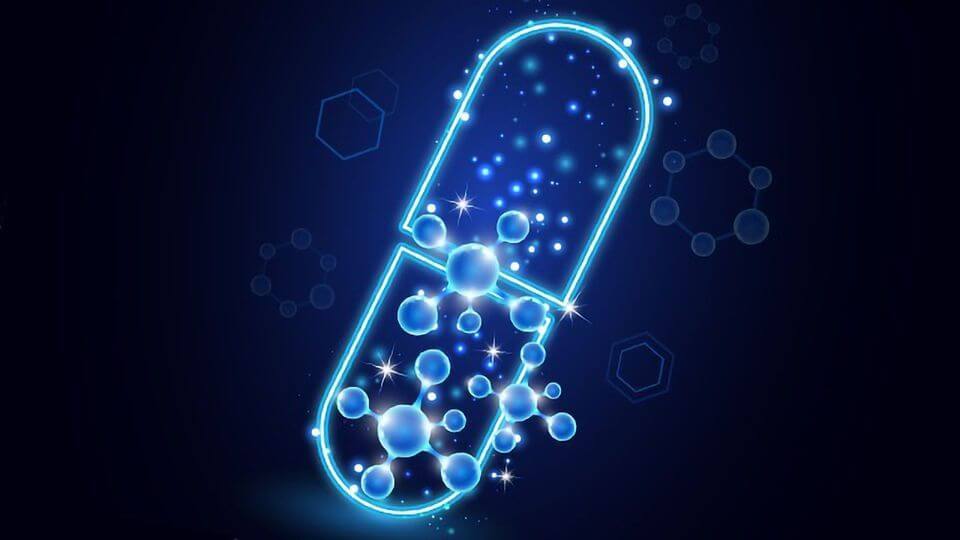
1. Medicinal Compound Synthesis
The pharmaceutical industry heavily relies on pilot plant glass reactors for the synthesis of medicinal compounds. These reactors facilitate the development and optimization of synthetic routes, enabling researchers to produce small quantities of the target compound for initial testing and analysis. By utilizing the glass reactor’s transparency, scientists can visually inspect the reaction, monitor the formation of impurities, and modify reaction conditions accordingly.
2. Drug Formulation Development
In the field of drug formulation, pilot plant glass reactors play a crucial role in optimizing various parameters such as solvents, mixing conditions, and temperature profiles. These reactors allow researchers to evaluate the impact of different formulation approaches on drug stability, bioavailability, and overall efficacy. By conducting experiments at a small scale, scientists can save significant costs associated with large-scale production while gaining valuable insights into the formulation process.
3. Catalyst Screening and Optimization
Catalysts play a vital role in many chemical processes, and pilot plant glass reactors provide a platform for catalyst screening and optimization. Researchers can test various catalysts, including heterogeneous, homogeneous, and enzyme catalysts, to identify the most effective option for a given reaction. The ability to visually observe catalyst behavior and monitor reaction kinetics enables scientists to evaluate catalyst performance and make informed decisions for industrial-scale implementation.
C. Petrochemical Industry
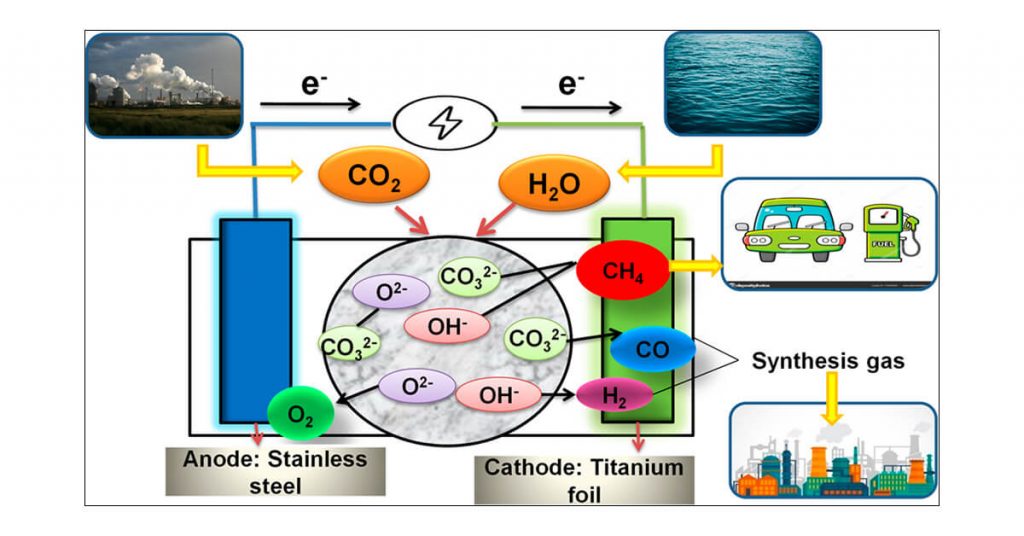
1. Catalyst Research and Development
Catalysts are widely used in the petrochemical industry to facilitate complex reactions and improve process efficiency. Pilot plant glass reactors are valuable tools for catalyst research and development, allowing scientists to investigate different catalyst compositions, structures, and preparation methods. The transparent nature of the glass reactor enables visual observation of catalyst behavior, aiding in the design of efficient catalysts for specific reactions.
2. Hydrocarbon Conversion Studies
The petrochemical industry often deals with the conversion of hydrocarbons into valuable products such as fuels, polymers, and specialty chemicals. Pilot plant glass reactors enable researchers to study hydrocarbon conversion reactions, optimize reaction conditions, and evaluate the selectivity and yield of the desired products. The reactors offer a controlled environment where temperature, pressure, and reactant ratios can be precisely regulated to mimic industrial conditions.
3. Alternative Fuel Development
With the increasing focus on renewable energy sources, pilot plant glass reactors contribute significantly to the development of alternative fuels. Researchers can explore different feedstocks, catalysts, and reaction conditions to convert biomass, waste materials, or carbon dioxide into useful fuels such as biofuels or hydrogen. These reactors provide a versatile platform for investigating the feasibility and optimization of alternative fuel production processes.
III. Application: Optimizing Ethanol Production Using a Pilot Plant Glass Reactor
To demonstrate the practical application of a pilot plant glass reactor, let’s consider a case study focused on optimizing ethanol production from lignocellulosic biomass.
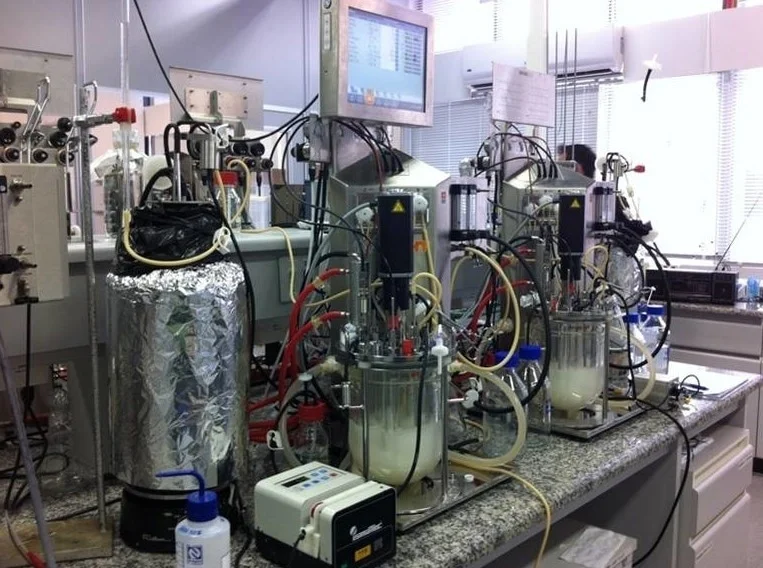
A. Background and Objectives
In this case study, the objective is to optimize the enzymatic hydrolysis and fermentation steps involved in ethanol production. The lignocellulosic biomass undergoes pretreatment, enzymatic hydrolysis, and subsequent fermentation to convert the cellulose and hemicellulose components into fermentable sugars and then to ethanol.
B. Experimental Setup
A pilot plant glass reactor with a capacity of 50 liters is employed for this study. The reactor is equipped with an efficient stirring mechanism, a temperature control system, and ports for enzyme addition, sampling, and product collection. The reactor is charged with pretreated biomass, water, and necessary enzymes for hydrolysis.
C. Process Parameter Optimization
Using the pilot plant glass reactor, various process parameters are systematically evaluated to optimize ethanol production. These parameters include temperature, enzyme dosage, reaction time, pH, and mixing intensity. By altering these parameters within the glass reactor, researchers can assess their impact on sugar conversion efficiency and ethanol yield.
D. Data Analysis and Results
Throughout the optimization process, researchers collect data on sugar concentrations, enzyme activity, and ethanol production at different parameter settings. Statistical analysis and modeling techniques are employed to identify the optimal parameter combination that maximizes ethanol yield while maintaining acceptable sugar conversion rates. The transparent nature of the glass reactor allows visual inspection of the reaction progress and identification of potential issues such as enzyme deactivation or inhibitory byproducts.
The application case study demonstrates how a pilot plant glass reactor serves as a crucial tool for optimizing ethanol production from lignocellulosic biomass. The reactor’s flexibility, precise control over process parameters, and visual monitoring capabilities enable researchers to understand the intricacies of the reaction, leading to improved process efficiency and higher ethanol yields.
IV. Advantages of Pilot Plant Glass Reactors
Pilot plant glass reactors offer numerous advantages over alternative reactor types, making them the preferred choice for many researchers and industrial professionals.
A. Enhanced Safety and Containment
The use of glass as the primary material for pilot plant reactors provides excellent chemical resistance and containment properties. Glass is highly resistant to corrosion from a wide range of chemicals, ensuring a safe environment for conducting diverse reactions. Additionally, the transparency of the glass vessel allows researchers to visually monitor the reaction without the need for frequent sampling, minimizing potential exposure risks.
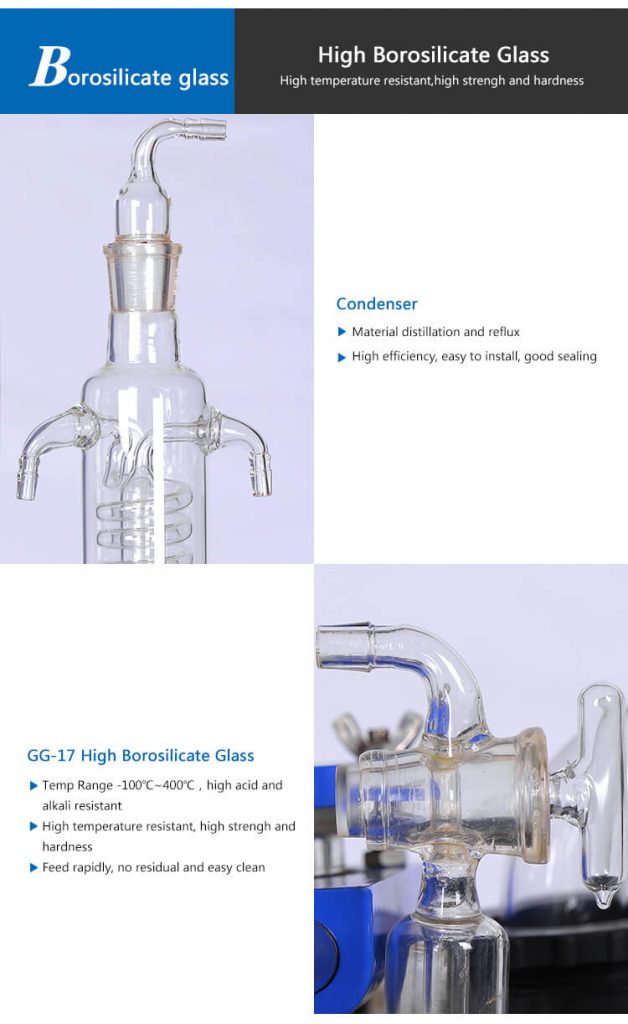
B. Visual Monitoring and Analysis
The transparency of pilot plant glass reactors allows researchers to visually observe the ongoing reaction, providing valuable insights into reaction kinetics, phase separation, and any unforeseen events. Visual monitoring simplifies data collection, facilitates troubleshooting, and aids in real-time adjustment of reaction parameters. Researchers can identify issues such as phase separation, solid deposition, or color changes, leading to prompt corrective actions.
C. Flexibility and Versatility
Pilot plant glass reactors offer significant flexibility in terms of reaction types and conditions. They can accommodate a wide range of reaction processes, including mixing, heating, cooling, and multi-phase reactions. The ability to control various parameters such as temperature, pressure, and mixing intensity allows researchers to optimize reaction conditions and explore different reaction pathways.
D. Ease of Cleaning and Maintenance
Glass reactors are relatively easy to clean and maintain, ensuring high operational efficiency. The smooth and inert surface of borosilicate glass prevents the accumulation of reaction residues, making cleaning procedures more straightforward. Additionally, glass reactors are resistant to thermal shock, allowing for rapid temperature changes during cleaning or process transitions without the risk of vessel failure.
E. Cost-Effectiveness
Pilot plant glass reactors offer a cost-effective solution for small-scale experimentation and process development. Compared to larger industrial-scale reactors, glass reactors are more affordable and require less material for conducting experiments. They also enable researchers to explore multiple reaction conditions and parameter variations before committing to expensive large-scale production equipment.
V. Choosing the Right Pilot Plant Glass Reactor
When selecting a pilot plant glass reactor, several considerations must be taken into account to ensure the suitability of the equipment for specific research or industrial applications.
A. Considerations for Reactor Size and Capacity
The choice of reactor size and capacity depends on the desired experimental scale and the volume of reactants required. Smaller reactors are suitable for laboratory-scale research, while larger reactors may be needed for scaling up processes. It is crucial to select a reactor size that can accommodate the intended reaction volume while providing sufficient space for efficient mixing and heat transfer.
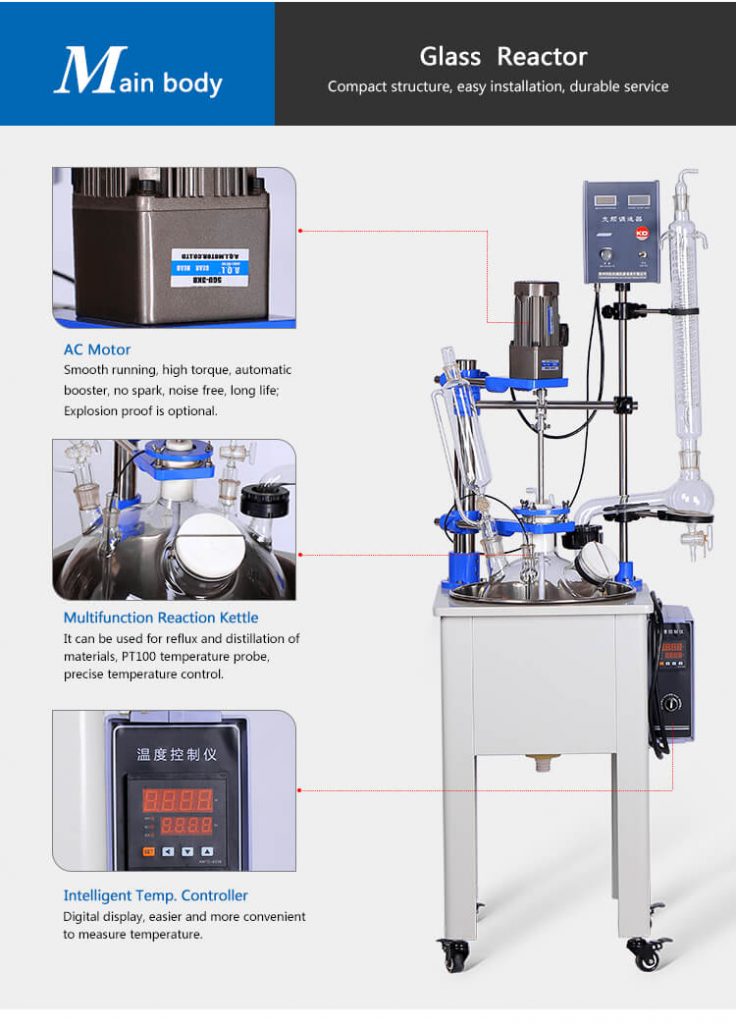
B. Temperature and Pressure Control Capabilities
The ability to precisely control temperature and pressure is vital for many reactions. The pilot plant glass reactor should have a reliable and accurate temperature control system, such as a heating jacket or coil, along with a cooling jacket for efficient heat removal. The reactor must be designed to withstand the desired pressure range without compromising safety or vessel integrity.
C. Reaction Vessel Material Selection
Although glass is the primary material for pilot plant reactors, there are variations in the quality and composition of borosilicate glass. It is essential to select a reactor that utilizes high-quality borosilicate glass, ensuring excellent resistance to chemical corrosion and thermal shock. High-quality glass reactors offer superior durability and reliability, minimizing the risk of equipment failure during experiments.
D. Ancillary Equipment and Accessories
Additional equipment and accessories can enhance the functionality and usability of pilot plant glass reactors. Examples include temperature sensors, pressure transducers, sampling ports, reflux condensers, and addition funnels. Assessing the availability and compatibility of these accessories with the chosen reactor is crucial to ensure smooth operation and data collection during experiments.
Pilot plant glass reactors have revolutionized the field of industrial research and development, providing a versatile and reliable platform for small-scale experimentation and process optimization. These reactors find applications across various industries, allowing researchers to study reaction kinetics, optimize process parameters, and evaluate the scalability of new processes. With their enhanced safety features, visual monitoring capabilities, and flexibility, pilot plant glass reactors have become indispensable tools in chemical process development, pharmaceutical and fine chemicals industries, and the petrochemical sector. By choosing the right reactor and harnessing its advantages, researchers can accelerate innovation and drive advancements in the field of industrial chemistry.