Stainless steel reactors play a pivotal role in numerous industries, where the chemical transformation of raw materials is a fundamental process. These robust vessels owe their popularity to the exceptional properties of stainless steel, offering corrosion resistance, high-temperature stability, and mechanical strength. Understanding the working principle of stainless steel reactors is crucial for optimizing their performance and ensuring safe operations.
Introducing Stainless Steel Reactors
Stainless steel reactors are specialized containers designed to handle chemical reactions under controlled conditions. They are widely used in the pharmaceutical, petrochemical, food, and chemical industries, among others. The primary advantage of stainless steel over conventional materials is its resistance to corrosion, ensuring the purity of the product and extending the life of the reactor.
The popularity of stainless steel reactor is not only due to their resistance to corrosion but also to their versatility and robustness. They can handle a wide range of chemical processes, including polymerization, oxidation, reduction, esterification, and hydrolysis reactions. Stainless steel reactors come in various configurations, including batch, continuous flow, and plug-flow reactors, suiting different production scales.
The Working Principle of Stainless Steel Reactors
The fundamental principle behind stainless steel reactor is to provide a controlled environment for chemical reactions to occur. They consist of a stainless steel vessel, agitator, heating and cooling systems, pressure and temperature sensors, and safety measures. The reactor’s design ensures efficient mixing of reactants while maintaining optimal temperature and pressure conditions.
Stainless steel reactors often have agitators or mixing systems to ensure even distribution of reactants in the vessel. Achieving high conversion rates and preventing localized hotspots is crucial to avoid undesirable side reactions or product degradation. The design of the agitator may vary depending on the type of reaction and the properties of the reactants involved.
Stainless steel reactors employ heating and cooling systems to maintain the desired temperature range during chemical reactions. This is critical because many reactions are temperature-dependent and require precise control to achieve the desired product yield and selectivity. Jacketed reactors and internal coils are common methods used to heat or cool the reactor contents efficiently.
The stainless steel reactor incorporates pressure and temperature sensors that continuously monitor the reaction conditions. These sensors offer real-time data to operators, enabling them to adjust process parameters accordingly. Furthermore, advanced automation systems can even take charge of the reactor’s operation, optimizing the reaction conditions to achieve maximum efficiency and safety.
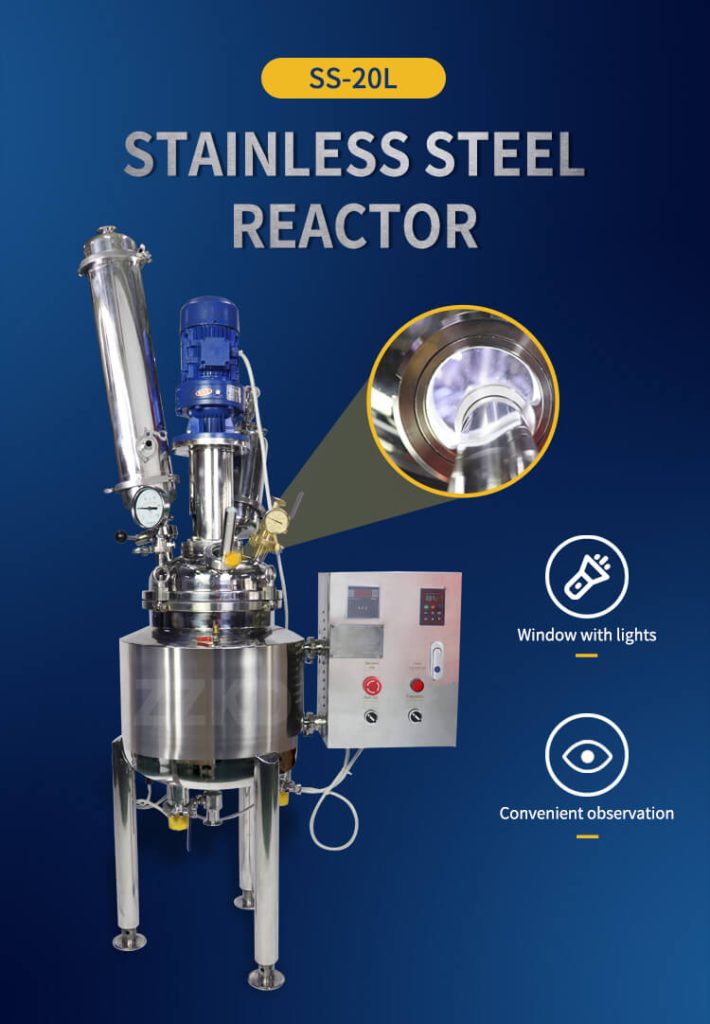
Corrosion Resistance: The Key to Stainless Steel Reactors
One of the most critical aspects of stainless steel reactor is their ability to resist corrosion effectively. Stainless steel’s high chromium content creates a protective oxide layer, shielding the metal from corrosive elements. This unique property ensures the integrity of the reactor, preventing contamination and prolonging its operational life.
Stainless steel’s corrosion resistance is boosted by additional alloying elements such as nickel, molybdenum, and titanium. These elements contribute to the formation of a stable and protective oxide layer, even in harsh chemical environments. As a result, stainless steel reactor can handle aggressive reactants, acidic or alkaline solutions, and high-temperature reactions without corroding or degrading over time.
Stainless steel’s exceptional corrosion resistance makes it ideal for processes with highly corrosive substances or extreme conditions. The petroleum industry commonly utilizes stainless steel reactors to refine crude oil and produce various petroleum products.They are also prevalent in the chemical industry, where they facilitate the synthesis of specialty chemicals and pharmaceutical intermediates.
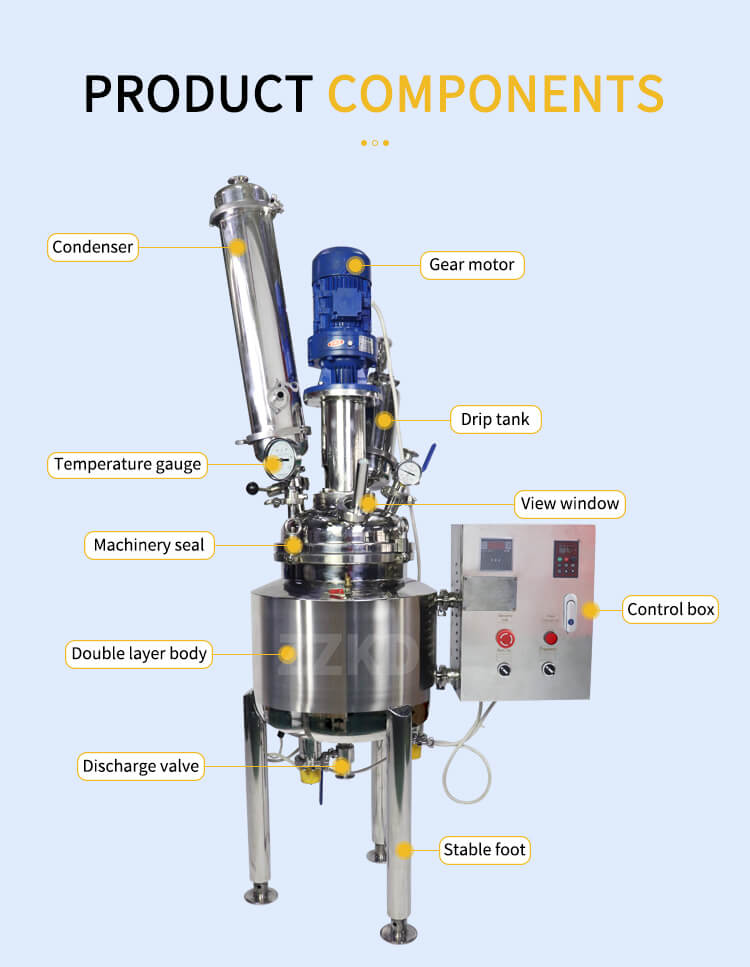
Application: Stainless Steel Reactors in the Pharmaceutical Industry
The pharmaceutical industry heavily relies on stainless steel reactor for the synthesis of various drugs and active pharmaceutical ingredients (APIs). One such example is the production of antibiotics. Stainless steel reactor provide a contamination-free environment, enabling the synthesis of pure, high-quality medicines with minimal impurities.
In the pharmaceutical industry, safety and product quality are of utmost importance. Stainless steel reactor play a crucial role in ensuring the final product’s purity, free from contamination, unwanted reactions, or side products. Additionally, the outstanding corrosion resistance of stainless steel prevents leaching of metal ions, thus safeguarding pharmaceutical product purity and safety. As a result, stainless steel reactors have become indispensable assets in pharmaceutical manufacturing, ensuring the highest standards of quality and safety in the production of life-saving medications.
The pharmaceutical industry also utilizes stainless steel reactors for large-scale production of vaccines, biological drugs, and other critical medications. The ability of stainless steel to withstand rigorous cleaning and sterilization processes is crucial in maintaining aseptic conditions during pharmaceutical manufacturing.
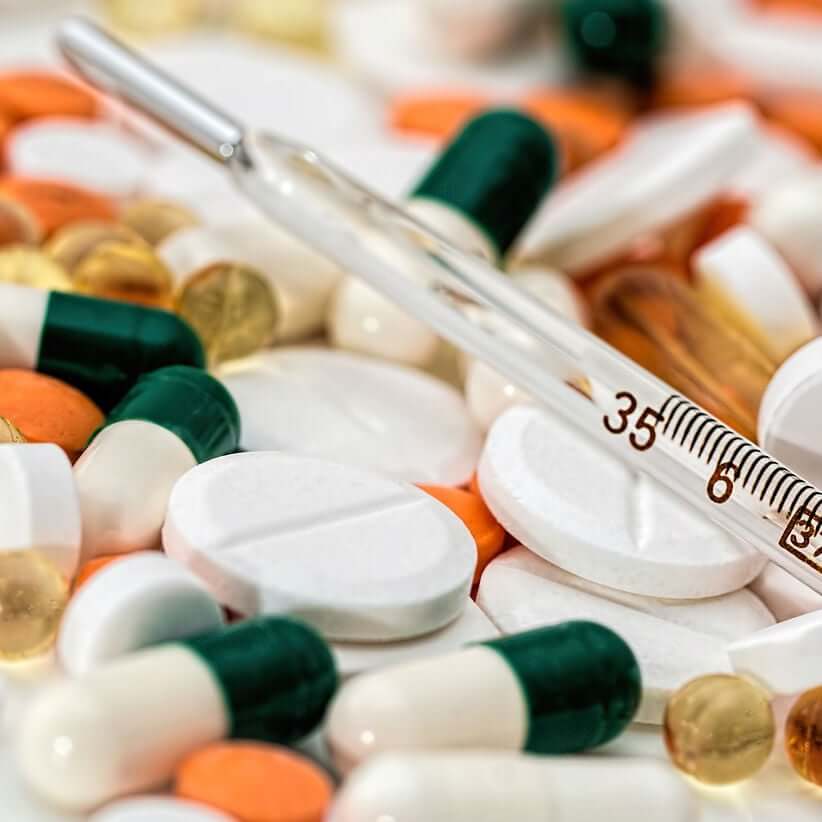
Optimal Temperature and Pressure Control
Maintaining the right temperature and pressure is critical for successful chemical reactions in stainless steel reactors. Temperature control employs a heating and cooling system to regulate exothermic and endothermic reactions at the desired rate. Moreover, precise pressure regulation ensures the safety of the reactor and prevents unwanted side reactions.
The heating and cooling systems in stainless steel reactor allow operators to control the reaction temperature within a narrow range. This is crucial for reactions with narrow temperature windows or high exothermicity, as excessive heat may cause hazardous conditions.
Stainless steel reactors achieve pressure regulation through pressure relief valves, rupture discs, and safety interlocks. These safety features are designed to prevent over-pressurization of the reactor, which could lead to catastrophic failure. Additionally, pressure control is essential for reactions involving gases or volatile substances to maintain the desired reaction rate and equilibrium.
Safety Measures and Regulations
Operating stainless steel reactor safely is of paramount importance. Reactor designs include safety measures like pressure relief valves, emergency shut-offs, and temperature monitoring to prevent accidents and safeguard everyone and the environment. Adherence to industry regulations and guidelines further ensures safe and compliant operation.
The design and construction of stainless steel reactors adhere to rigorous safety standards and codes, such as ASME (American Society of Mechanical Engineers) Boiler and Pressure Vessel Code. This ensures that the reactors can withstand the intended operating conditions without compromising safety.
Safety interlocks and automation systems in stainless steel reactors prevent hazardous situations caused by inadvertent operator actions. For instance, the reactor may have a safety interlock that prevents the agitator from operating when the reactor is not securely closed or when the temperature exceeds a predefined limit.
Proper training and standard operating procedures are essential for safe operation and maintenance of stainless steel reactor. Operators need expertise in handling hazardous chemicals, emergency response, and safety protocols relevant to the reactor’s design and application.
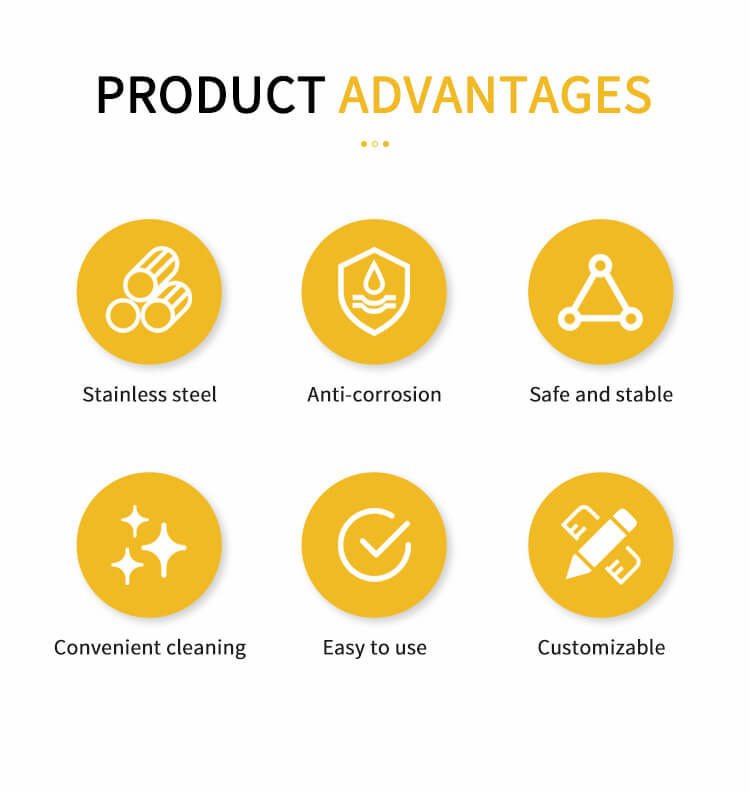
Conclusion: Pioneering the Future of Chemical Synthesis
Continuing to lead modern industrial processes, stainless steel reactors revolutionize chemical synthesis in various sectors. Rooted in corrosion resistance, optimal temperature and pressure control, and stringent safety measures, their working principle makes them indispensable tools in the quest for innovation and sustainable manufacturing practices. Moreover, their versatility and robustness position stainless steel reactors as key players in shaping a greener and more efficient future across multiple industries.
By harnessing the power of stainless steel reactor, industries can achieve higher yields, produce purer products, and minimize waste. This, in turn, drives progress towards a greener and more efficient future. Moreover, as technology advances and our understanding of materials improves, we can expect stainless steel reactor to remain a cornerstone of chemical engineering, paving the way for groundbreaking discoveries and developments in countless applications. From pharmaceuticals to petrochemicals, and from food production to specialty chemicals, stainless steel reactors will continue to shape the world of chemistry and contribute significantly to a safer and more sustainable planet.