In today’s dynamic industrial landscape, the efficient management of solvents is imperative for both economic and environmental reasons. Solvent recovery systems play a pivotal role in this process by reclaiming solvents for reuse, thereby reducing waste, cutting costs, and enhancing sustainability. However, with a myriad of options available in the market, selecting the appropriate solvent recovery system can be a daunting task. To navigate through this complexity, it is essential to consider various factors such as the type of solvents used, production volume, regulatory requirements, and budget constraints. In this comprehensive guide, we delve into the intricacies of solvent recovery systems, empowering you to make informed decisions tailored to your specific needs.
1. What is Solvent Recovery Systems?
Solvent recovery systems are designed to extract and purify solvents from process streams, enabling their reuse in industrial operations. These systems employ various techniques such as distillation, adsorption, membrane filtration, and chemical reaction to separate solvents from contaminants effectively. The choice of solvent recovery system depends on the nature of the solvents involved, their concentrations, and the desired level of purity.
2. What Types of Solvent Recovery Systems Are There?
a. Distillation Units:
Distillation remains one of the most widely used methods for solvent recovery. It involves heating the solvent mixture to its boiling point, separating it from other components based on differences in volatility, and then condensing the vapor back into a liquid. Distillation units are suitable for high-boiling solvents and large-scale operations but may require significant energy input.
b. Adsorption Systems:
Adsorption systems utilize adsorbent materials such as activated carbon or molecular sieves to capture solvents from gas or liquid streams. These systems are particularly effective for low-concentration solvent recovery and can achieve high levels of purity. However, they require periodic regeneration of the adsorbent material and may incur ongoing maintenance costs.
c. Membrane Filtration:
Membrane filtration relies on semi-permeable membranes to selectively separate solvents from process streams based on molecular size and polarity. This method is suitable for recovering volatile solvents with relatively low boiling points and offers advantages such as low energy consumption and minimal environmental impact. However, membrane fouling and limited solvent recovery rates may pose challenges in certain applications.
d. Chemical Reaction Systems:
Chemical reaction systems involve the use of chemical processes to convert solvents into non-volatile compounds or recover them in a purified form. Examples include oxidation, hydrolysis, and solvent extraction. While these systems can be highly efficient in specific scenarios, they often require additional equipment and expertise for operation and maintenance.
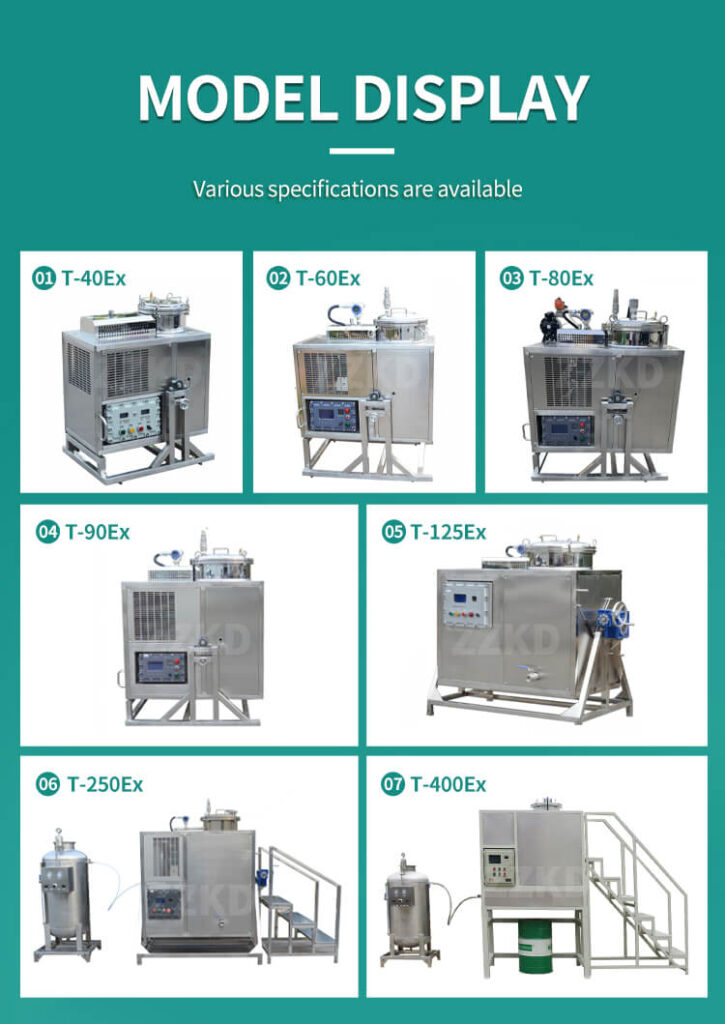
3. What Factors Should Be Considered When Selecting a Solvent Recovery System?
a. Solvent Properties:
Different solvents exhibit varying physical and chemical properties, such as boiling point, vapor pressure, and solubility. It is crucial to assess these characteristics to determine the most suitable recovery method. For instance, high-boiling solvents may require distillation, while volatile solvents may be better suited for adsorption or membrane filtration.
b. Production Volume:
The scale of solvent recovery operations has a significant impact on the choice of recovery system. Large-scale facilities with high production volumes may benefit from continuous distillation units or adsorption systems with large capacity. In contrast, small to medium-sized operations may opt for batch distillation or membrane filtration systems that offer flexibility and cost-effectiveness.
c. Regulatory Compliance:
Environmental regulations governing solvent emissions, waste disposal, and workplace safety must be carefully considered when selecting a solvent recovery system. Compliance with regulatory requirements not only avoids potential fines and penalties but also demonstrates a commitment to sustainability and corporate responsibility.
d. Cost Considerations:
The initial investment cost, operational expenses, and potential savings associated with solvent recovery systems should be thoroughly evaluated. While certain systems may have higher upfront costs, they could offer long-term benefits in terms of reduced solvent consumption, waste disposal costs, and energy efficiency. Additionally, factors such as maintenance requirements, consumables, and downtime should be taken into account when estimating the total cost of ownership.
e. Space and Infrastructure:
The available space, utilities, and infrastructure within the facility may influence the selection of solvent recovery equipment. Large-scale distillation units or adsorption systems may require dedicated areas with adequate ventilation, while compact membrane filtration units could be installed in smaller spaces or integrated into existing process lines.
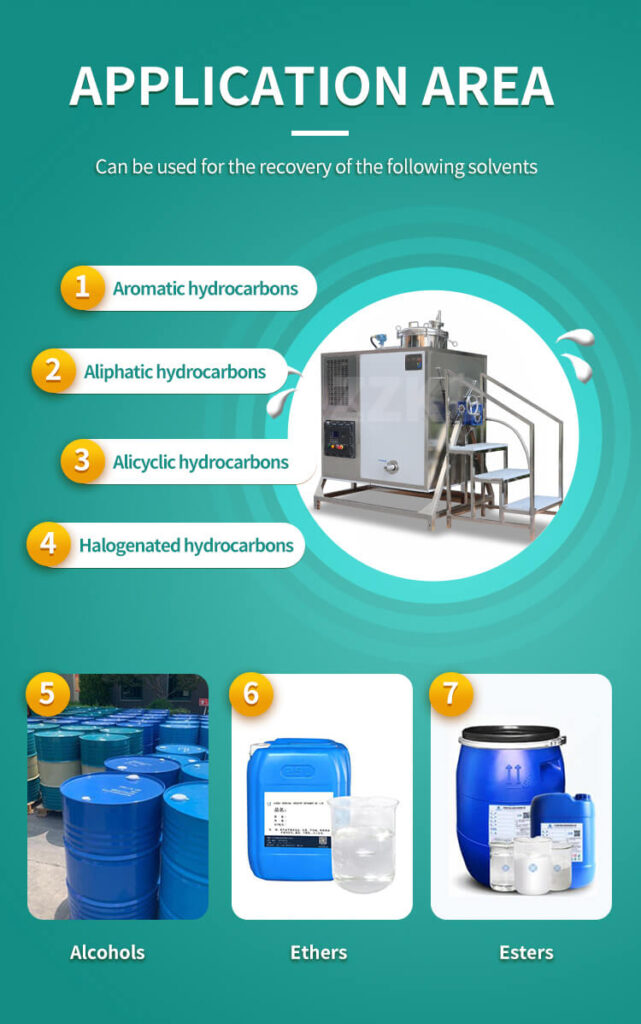
4. Is It Advantageous for Businesses to Invest in an Thinner Recycling Machine?
Absolutely, investing in an thinner recycling machine can offer significant benefits for businesses across various industries. However, the extent of these benefits may vary depending on the specific needs and objectives of the company. When considering such an investment, businesses often have diverse motivations. Some prioritize reducing costs associated with alcohol consumption in their processes, while others focus on meeting environmental regulations or improving efficiency. Similar to customers considering various factors when selecting products, such as price, quality, and reliability, businesses must also carefully evaluate different aspects to choose the most suitable thinner recycling machine for their operations.
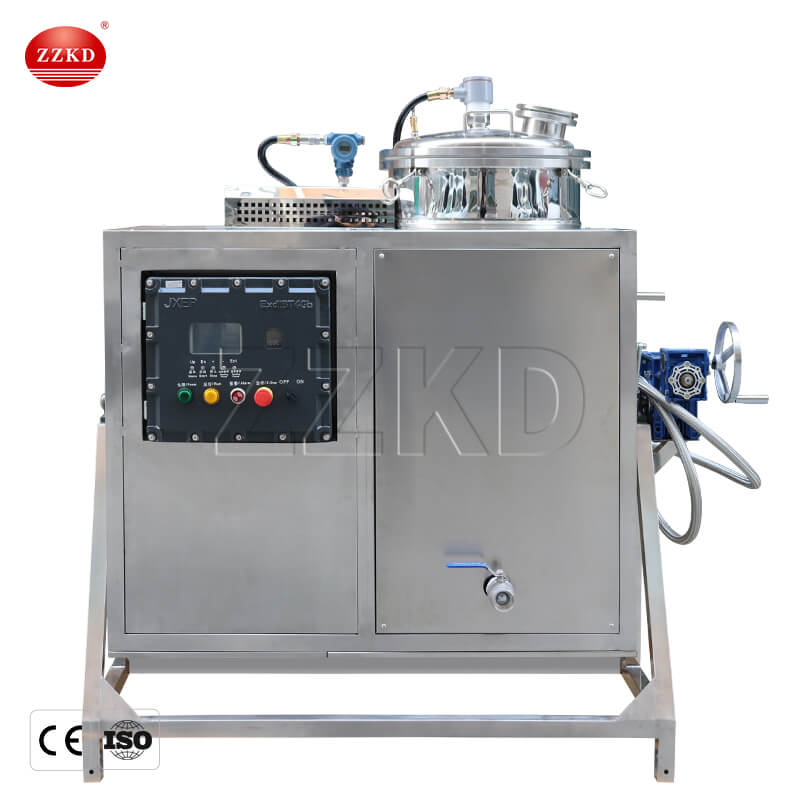
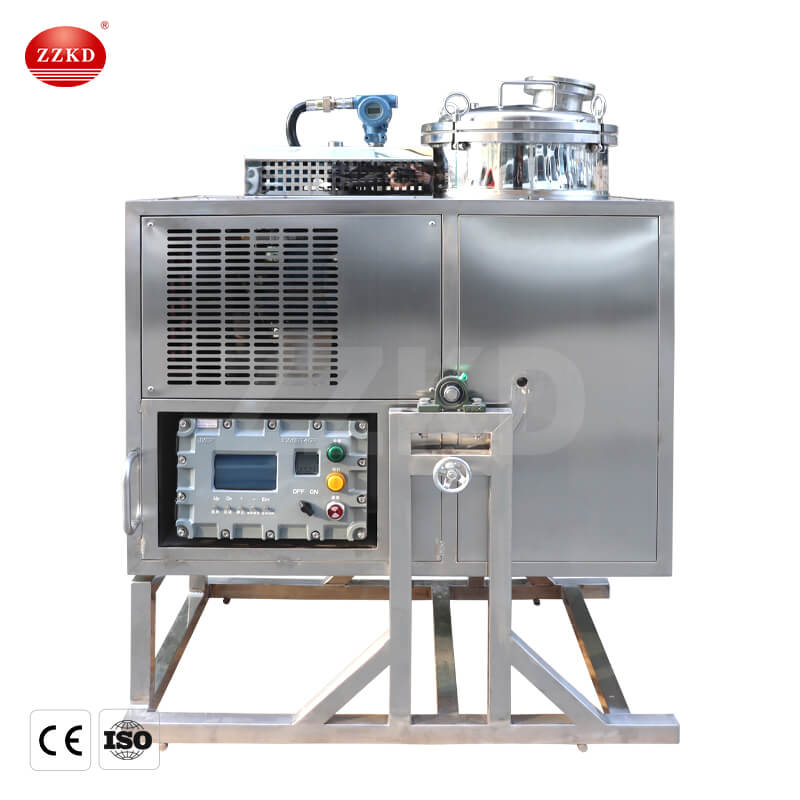
Choosing the right solvent recovery system requires a comprehensive understanding of solvent properties, production requirements, regulatory compliance, cost considerations, and infrastructure constraints. By carefully evaluating these factors and exploring the diverse range of recovery technologies available, businesses can implement sustainable and cost-effective solutions tailored to their specific needs. At the intersection of innovation and environmental responsibility, solvent recovery systems pave the way for a greener and more efficient future in industrial operations.
ZZKD is a leading provider of solvent recovery solutions, offering a wide range of innovative technologies and services to industries worldwide. With a commitment to excellence, sustainability, and customer satisfaction, we strive to deliver customized solutions that optimize solvent usage, minimize environmental impact, and maximize operational efficiency. Contact us today to learn more about our products, services, and expertise in solvent recovery.