High pressure chemical reactors are essential tools utilized in a wide range of industries, facilitating efficient compound synthesis under extreme conditions. These reactors provide a controlled environment where reactions can occur at elevated pressures, resulting in improved reaction rates and higher product yields. In this article, we will explore the concept of high pressure chemical reactors, their applications, and the benefits they offer to industrial processes.
I. Understanding High Pressure Chemical Reactors
A. Definition and Function
High pressure chemical reactors are vessels designed to handle reactions at pressures significantly higher than atmospheric pressure. They are constructed with robust materials that can withstand the extreme conditions present within the reactor. These reactors provide a controlled space for chemical reactions to take place under high pressure, allowing for the manipulation of reaction kinetics and product formation.
B. Components and Design Considerations
A high pressure chemical reactor consists of several key components, including the reactor vessel, agitators, heating/cooling systems, pressure control mechanisms, and safety features. The reactor vessel is typically made of materials such as stainless steel or high-strength alloys to ensure resistance to corrosion and pressure. Design considerations include provisions for pressure relief, temperature control, and efficient mixing to promote uniform reaction conditions.
C. Operational Safety Measures
Operating a high pressure chemical reactor requires adherence to strict safety protocols. Safety features such as pressure relief valves, rupture discs, and temperature sensors are crucial to prevent over-pressurization and ensure safe operation. Proper training, regular maintenance, and routine inspections are essential to minimize the risk of accidents and ensure the well-being of personnel working with high pressure chemical reactors.
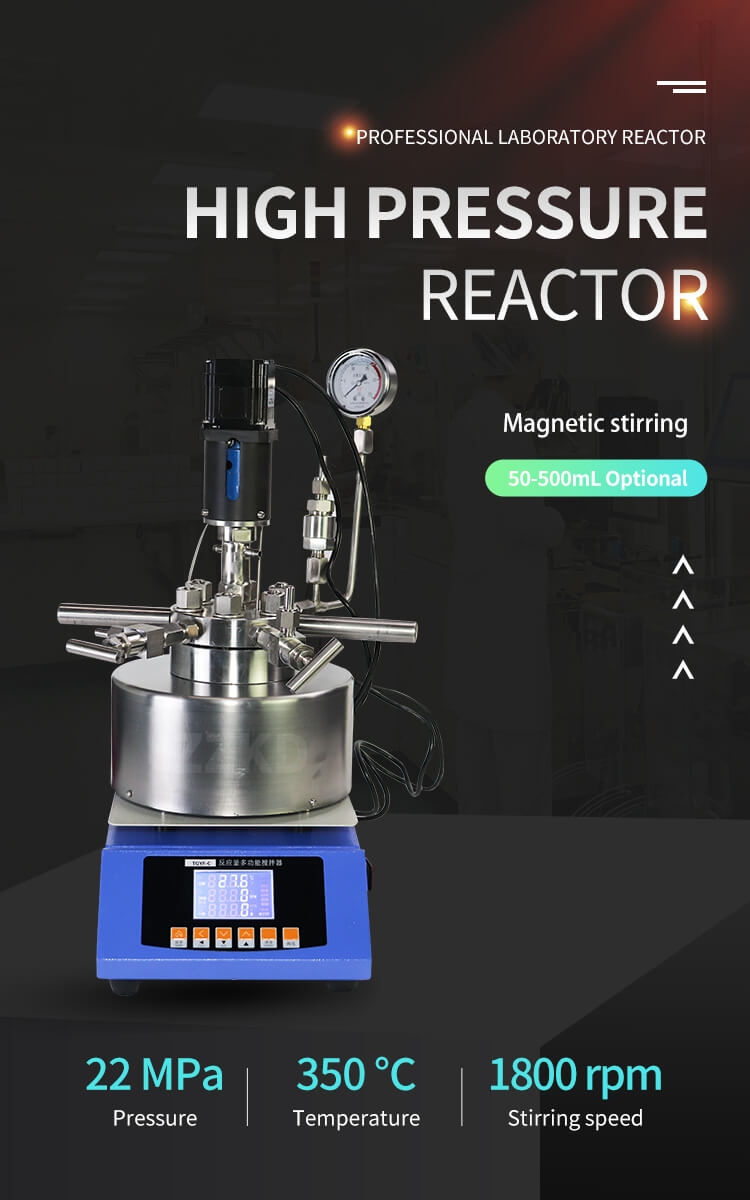
II. Applications of High Pressure Chemical Reactors
A. Petrochemical Industry: Enhancing Catalytic Processes
High pressure chemical reactors play a pivotal role in the petrochemical industry, particularly in catalytic processes. Catalytic reactions, such as hydrocracking and reforming, are often performed under high pressure conditions to optimize conversion rates and increase the yield of valuable products, such as gasoline, diesel, and petrochemical intermediates.
B. Pharmaceutical Sector: Efficient Synthesis of Active Pharmaceuticals
In the pharmaceutical sector, high pressure chemical reactors enable the synthesis of active pharmaceutical ingredients (APIs) and complex drug molecules. Reactions conducted at high pressure can enhance reaction rates, improve yield, and enable the synthesis of challenging compounds. High pressure reactors are especially valuable in the production of APIs that require specific pressure conditions for optimal quality and yield.
C. Chemical Manufacturing: Optimizing Complex Reactions
High pressure reactors find wide applications in chemical manufacturing, enabling the optimization of complex reactions. Reactions involving multi-component systems, high-viscosity materials, or unstable intermediates can benefit from high pressure conditions. High pressure chemical reactors facilitate improved reaction control, increased conversion rates, and enhanced selectivity, thereby improving overall process efficiency and product quality.
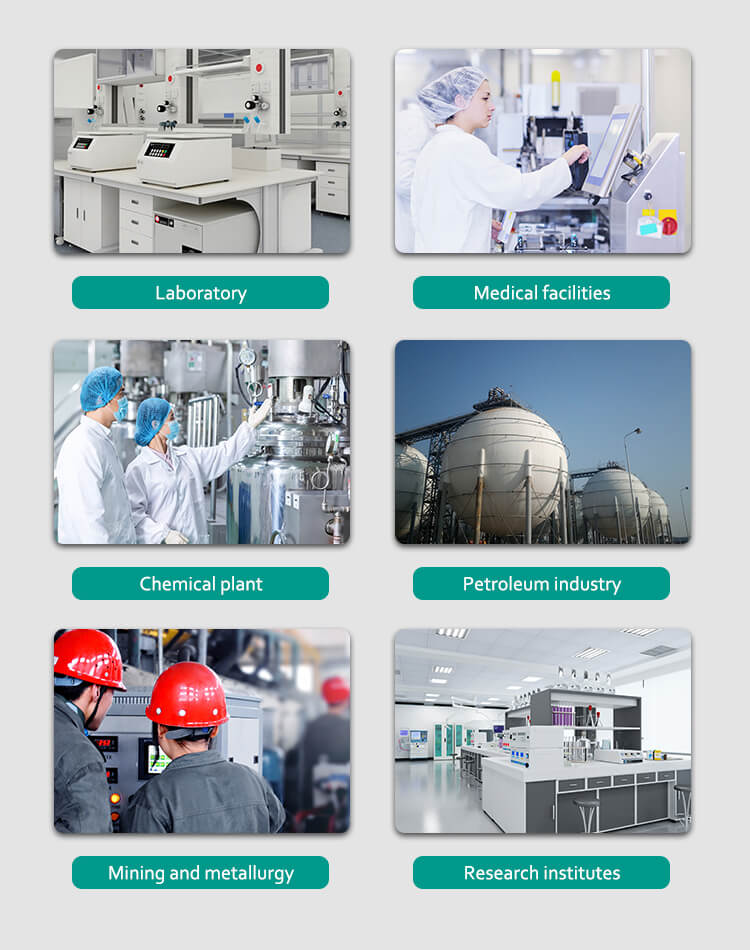
III. Case : High Pressure Reactor in Polymerization Process
A. Process Overview
One notable application of high pressure chemical reactors is in polymerization processes. Polymerization refers to the chemical reaction where small monomer units combine to form a polymer chain. High pressure reactors are commonly employed in polymerization to achieve higher molecular weights, control branching, and enhance the overall polymerization kinetics.
B. Importance of High Pressure Reaction Conditions
Polymerization reactions conducted in high pressure chemical reactors offer several advantages. The high pressure environment enables better solubility of reactants, improved mass transfer, and increased collision rates between monomer units, resulting in faster reaction kinetics. Additionally, high pressure conditions can influence the morphology and physical properties of the resulting polymers, leading to tailored materials with desired characteristics.
C. Benefits and Challenges of Polymerization at High Pressure
The utilization of high pressure chemical reactors in polymerization processes brings numerous benefits. These reactors allow for the production of polymers with higher molecular weights, improved melt flow properties, and enhanced thermal stability. Furthermore, high pressure polymerization can be advantageous for the synthesis of specialty polymers with unique properties. However, challenges such as controlling reaction exotherms, managing reactor fouling, and ensuring monomer purity must be addressed to maximize the benefits of high pressure polymerization.
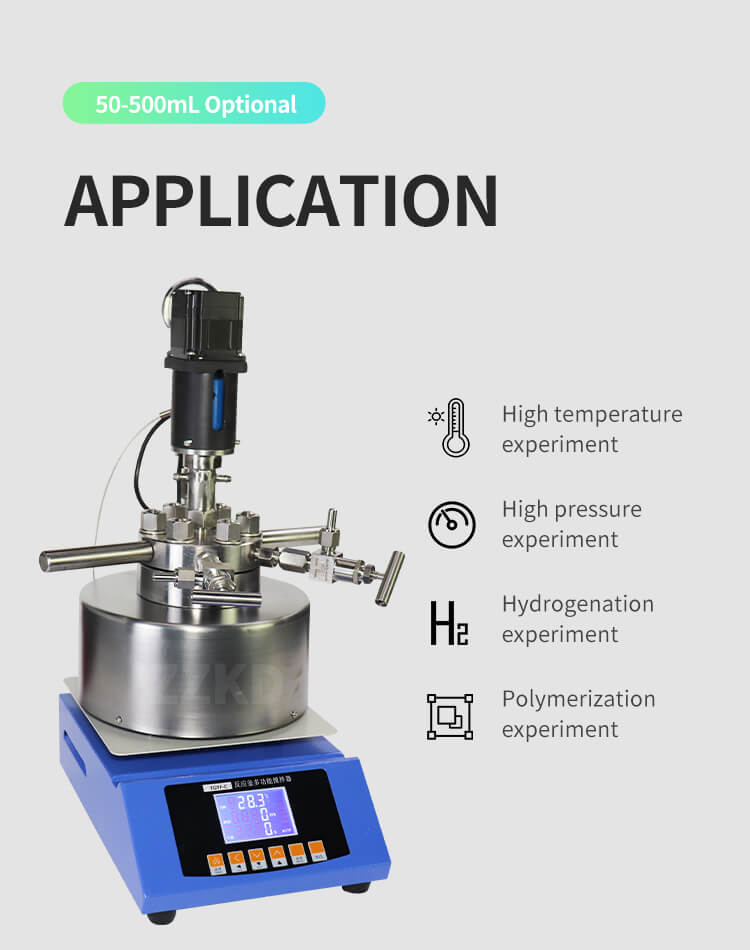
IV. Advantages of High Pressure Chemical Reactors
A. Improved Reaction Rates and Kinetics
High pressure conditions significantly enhance reaction rates by promoting faster collision rates and improving the solubility of reactants. This accelerated kinetics allows for shorter reaction times, higher throughput, and increased productivity in various industrial processes.
B. Increased Yield and Selectivity
The use of high pressure chemical reactors often leads to higher product yields and improved selectivity. The elevated pressures can drive reactions to completion, minimize the formation of unwanted by-products, and enhance the desired product’s purity, resulting in more efficient and cost-effective processes.
C. Enhanced Mass Transfer
High pressure conditions facilitate improved mass transfer by increasing the solubility and diffusivity of reactants. This leads to better intermolecular contact, faster reaction rates, and improved overall conversion, particularly in reactions involving gases or poorly soluble reactants.
D. Expanded Reaction Scope
High pressure chemical reactors offer the possibility to explore and optimize reactions that are otherwise challenging or unattainable under ambient conditions. The increased pressure can stabilize reactive intermediates, modify reaction pathways, and unlock new synthetic routes, expanding the range of chemistries that can be explored.
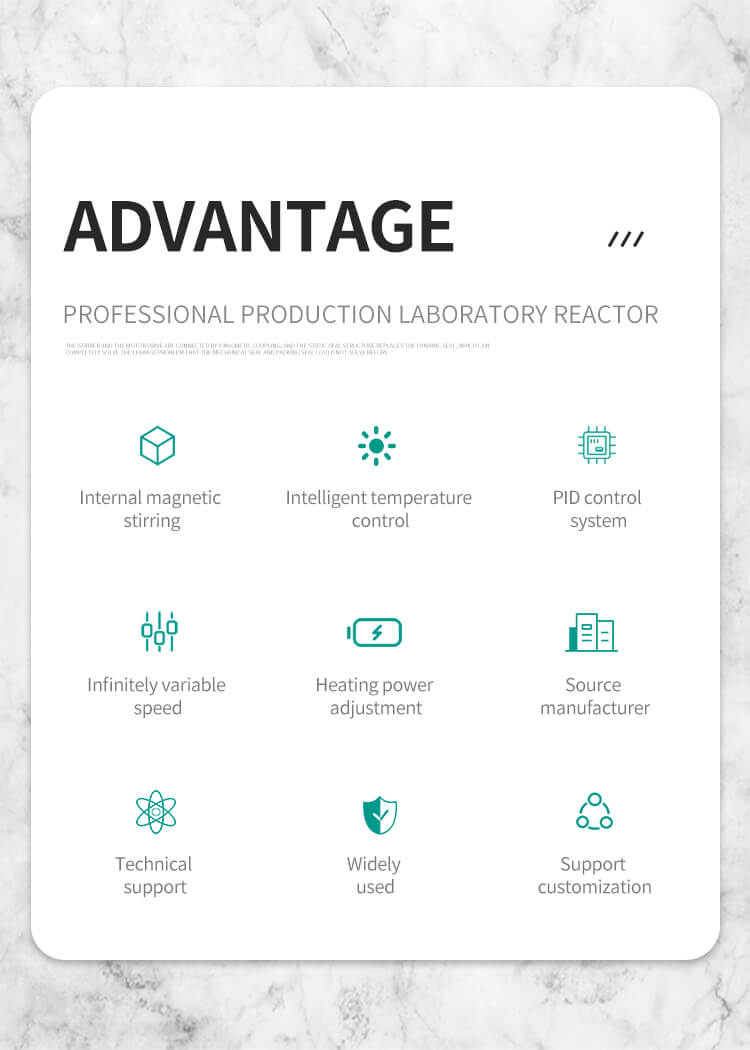
V. Design and Operation Considerations
A. Material Selection for High Pressure Reactors
The choice of materials for high pressure chemical reactors is critical to ensure their integrity and longevity. Constructors must use materials capable of withstanding high pressures, corrosive reactants, and elevated temperatures for reactor vessels. Stainless steel, high-strength alloys, and specialized polymers are commonly used for their excellent mechanical properties and resistance to chemical attack.
B. Pressure Control and Safety Features
Accurate pressure control is essential for the safe and efficient operation of high pressure reactors. Pressure relief valves, rupture discs, and pressure monitoring systems are integrated into the reactor design to prevent over-pressurization and ensure the safety of personnel and equipment. These safety features provide a reliable means to release excess pressure and protect the reactor from potential catastrophic failures.
C. Heat Transfer in High Pressure Systems
Efficient heat transfer is crucial in high pressure chemical reactors to maintain precise temperature control and prevent the accumulation of excessive heat. Cooling jackets, internal coils, or heat exchangers are commonly employed to regulate the reactor’s temperature. Proper design and selection of heat transfer mechanisms are vital to maintain optimal reaction conditions and prevent undesirable side reactions.
VI. Key Factors for Successful Implementation
A. Process Optimization and Scale-up
Successful implementation of high pressure chemical reactors requires careful process optimization and scale-up considerations. Meticulously optimizing reaction conditions, catalyst selection, and parameters like temperature, pressure, and feed rates ensures reproducibility and scalability of the desired process.
B. Effective Catalyst Management
Catalysts play a crucial role in many high pressure reactions. Proper catalyst management, including selection, preparation, and regeneration, is essential to maintain activity, selectivity, and long-term stability. Close monitoring and control of catalyst performance can significantly impact reaction efficiency and overall process economics.
C. Automation and Control Systems
Automation and control systems are integral to high pressure reactor operation. Advanced control algorithms, real-time monitoring, and data logging facilitate precise control of process variables, ensure consistent performance, and enable remote operation and diagnostics. Automation also enhances safety by implementing interlocks and alarms for abnormal conditions.
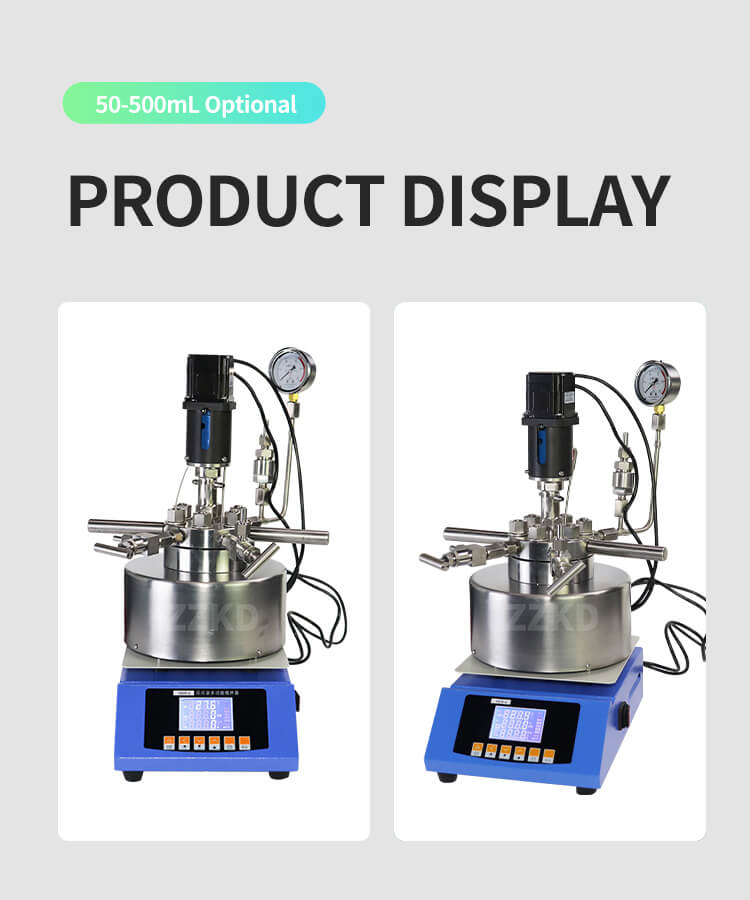
VII. Future Developments and Innovations
A. Advances in High Pressure Reactor Technology
We anticipate that continuous advancements in high pressure reactor technology will further enhance process efficiency, safety, and scalability. Innovations in materials, sealing technologies, and pressure control mechanisms will continue to push the boundaries of what can be achieved under high pressure conditions.
B. Integration of High Pressure Reactors with Continuous Flow Systems
The integration of high pressure reactors with continuous flow systems holds great promise for improving reaction control, scalability, and process safety. This combination allows for continuous production, precise residence time control, and efficient heat transfer, leading to streamlined and sustainable chemical processes.
C. Application of High Pressure Reactors in Green Chemistry
High pressure chemical reactors can contribute to the principles of green chemistry by enabling more sustainable and energy-efficient processes. By enhancing reaction rates, selectivity, and yield, these reactors can minimize waste generation, reduce energy consumption, and promote the use of environmentally friendly solvents and reagents.
High pressure chemical reactors have revolutionized complex reaction processes in industries such as petrochemicals, pharmaceuticals, and chemical manufacturing. Their ability to operate under elevated pressures and temperatures offers numerous benefits, including improved reaction rates, increased yield, enhanced selectivity, and expanded reaction scope. As technology advances, high pressure reactors will continue to play a crucial role in optimizing industrial processes and driving innovation in chemistry, leading to more efficient and sustainable production methods.