Stainless steel reactor vessels play a crucial role in various industries, including chemical processing, pharmaceuticals, food and beverage, and petrochemicals. Stainless steel reactor vessels are designed for safe and efficient handling of various chemical reactions in modern manufacturing. In this article, we will explore the features, advantages, and applications of stainless steel reactor vessels, with a particular focus on a real-world case in the pharmaceutical industry.
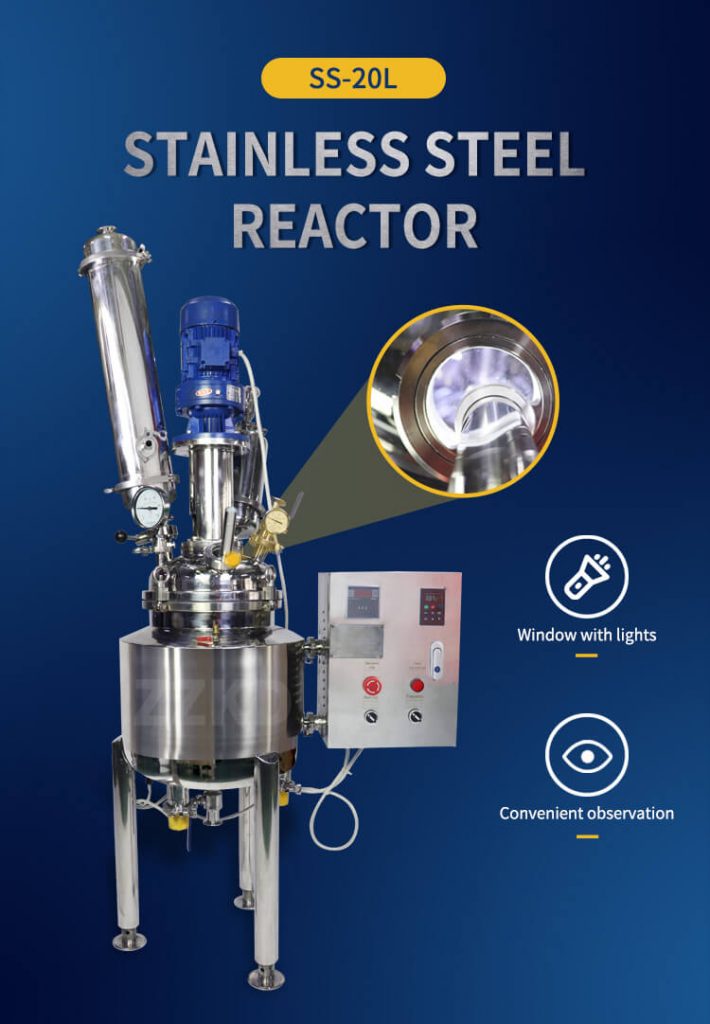
Advantages of Stainless Steel Reactor Vessels
Stainless steel reactor vessels offer numerous advantages over other materials commonly used in chemical processing equipment. One of the key benefits is their exceptional corrosion resistance. Stainless steel, particularly grades like 316 and 316L, exhibits excellent resistance to a wide range of chemicals, acids, and alkalis, ensuring the vessel’s longevity and preventing contamination of the process fluids. This resistance is vital in maintaining the purity and quality of the end products.
Another advantage is the high strength-to-weight ratio of stainless steel. This property allows for the design of reactor vessels with thinner walls while maintaining structural integrity. The lightweight nature of stainless steel vessels simplifies installation, reduces transportation costs, and provides ease of operation during maintenance activities.
Furthermore, stainless steel reactor vessel are highly durable, ensuring a long service life even under harsh operating conditions. They can withstand extreme temperatures and pressures, making them suitable for a wide range of chemical reactions. Stainless steel’s mechanical properties, like impact resistance and fatigue strength, enhance vessel reliability and safety significantly.
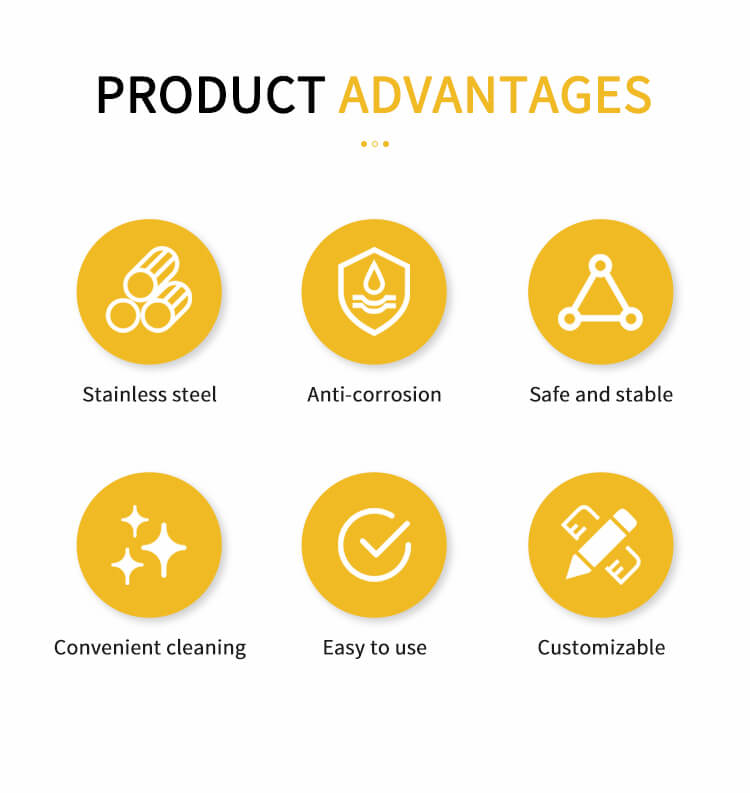
Application: Stainless Steel Reactor Vessel in the Pharmaceutical Industry
In the pharmaceutical industry, stainless steel reactor vessels are widely used in the production of medicines, pharmaceutical intermediates, and active pharmaceutical ingredients (APIs). These vessels play a critical role in various stages of drug manufacturing, including synthesis, crystallization, purification, and formulation.
For instance, during the synthesis of APIs, stainless steel reactor vessels provide an ideal environment for chemical reactions. Their inert nature prevents unwanted reactions between the process fluid and the vessel walls, ensuring the purity and efficacy of the final product. Additionally, the smooth surface finish of stainless steel vessels allows for easy cleaning and sterilization, a crucial requirement in pharmaceutical manufacturing.
In the case of crystallization, stainless steel reactor vessel provide a controlled environment for the formation of high-quality crystals. The vessels can be equipped with internal agitators or other mixing mechanisms to promote uniform heat distribution and mass transfer, leading to superior crystal growth.
Moreover, stainless steel reactor vessels facilitate the purification of pharmaceutical compounds through processes like distillation, evaporation, and filtration. These vessels can withstand the high temperatures and vacuum conditions often required during purification steps. The excellent thermal conductivity of stainless steel allows for efficient heat transfer, ensuring optimal separation and purification of the desired compounds.
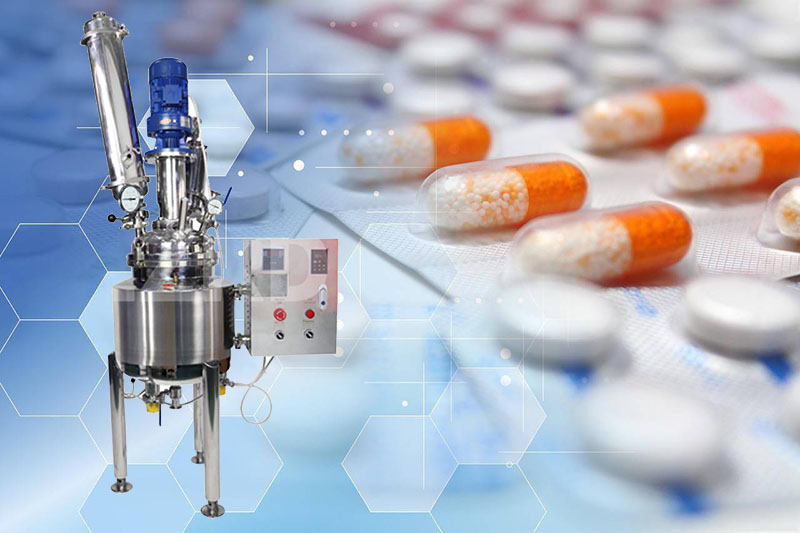
Key Considerations for Selecting a Stainless Steel Reactor Vessel
When selecting a stainless steel reactor vessel for a specific application, several factors should be taken into consideration. First and foremost, it is essential to assess the compatibility of the vessel material with the process fluids, including any potential corrosive agents or reactive substances. Stainless steel offers a wide range of grades, each with its own resistance properties, so choosing the appropriate grade is crucial.
The operating conditions, such as temperature, pressure, and agitation requirements, must also be considered. These factors will influence the vessel’s design, wall thickness, and reinforcement requirements. It is important to consult with experienced engineers or manufacturers to ensure the vessel’s specifications meet the process demands.
Another vital consideration is the vessel’s size and capacity. Factors such as the batch size, production volume, and space limitations must be evaluated to determine the optimal vessel dimensions. Additionally, the vessel should be designed with appropriate ports and connections to allow for efficient material transfer, sampling, and monitoring.
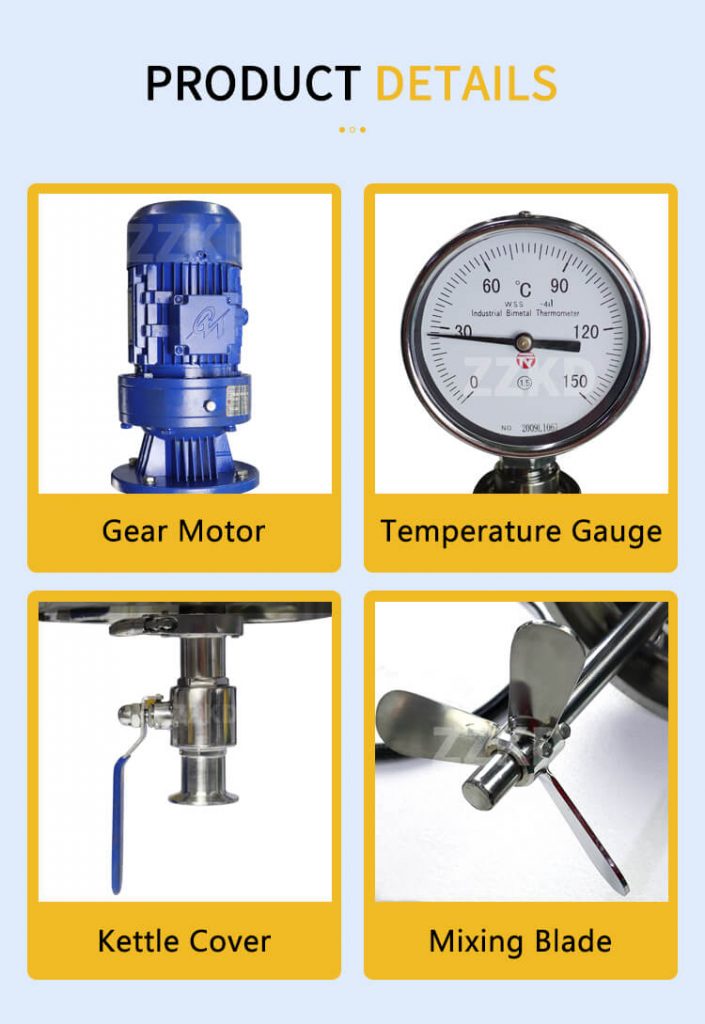
Maintenance and Care of Stainless Steel Reactor Vessels
To maximize the lifespan and performance of stainless steel reactor vessels, proper maintenance and care are essential. Regular inspections should be conducted to identify any signs of corrosion, mechanical damage, or leaks. Prompt repair or replacement of damaged components can prevent process disruptions and ensure safety.
Cleaning procedures should be followed diligently to eliminate any residues or contaminants that may accumulate during the manufacturing process. The use of appropriate cleaning agents and techniques, such as CIP (clean-in-place) systems, is crucial to maintain the vessel’s hygienic conditions.
Additionally, routine checks and calibration of instrumentation and safety devices should be performed to guarantee accurate measurement and reliable operation. The vessel’s agitator, heating/cooling system, and other auxiliary equipment should also be inspected regularly to ensure their proper functioning.
Stainless steel reactor vessels have become an integral part of chemical processing industries, offering exceptional corrosion resistance, durability, and versatility. Their application in the pharmaceutical industry, as demonstrated in the case discussed above, highlights their crucial role in ensuring the production of high-quality medicines and APIs.
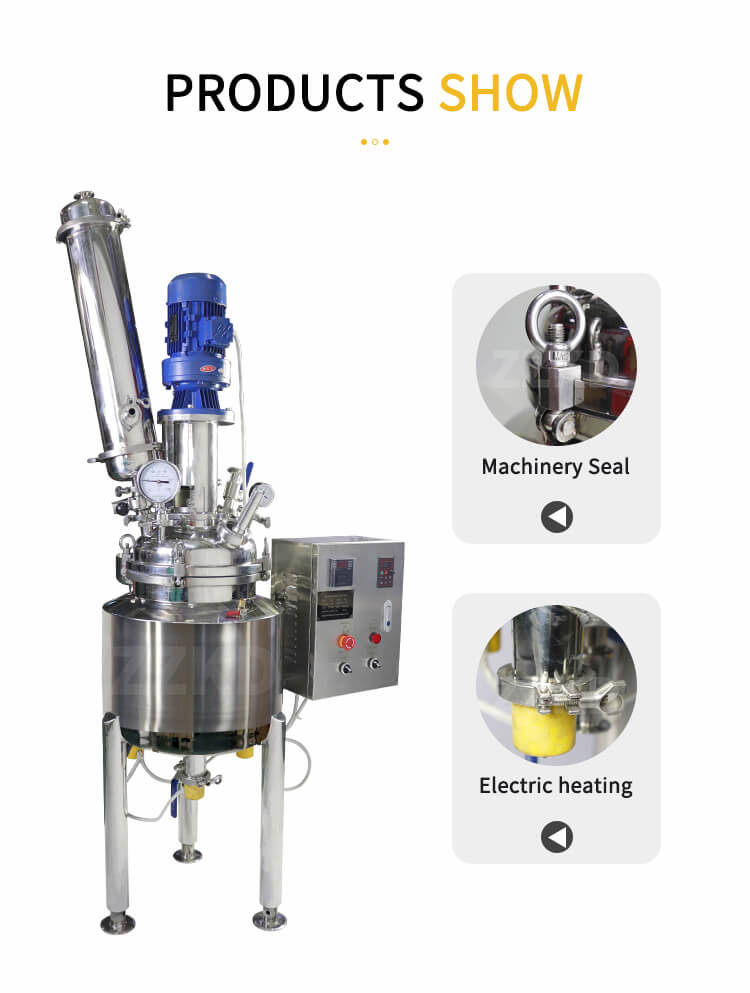
When selecting a stainless steel reactor vessel, careful consideration of material compatibility, operating conditions, and design parameters is essential. Regular maintenance and cleaning are vital to prolong the vessel’s lifespan and maintain optimal performance.
With their outstanding properties and broad range of applications, stainless steel reactor vessels continue to play a vital role in advancing chemical processes and enabling the production of essential products across various industries.