Borosilicate glass reactors have become an indispensable tool in the field of chemical process control, offering exceptional resistance to thermal stress and chemical corrosion. These reactors are widely used in laboratories, pilot plants, and industrial settings for various applications such as chemical synthesis, pharmaceutical manufacturing, and the petrochemical industry. This article aims to delve into the advantages of borosilicate glass reactors, explore their applications, present a case study, and highlight important safety measures.
Advantages of Borosilicate Glass Reactors
Borosilicate glass, composed primarily of silica and boron oxide, possesses remarkable properties that make it ideal for reactor construction. One of the key advantages is its exceptional resistance to thermal stress. Borosilicate glass can withstand rapid temperature changes without cracking or shattering, allowing for precise control of reaction conditions. This unique property ensures the safe handling of highly exothermic reactions and reduces the risk of equipment failure.
Another advantage is the outstanding chemical resistance of borosilicate glass. It is highly inert and resistant to a wide range of corrosive substances, including acids, bases, and organic solvents. This characteristic makes borosilicate glass reactors suitable for various chemical processes, ensuring the purity and integrity of the reactions.
Furthermore, borosilicate glass reactors offer excellent transparency, allowing operators to visually monitor the progress of reactions without disturbing the system. This feature enables real-time observation and adjustment, enhancing process control and facilitating troubleshooting if necessary.
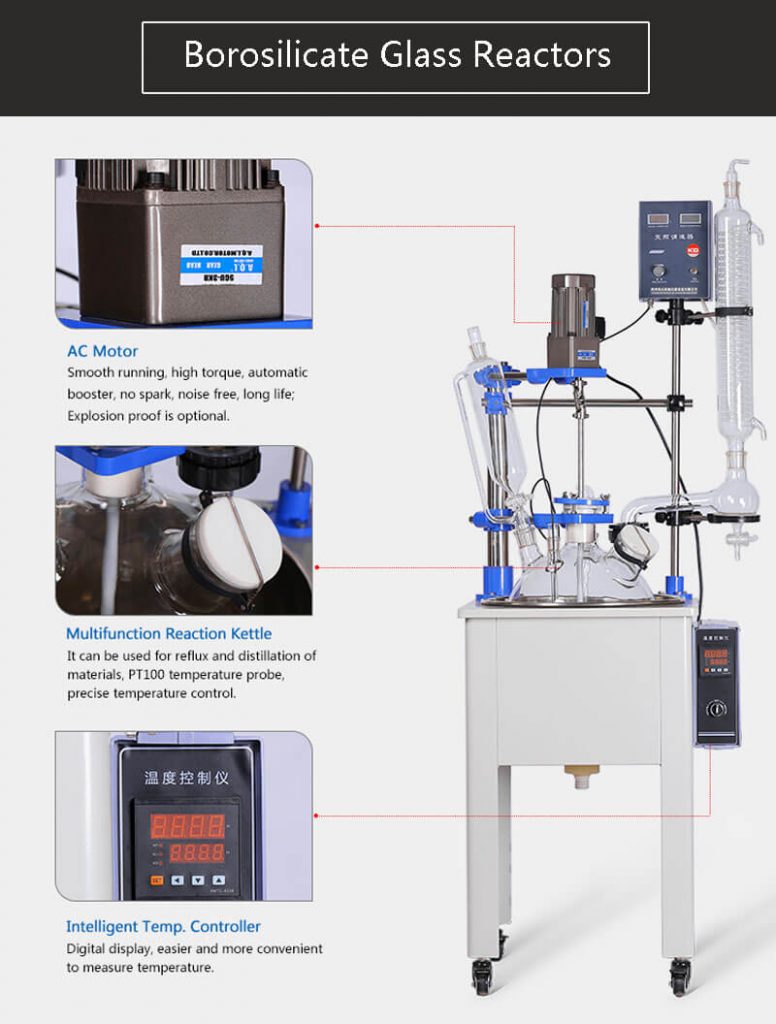
Applications of Borosilicate Glass Reactors
Laboratory Scale Chemical Synthesis
In laboratory settings, borosilicate glass reactors are widely used for chemical synthesis. Researchers can conduct a range of reactions, such as organic synthesis, polymerization, and catalytic processes, with precise control over temperature, pressure, and reaction time. The transparency of the glass allows for easy monitoring of color changes, phase separations, and the formation of precipitates, enabling scientists to optimize reaction conditions and yield high-quality products.
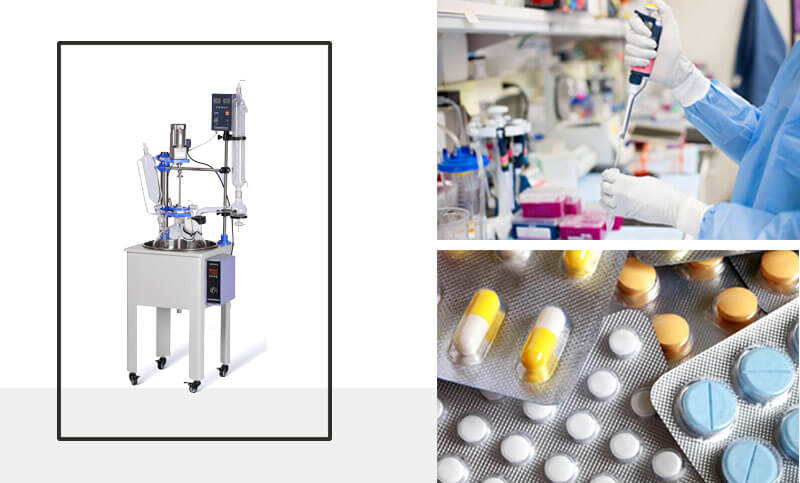
Pharmaceutical Manufacturing
The pharmaceutical industry relies on borosilicate glass reactors for the production of drugs and pharmaceutical intermediates. These reactors facilitate the synthesis of complex molecules, such as active pharmaceutical ingredients (APIs) and specialty chemicals, while maintaining the necessary purity and quality standards. The excellent resistance of borosilicate glass to aggressive chemicals ensures the integrity of the reaction, preventing contamination and preserving the final product’s efficacy.
Petrochemical Industry
In the petrochemical industry, borosilicate glass reactors play a vital role in various processes, including catalyst development, polymerization, and the production of specialty chemicals. The reactors’ resistance to high temperatures and corrosive substances is crucial for handling aggressive reactants and maintaining reaction control. Borosilicate glass reactors also find application in pilot plants, allowing engineers to scale up processes while minimizing the risk of reactor failure.
Case: Borosilicate Glass Reactor in the Production of Specialty Chemicals
To illustrate the effectiveness of borosilicate glass reactors, let’s consider a case study in the production of specialty chemicals. A chemical manufacturing company aimed to synthesize a new compound with potential applications in the electronics industry. The researchers controlled reaction parameters and visually monitored progress precisely using a borosilicate glass reactor.
The transparent reactor allowed them to observe the color change and formation of the desired compound in real-time. The resistance to corrosive chemicals ensured that the reactants did not interact with the glass, avoiding contamination and maintaining the purity of the product. The excellent thermal shock resistance of the glass reactor allowed for rapid cooling and handling of the highly exothermic reaction.
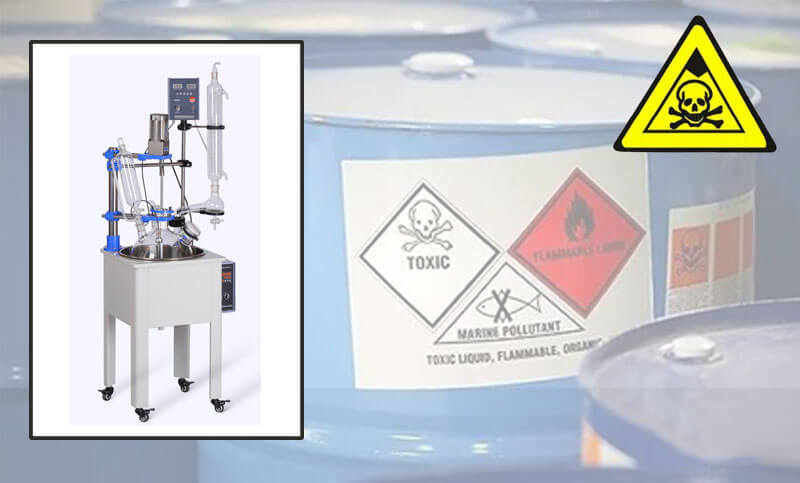
Safety Measures for Working with Borosilicate Glass Reactors
While borosilicate glass reactors offer numerous advantages, it is essential to prioritize safety when working with these systems. Some key safety measures include:
1. Appropriate protective gear: Wear protective gloves, goggles, and lab coats to safeguard against chemical splashes and potential glass breakage.
2. Proper handling: Use caution when assembling and disassembling the glass reactor to avoid accidental damage. Avoid sudden temperature changes and rapid cooling to prevent thermal stress.
3. Regular inspections: Conduct regular inspections of the glass reactor to identify any signs of wear, stress, or damage. Replace any damaged components promptly.
4. Training and knowledge: Ensure operators receive proper training in working with borosilicate glass reactors. Familiarize them with safety protocols and emergency procedures.
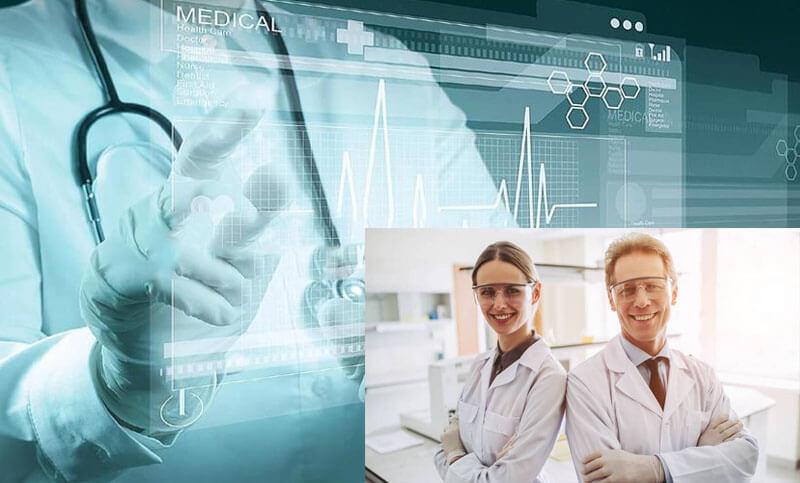
Borosilicate glass reactors have proven to be versatile and reliable tools for chemical process control. Borosilicate glass reactors’ exceptional resistance to thermal stress and chemical corrosion, combined with transparency and inertness, prove invaluable across applications. From laboratory-scale synthesis to pharmaceutical manufacturing and the petrochemical industry, these reactors enable precise control over reaction conditions and facilitate real-time observation. However, it is crucial to follow safety measures and protocols to ensure the safe and efficient operation of borosilicate glass reactors in any setting.