In the world of chemical engineering, innovation plays a crucial role in improving process efficiency, product quality, and safety standards. One such innovation that has revolutionized the industry is the glass reactor system. Combining the transparency and inertness of glass with advanced technology, these systems offer a versatile and reliable platform for a wide range of chemical reactions. In this article, we will explore the features, applications, and benefits of glass reactor systems, shedding light on their significant contributions to the field of chemical engineering.
I. Understanding Glass Reactor Systems
A. Definition and Structure
A glass reactor system serves as a laboratory apparatus for conducting chemical reactions under controlled conditions. It consists of a glass vessel, usually made of borosilicate glass, which can withstand high temperatures and chemical reactivity. The vessel includes a variety of accessories, such as stirrers, temperature probes, condensers, and pressure regulators, enabling precise control over reaction parameters. Typically, the system encloses within a jacket, enabling efficient heating or cooling of the reaction mixture.
B. Types of Glass Reactor Systems
Glass reactor systems come in various configurations to cater to different process requirements. Some common types include:
1. Batch Reactors: These systems are designed to carry out reactions in discrete batches, loading the reactants into the reactor vessel, and proceeding with the reaction until completion. Pharmaceutical synthesis, fine chemical manufacturing, and material synthesis widely use batch reactors.
2. Continuous Flow Reactors: In contrast to batch reactors, continuous flow reactors enable the continuous processing of reactants, resulting in a steady-state operation. These systems offer advantages such as improved heat transfer, enhanced control over reaction kinetics, and higher productivity. Continuous flow reactors find applications in the production of chemicals, fuels, and polymers.
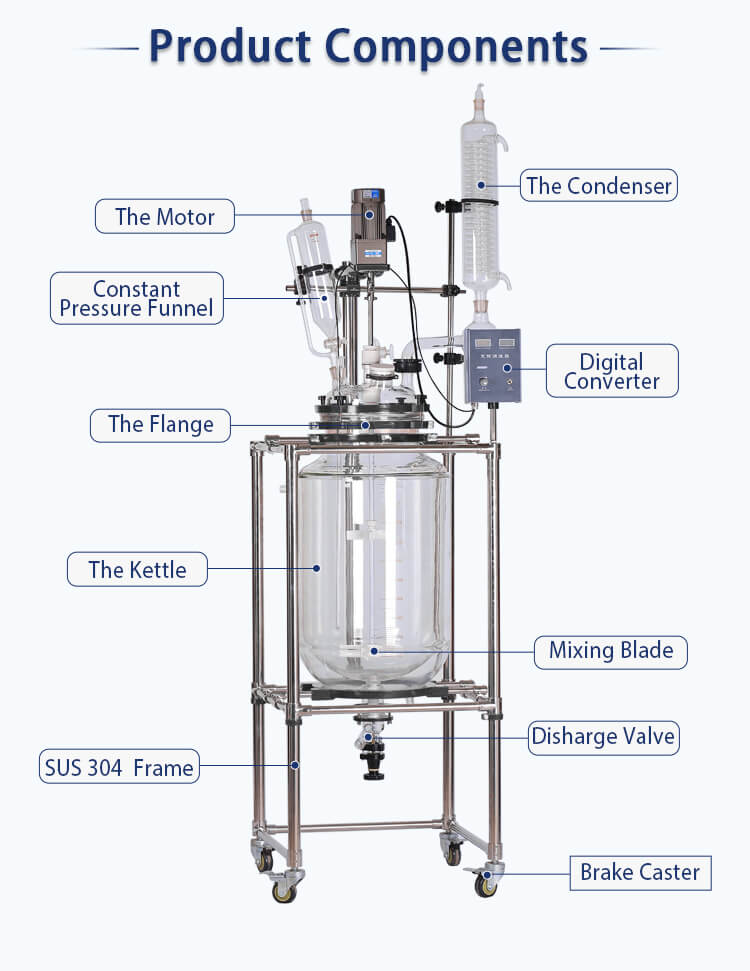
II. Applications of Glass Reactor Systems
A. Chemical Synthesis and Process Development
Glass reactor systems have found extensive applications in chemical synthesis and process development. Their versatility allows chemists to explore a wide range of reactions, from simple organic transformations to complex multi-step syntheses. The transparency of the glass vessel enables real-time observation of the reaction progress, facilitating better understanding and control. The precise control over reaction parameters, such as temperature, pressure, and stirring speed, enables optimization of reaction conditions, leading to improved yields and selectivity.
B. Crystallization Studies
Crystallization is a vital process in various industries, including pharmaceuticals, fine chemicals, and food production. Glass reactor systems are widely employed for studying and optimizing crystallization processes. The ability to control temperature, stirring rate, and solvent evaporation in these systems allows for the generation of well-defined crystal forms with desired properties. Moreover, the transparency of the glass vessel facilitates in-situ monitoring of crystal growth and morphology, aiding in process optimization and troubleshooting.
C. Hydrothermal Synthesis
Glass reactor systems are also utilized for hydrothermal synthesis, which involves chemical reactions at elevated temperatures and pressures in aqueous or solvent environments. Hydrothermal synthesis is employed in the preparation of various materials, such as nanoparticles, zeolites, and metal-organic frameworks. The robust nature of the glass reactor system enables safe operation under high-pressure conditions, while the transparency allows for real-time observation of nucleation and crystal growth processes.
Application: Synthesis of Pharmaceutical Intermediates
To illustrate the practical application of a glass reactor system, let us consider the synthesis of pharmaceutical intermediates. In this case, the reaction requires controlled heating, efficient mixing, and the ability to monitor the reaction progress. A glass reactor system equipped with a temperature-controlled jacket, magnetic stirrer, and an in-line spectroscopic probe can fulfill these requirements effectively. The chemist can monitor the reaction in real-time, make adjustments if necessary, and optimize the reaction conditions to obtain the desired intermediate in high yield and purity.
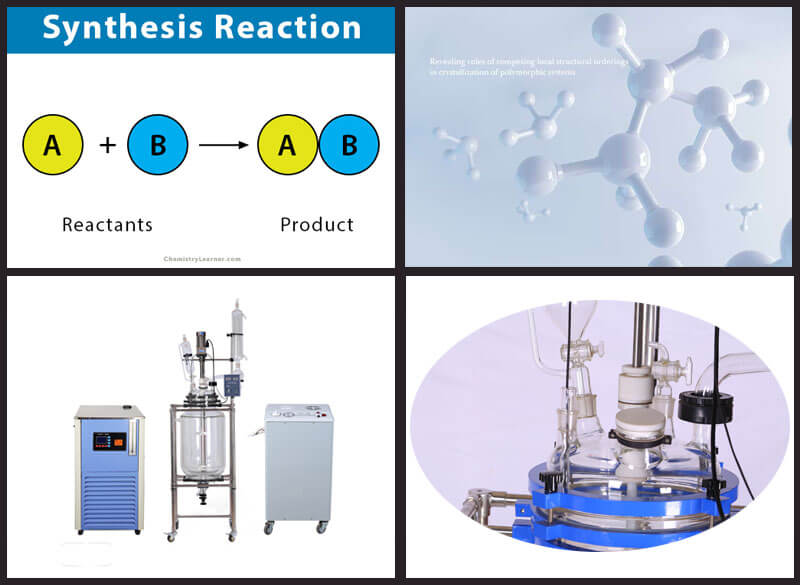
III. Benefits of Glass Reactor Systems
A. Enhanced Safety
The use of glass reactor systems offers significant safety advantages over traditional metal reactors. Glass vessels are chemically inert, reducing the risk of unwanted reactions or contamination. Additionally, the transparency of the glass allows operators to monitor the reaction visually, minimizing the chances of unexpected events such as over-pressurization or thermal runaway. In the event of any malfunction or reaction deviation, operators can take immediate corrective actions.
B. Process Intensification
Glass reactor systems enable process intensification by offering precise control over reaction parameters and allowing real-time monitoring. This facilitates the optimization of reaction conditions, leading to improved yields, reduced reaction times, and minimized waste generation. The ability to conduct reactions continuously in some systems also enhances productivity and reduces labor and material costs.
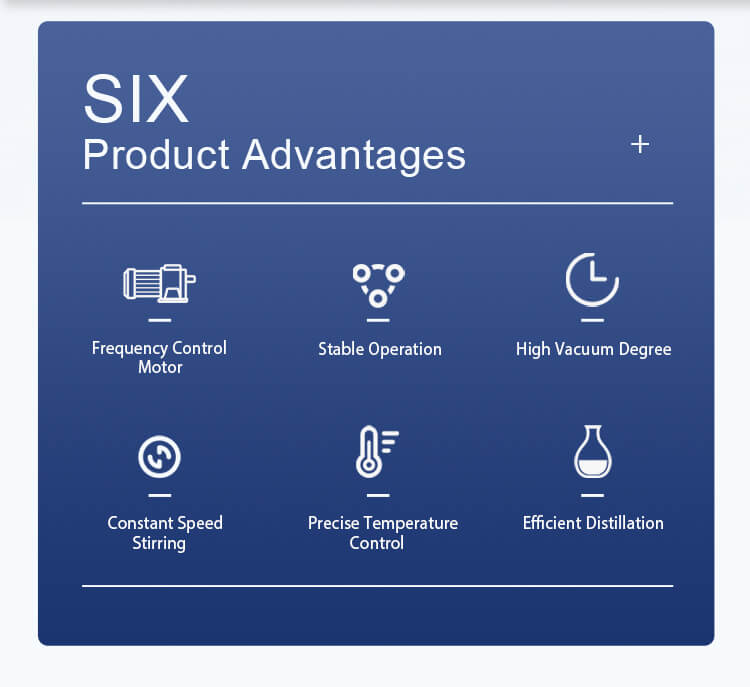
C. Flexibility and Scalability
Glass reactor systems are highly flexible and scalable, accommodating a wide range of reaction volumes. From laboratory-scale experiments to pilot plant operations, these systems can be easily adapted to different process requirements. The modular design of many glass reactor systems allows for easy interchangeability of components, facilitating customization and upgrades as needed.
Glass reactor systems have emerged as indispensable tools in the field of chemical engineering, enabling precise control, real-time monitoring, and optimization of chemical reactions. With their versatility, transparency, and enhanced safety features, these systems have found applications in various domains, including chemical synthesis, crystallization studies, and hydrothermal synthesis. As technology continues to advance, glass reactor systems are expected to play an increasingly vital role in driving innovation and progress in the chemical industry, facilitating the development of safer, more efficient, and sustainable processes.